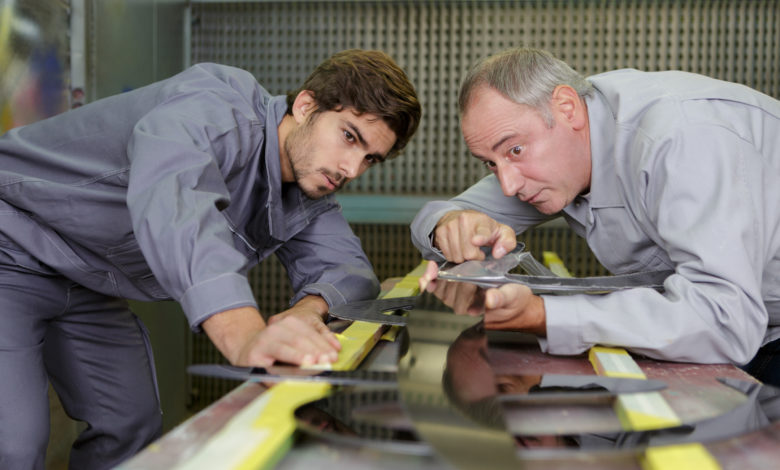
“Ohhh, my aching back!”
As a business owner and sign manufacturer, these are probably four of the most often heard words as you walk among your staff in the shop. I am sure that you have often thought, even if you didn’t say it, what a bunch of belly-aching wimps. But are they? Or, are your employees trying to tell you that the workcells they occupy are not set up to prevent repetitive stress injuries.
You may say, “Who cares? I pay them a good wage to produce a product.” You should care because lost work hours disrupt production, and insurance claims drive up your risk management costs at an alarming rate.
Taking a proactive approach to the ergonomics of workcells can save you time, money and improve employee retention. Including the employees who work in these cells in the process of developing new layouts and procedures will increase their perception of your company as a progressive employer and strengthen their level of commitment to the company.
The first step to improving a workcell is to assess how tasks are completed today. Take a few minutes and actively watch the employees as they go through their normal activities. If you tell the employees in advance what you are doing, it makes them feel more like being a participant in the process and less like they are being examined. Take notes of how often the employee has to take steps away from their workspace, how many times they have to bend over more than 15-20 degrees, and how often they have to turn to the left or right more than 20 degrees. Pay particular attention to how often they have to squeeze, twist, or apply pressure with their hands or arms.
The next step to improving workplace ergonimics in your sign shop is to sit down with your employees and discuss your observations. Ask them to give their thoughts on how moving raw materials, creating specialty storage cabinets/bins, or arranging workcell machines and work surfaces would make their work less stressful. Write down the observations from the employees and display them on a whiteboard or large tablet that can be marked up with ideas if needed. Brainstorm for a short time, no more than 30 minutes, and come up with a plan.
Once you have the plan, you can analyze the individual points and decide if they are feasible economically and logistically. Will the plan require new machinery, new storage containers, or require tradespeople to move heavy objects to new locations? All of these will all come into play as you move toward implementing your plan. Once you have decided how to move forward, call another meeting of the employees to be affected and ask for feedback.
Finally, put your efforts to work. Implement the plan and involve the workers in the implementation process. Keep them in touch with the process, so they commit to its success. Don’t forget to review the process in a few months to ensure the new designs and procedures are actually succeeding and make adjustments if needed. The change could be just what the doctor ordered.