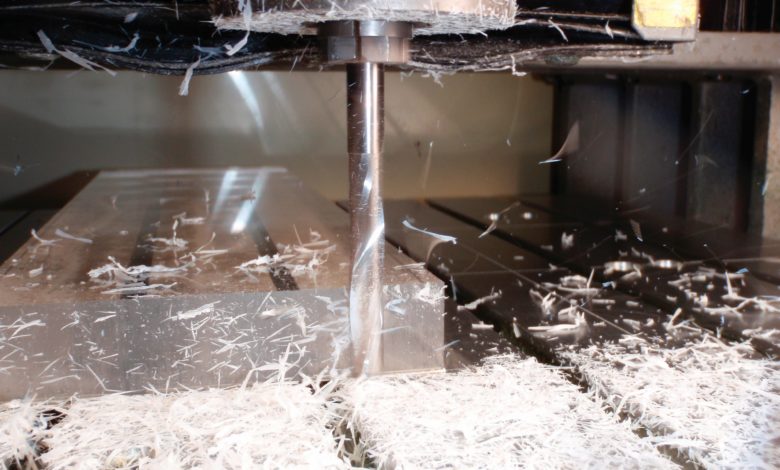
Basic features: Digital finishing systems vs. CNC routers
Both CNC routers and CNC digital finishing systems have “knife cutting capabilities and routing capabilities,” says Russell Boudria, Multicam. Shops wanting to get into this side of the business should look at the types of substrates they want to cut before making their decision.
If the shop wants to cut sheet material, dense, hard, or raw materials, they will want to purchase a CNC router machine. If the bulk of the shop’s intended applications involve knife cutting materials, especially roll-to-roll, textiles, vinyl, and banner material, they should purchase a digital finishing machine, Boudria advises.
Chuck Donaldson, Antares Inc., agrees, saying that it is “the materials driving the industry more than the equipment.” Antares manufactures cutting tools that are used for engraving, sign, and mold making on both CNC machines and engravers. The biggest difference between engraving tools and tools for a CNC is the length of the tool.
“CNCs have better spindles than engraving machines, a tighter hold, and they turn faster,” explains Donaldson. “CNCs have become higher in precision, in speed, and volume and output than engraving machines — that is why people are spending three times more for a CNC than an engraver.”
The material on the machine dictates what tool is used to cut it or what the customer wants the end product to look like. “If a customer wants bigger products, larger format, or multiple copies …. a CNC is certainly going to make life easier,” Donaldson says.
A business must balance what it wants to use a CNC for versus the space available in its shop. Another consideration is that CNCs use a higher voltage than smaller engravers or digital finishing systems.
Applications: Digital finishing systems vs. CNC routers
Digital finishing systems can produce point-of-purchase displays and outdoor signage, but there has been “tremendous growth in interior design with wallpaper, pillows, and upholstery,” says Mark Packman, also of Multicam. ADA signage, clothing, and textiles are also in huge demand, so it’s important that shops that want to get into these markets invest in the right cutting system for their product line.
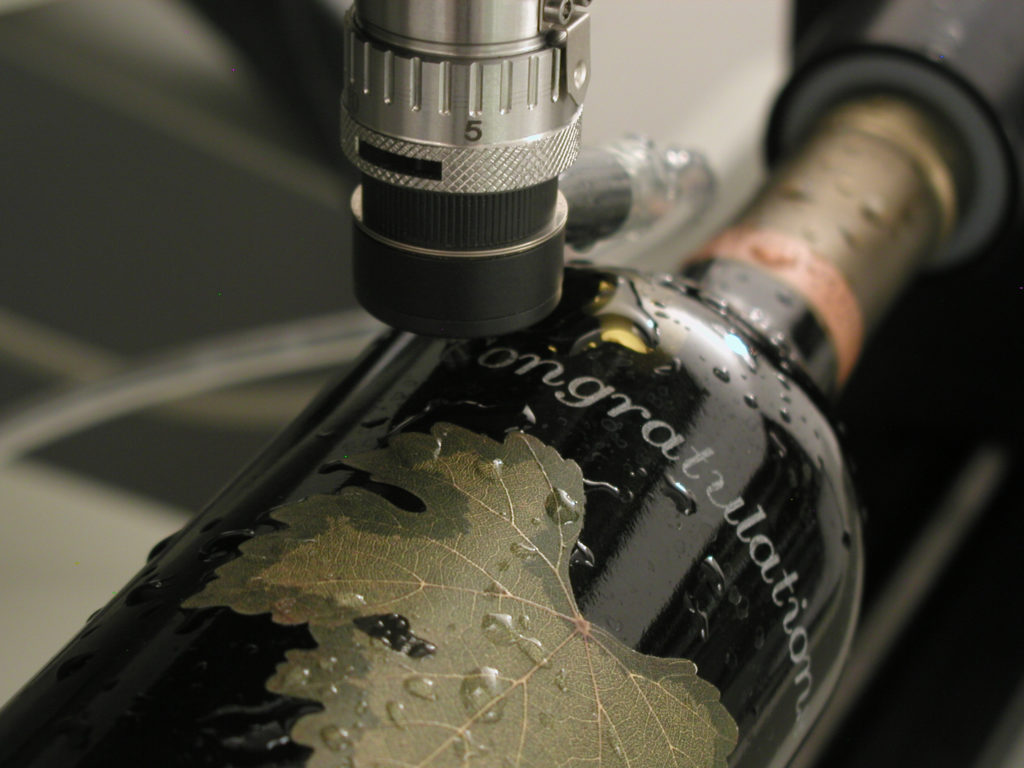
“For digital finishing, styrene, foam core, thin paper products, corrugate for packaging, rubber, or foam insulation board — if you are doing all that — the majority of your business should be digital finishing,” says Packman. “The speed of knife cutting is faster on a digital finishing system.” To cut through wood, non-ferrous metals, thicker aluminum, and composite materials, shops should look at a CNC with a larger spindle on it, he adds.
“The beauty of the grand format and CNC marketplace has to do with invention — daily invention of new substrates,” says Packman. “That allows you to be much more creative with what you can manufacture. There is daily new product development for our industry. It is fantastic.”
Technological advances in the grand-format printing industry have put some pressure on shops’ ability to keep up when it comes to cutting. Instead of the print side of the shop being the bottleneck, now it is the cutting side. That’s why Multicam believes it’s seeing more customers purchasing more than one cutting system. Many are buying CNC routers and digital finishing systems or more than one of each type of machine to keep up with the speed of the printers.
“There are so many markets out there, it is amazing to see what our customers bring to us to help them with,” says Boudria. “We’ve seen everything from making train batteries to shipbuilding, (and) cabinet shops to channel letters. It is amazing the products we’re involved with and get to help make.”
CAMaster’s industrial CNC router can also act as a digital finisher, says Cody Smith of CAMaster. “We provide versatility for the customer. They can do aluminum dimensional letters but then on the same machine could direct print vinyl and cut out decals with the oscillating knife.”
Cesare Magnani, Biesse, adds that most CNC routers can cut a variety of different materials from typical plastics like acrylic, polypropylene, and polyethylene to more dense materials like foam, aluminum, non-ferrous metals like bronze, wood, and composites. That means that shops can use their routers to cut out small components, machinery parts, covers or tops, and structural elements.
CNC machines have drag knives and oscillating knives as well as routing bits for carving. “We can not only work with a 3-axis machine carving vertically, but we have 4- and 5-axis solutions they can take to a different level of carving. They not only work vertically but inclined also. It has been a revolution. The machines today are not only more powerful but more affordable than they used to be. They have more capabilities and many different sizes,” Magnani says.
In the past, routers came with a 4′ X 4′ table, then 4′ X 8′, and then 5′ X 12′. Now there are huge machines — up to 7′ X 40′ — depending on the application.