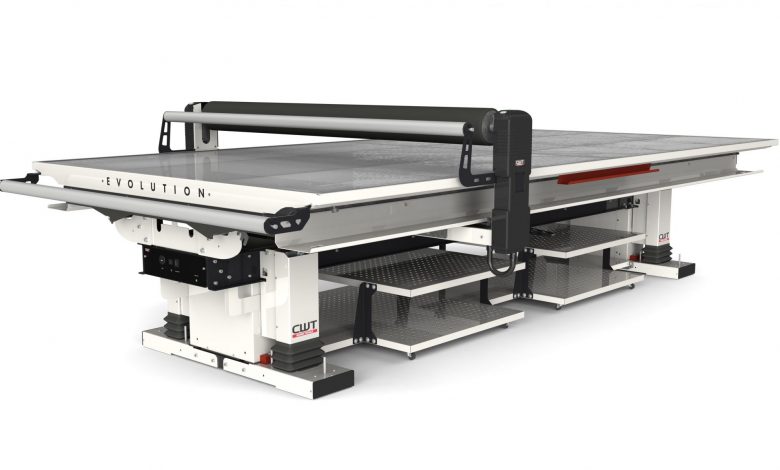
Production tables, worktables or finishing tables, are a critical part of any sign or graphics shop. They allow shops to trim prints, weed vinyl letters and complete the lamination process.
Most tables haven’t changed much in the past decade, but most manufacturers say that certain features are a must when shops consider purchasing one.
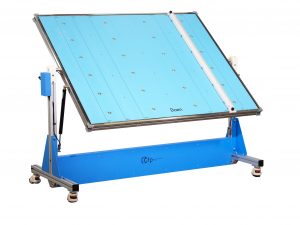
“A worktable is especially needed by wide-format printers who routinely handle oversized prints and long graphic output,” says Mitch Noble, marketing consultant with Graphic Finishing Partners, LLC, in Maryland Heights, Missouri. “The problem becomes floor space for many production and sign shops. After installing the computer, plotter, printer and, of course, laminator, there is little room for a table big enough to layout the wide-format jobs. Yet nearly every shop has a table of some kind and they are forced to arrange their equipment around it.”
Many shops build their own out of wood so they can mount any surface they want on top of it. Other finishing tables are so large that smaller shops wouldn’t even be able to consider them.
Graphic Finishing Partners recently introduced a portable finishing table called the Gfp FT 60 Finishing Table that combines a 60” wide by 48” deep roller ball transfer table with a cutting surface, both in one space-saving accessory. One side of the table can be used for feeding any laminator and the reverse side is used for trimming digital prints and sheet goods or weeding vinyl. The table folds 90 degrees and rolls away for easy storage when it isn’t in use.
“It is perfect for small printers, sign shops, framers, photographers and designers,” Noble says.
Noble says he doesn’t understand why anyone would purchase a flatbed applicator.
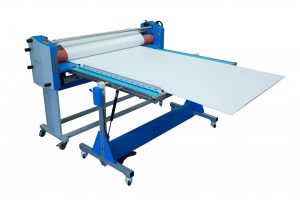
“They are so manual, which is great if you are doing one board or one sheet,” he says. “When you start doing multiple applicator jobs it doesn’t make sense. It is so labor intensive and then you have this big honking table in the middle of stuff. Some are 9’ long right in the middle of your shop.”
Having a portable worktable allows a shop to get it out of the way when it isn’t needed at a “fraction of the cost of flatbed applicators,” he says.
The Gfp FT 60 Finishing Table has roller balls half embedded in the surface, which makes moving product across it a lot easier, he says. Side guides help a shop be more accurate in lining up its prints with the lamination film. The reverse side of the table has a self-healing cutting mat that is backlit.
“Another nice thing about it is it ships flat,” Noble says. Most flatbed applicators are big, hard to get through doors and weigh a ton.
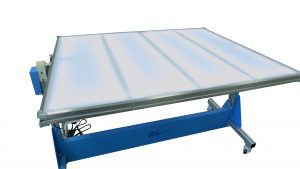
He adds that in a production environment, The Gfp FT 60 is an “economical alternative to expensive flatbed applicators. One finishing table at the front and one at the rear of any roll laminator provides continuous workflow at a fraction of the cost of today’s expensive flatbed applicators. You get the convenience and ease of continuously feeding boards or sheets up to 5’ x 10’, plus the advantages of high-speed lamination from the roll laminator … and a cutting surface for trimming.”
Joe Cutrone, North American sales manager for Rollsroller, says that his company was the first to design a finishing table in the 1990s. Nobody else was in this business until about six years ago, he says. Now there are a plethora of competitors from Sweden, Holland and Germany, but the basic application remains the same.
The Rollsroller puts down pressure between the vinyl and the substrate. “That’s the gist and heart of any system,” Cutrone says.
The Rollsroller has a heated roller that works well with cold lamination. It can prevent the silvering that occurs with cold lamination. Just a little bit of heat can get rid of those little silver specks quickly instead of having to wait for a few hours or a whole day for them to dissipate on their own.
Another key feature of the Rollsroller is an anti-static system.
“We’re unique on that,” says Cutrone, adding that the anti-static system can be mounted to the glide beam, which helps when a shop produces things like film on acrylic where there is a lot of static in the actual materials.
Cutrone believes there is a huge value proposition in purchasing a flatbed applicator, no matter where it is used. It is particularly helpful for shops that are investing $100,000 for a flatbed printer and they need a really good, fast roll device.
Rollsroller offers a return on investment calculator on its website where shops can plug in the numbers to see if purchasing a flatbed applicator makes sense.
To compete in the portable finishing table market, Rollsroller recently introduced the Roll-X system, which can turn at a 90-degree angle and go through a 45-inch doorway. It is welded steel and fully assembled, he says.
The best feature of its finishing tables is its construction, Cutrone says. The tables are welded steel with a traverse glide beam and anti-static system.
“Quite frankly, I don’t think anybody else has that feature,” he says. The tables also feature adjustable height and heated rollers.
The company can also install a second beam on the table if required. That means that on an 18’ table, two operators could be working on the table at the same time.
Rollsroller can also make finishing tables in custom sizes. The largest table is 10’ wide by 40’ long.
Kala Finishing Systems’ Kala AppliKator has a roller made of high-resistance silicon, not rubber, so that adhesive material won’t stick to its surface for easier operation and less waste, says Frank Romanello, vice president of sales for Kala Finishing Systems.
One of the unique features of the Kala AppliKator is its roller elevation system where pressure on the roller is provided by rapid action motors located on both sides of the machine.
“This unique elevation system includes a safety laser sensor that detects the media or any obstacle and slows down before touching the substrate. The roller lands smoothly on the surface, including the most fragile materials like foam centered boards,” he says.
Kala’s finishing table is a modular design, meaning that shops can make it as long or as short as they want just by adding sections or taking them away. Because of its modular construction, it is cheaper to ship.
It comes with a PVC cutting mat that covers the entire surface of the table and it is antistatic and phthalate free.
The Kala AppliKator uses the same 65” shaft that is used on the Kala 1650 laminator or KalaXY automatic trimmer. If a client already has one of the other two machines, it offers “significant time saving in handling your rolls of media from one finishing stage to another,” Romanello says.
The table also offers three pressure settings, low, medium and high to reproduce consistent quality without guessing and relying on the pressure provided by the compressor itself. An added feature of the table is its detection laser which slows the roller’s downward cycle, minimizing the operator’s risk of having their fingers or hands trapped under the roller’s pressure.
“If the pressure adjustment button is released prior to achieving full pressure the roller goes up instantly,” Romanello says.