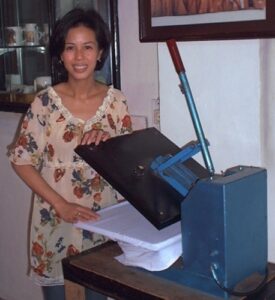
Mechanical heat presses for textile transfer applications have existed since the ‘60s. The first presses did not have today’s bells and whistles but satisfied the needs of that time. They did what a household iron could not do: provide equal and even pressure and temperature for a specific amount of time over the entire surface of the design to be transferred.
Today’s presses have changed quite a bit from their original design. Most are driven by a ubiquitous touchscreen electronic controller with digital read-out and control over all functions of the transfer process. This evolution made the machine more user-friendly and intuitive to operate, but this also came with a higher production cost and price tag.
The functionality of a heat press has also improved because of market demand from various applications. Today’s press can no longer pass the bar with a simple 12-second plastisol application but instead needs to auto-open, hover, replace its lowers, split the shirt, move sideways, double up, roll out, etc.
Aesthetically, heat presses have also moved along with the fashion (and color) of the day — recognizing that although they don’t have to win the beauty parade, functional tools need to come across as pleasing to the eye and user-friendly.
Even so, heat presses still need to first pass their functional muster and “prove their mettle.” Without meeting those basic requirements, a dead press still functions great as a boat anchor, but not much else.
Basic requirements of a heat press
The heat press is the most important component in a production setup. This tool is the catalyst for the image transfer onto the final substrate. Applications may vary, from traditional plastisol to flock, vinyl, rhinestone transfers, DTG curing, or sublimation projects. In each case, variations in time, temperature, and pressure are required to print on a variety of blank substrates currently available to the transfer enthusiast.
When acquiring a heat press, here are a few questions we suggest you consider:
- What type of products will you be transferring to? What size, thickness, material, and/or surface type?
- What type of press is best suited for your application — and why?
- What size press is best suited for your project?
- What is your anticipated volume?
- Will you be doing one-of-a-kind products or large-run production?
- Are you purchasing your press from a reliable company with reliable (and preferable in-country) after-sales service?
The heat press must provide accurate, reproducible heat and consistent pressure at every point of the platen, as well as sustain a precise time in a reliable, repeatable, and durable manner. These are the minimum requirements, but let’s break these down a little further.
Heat delivery
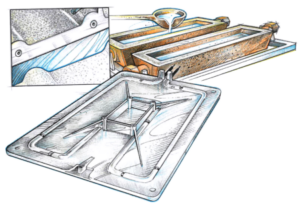
Your heat press should feature an ambient to 400 F capability to be adequate for all applications. Some recent low-temperature applications require a temperature of 230-260 F, with flock designs between 320-340 F, vinyl around 320 F, traditional plastisol transfer around 325 F, and rhinestone transfers around 350 F. Sublimation begins at lower temperatures but speeds up exponentially with increased temperatures. Ideal sublimation temperatures are between 350-400 F. Your heat press should be able to deliver these temperatures on a consistent and accurate basis.
Even more important than accurate heat is the availability of even or uniform heat. This requires a heat platen without cold spots. The best heat presses will have heating rods embedded into, rather than attached to, the surface of the heat casting. Embedding the heating rods needs to happen in a foundry where aluminum is poured into a cast containing the heating rods. As such, the heating element is permanently and firmly embedded and can provide consistent heat over the entire platen surface.
Pressure
Some applications require light pressure, some medium, and some very strong. Regardless of the pressure requirement, the press should have adjustable pressure controls and be able to deliver from 20-80 PSI per equivalent line pressure force to cover projects such as plastisol prints, hot or cold peel transfers, foils, flock, or rhinestone transfers, etc.
Manual presses have no air pressure gauge but should have a lever or knob to allow for increasing or decreasing the pressure. A digital readout (e.g., 1-9) on a manual press is helpful to indicate the level of pressure applied.
When dealing with heat, even and uniform pressure is more important than the amount of pressure. Uneven pressure has a similar effect on the substrate as does uneven heat, showing some areas of the product insufficiently transferred or sublimated. The secret of even pressure lies in the proper construction of the press, with both platens evenly closing over the entire surface. It also lies in the proper finishing of the heat casting — being perfectly flat, even at high temperatures.
And finally, there is also the importance of the lower pad. Low-quality pads, torn silicone, or weaknesses or bubbles on or below its surface will result in lower and/or lost pressure at those spots, with a negative effect on the product.
Time consideration

Most presses have built-in timers that alert the user when the required dwell time has been reached. Some presses, called air-automatic, semi-automatic, or auto-release presses, have release mechanisms that will automatically open when the set dwell time has elapsed. This is convenient for an operator monitoring several projects at once.
Analog presses are mostly a scaled-down version of their higher-end cousins. To remain within the budget of the start-up shop, these presses may not have integrated timers or temperature/pressure read-outs but may have included stick-on timers.
Although there may not always be an immediate correlation between the quality of the press and the presence or absence of integrated and automatic controls, other than convenience, often these analog presses are also built for smaller production environments and constructed accordingly, with a reduced life expectancy.
Size consideration
Heat castings must be at least 1″ larger on all four sides than the desired image or transfer surface of the substrate. Good quality presses with high-quality pads can allow for an even narrower ½” distance from the edge of the pad. Any closer to the corner of the pad results in a quick drop of pressure.
So, if your intention is to print on 11″ X 14″ Chromaluxe plate and 13″ X 13″ polyester bags, a good quality 15″ X 15″ press will do the job. For larger projects, better pick a press with a larger platen such as a 16″ X 20″ (which covers most standard-size transfers available on the market), a 20″ X 25″ (which covers oversize transfers as well as larger, non-textile substrates), or even a large-format 44″ X 64″ (e.g., to cover a 40″ X 60″ Chromaluxe aluminum plate).
Heat presses cannot accommodate substrates or transfers that are larger than the press’s transfer surface. Printing any substrate in two takes simply is not an option. This makes your selection of size a determining factor in the type of projects you can accomplish.
Another measure to consider is the maximum platen clearance — as measured by the distance between the upper and lower platen with the heat press in the closed position. A heat press can only handle substrates thinner than this maximum clearance between platens.
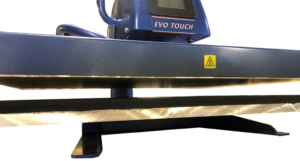
Sufficient clearance between the platen allows the press to “hover” above the surface of the lower without touching it. This adds functionality to the press as it will then be able to cure ink without touching the fabric, leaving it with a soft screen printed-like feel. This can then be used for direct-to-garment curing.
Heat recovery time
A further consideration for those interested in mass production is the heat recovery time — defined as the ability of a press to return to its set temperature at the end of the cycle. This recovery time is directly related to the type and quality of the press’s electrical components. Higher wattage heaters have quicker heat recovery. For example, a 2,000-watt heat casting will recover its heat a little quicker than that same press with a 1,750-watt heater. Similarly, an 8,000-watt sublimation oven, once the oven door has been closed, will recover its temperature quicker than a 5,000-watt oven.
Cantilever construction
A final consideration should be the ease at which a shirt or other textile product can be placed on the lower platen, exposing only the print side to the heat.
This is particularly useful when using your press for sublimation projects. To safely sublimate on shirts, hoodies, jackets, bags, or other two-sided textile products, it is important to only expose the printed side to heat and pressure. Laying the entire product on the press risks the sublimation inks migrating — not just to the top of the substrate but also to the inside and even the backside.
Remember, sublimation inks turn into a gas before they are trapped by a polymer. Gas does not discriminate between the front, inside, or back of a shirt. Imagine the ink gasses as a smoke cloud expanding from the transfer and attaching to whatever synthetic fiber they encounter first.
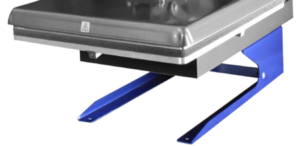
Another application for a cantilever heat press is garments with lots of buttons and zippers. Even when printing on the reverse side of these garments (away from all these obstructions), it will be much easier to transfer on one side of the garment while keeping the side with buttons and zippers safely away from the platen and draped below the press.
Most presses will have insufficient clearance below the base to pull any garment or bag over and around the base. As a remedy for this lack of clearance, the operator can also insert a Teflon sheet or cushion, or even some brown craft paper, in between the fabric layers. However, this takes additional preparation time and may not always work.
A cantilever press allows full clearance below the machine’s base and a safe and clean space for the back of the garment away from heat, pressure, and errant sublimation ink gasses.
Going forward
As modern heat presses continue to evolve to meet the versatility demands of the market, it is important to remember these simple yet pertinent basic requirements. Your choice can sometimes come down to the main projects the press is intended to be used for, how the machine fits into your workflow, and other needs. The choice is yours, and by knowing these basic requirements, you’ll be sure to find the right press.