I caught myself looking out of my workshop window and literally watching the grass grow. I had just closed my heat press on the umpteenth performance shirt I needed to deliver to a running club by tomorrow. I had already established that the ideal dwell time for my sublimated shirt design was 1 minute and 15 seconds, or about 1 minute longer than my patience, which was growing thinner by the minute as the sun was already setting behind the Ozarks. This was when I knew I had to either change my heat press or the way of working with the one I had.
My choices seemed straightforward: buy another press (easy) and get someone else to help me (harder). Am I really the first one to face this dilemma?
A quick search resulted in a number of solutions to my operational bottleneck. Turns out there are several options available to me other than adding more labor and equipment. Most heat presses offer replaceable lowers, but that really doesn’t help me out. However, some offer accessories that double a customer’s output. I was all ears.
Here is what I found and the solutions I am now considering.
Shuttle-style presses
Shuttle-style presses can be seen as a variation (or duplication) of a clamshell press. With the shuttle style, the press opens up not just over the original, single lower platen but moves onto and over the next lower station in a side-to-side sliding movement.
Presses exist in two variations: either the upper heat head moves left to right between both fixed lowers, or the heat head remains fixed with the lowers moving on a shuttle system left to right. The mechanics are a bit different in each case, but the result is the same: the operator virtually doubles their output capacity by working on alternating lowers while the press cycles through the timed compression, moving between one and the other lower.
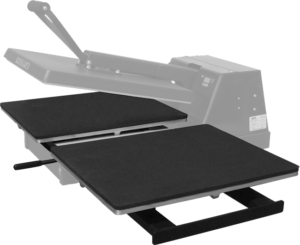
Moveable lowers
Some single-head presses can be expanded into a shuttle system by adding a second lower as part of a shuttle assembly. The assembly may come as a construction kit to be assembled by the customer. If so, the customer can add this accessory at a later time, after the purchase of the machine, if and when his production requires it.
The construction kit mostly consists of a rail system that carries both lower platens, allowing those to move from side to side. The closing pressure is carried by the assembly system, which needs to be sufficiently strong to support that pressure.
Movable upper platens
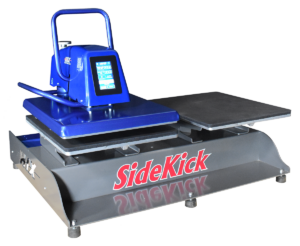
In this case, the upper heat casting with control housing moves left-to-right-to-left with the lowers permanently fixed onto the base of the machine.
In this case, with the upper head moving, the heat head’s rail assembly, located behind the press, can be simple and built to avoid carrying any major clamping pressure. Here, the clamping pressure is absorbed completely by the steel base the press rests on.
This construction cannot be achieved in the field by the customer but, because of its complexity, needs to be completed by the manufacturer, often as an original model (not as a later attachment).
Lower platen clearance
“Clearance,” as defined here, refers to the maximum distance between the upper and lower platen with the press in the closed position. It defines the types of substrates that can possibly be handled by the press.
The downside of a lower-platen shuttle attachment may be a narrowing of clearance between the platens, making this shuttle solution suitable only for thinner projects, e.g., T-shirts or other thin fabrics. This does cover a lot of the projects these types of clamshell presses are used for in the industry but still leaves some room for an alternative shuttle press that can handle thicker textile and solid non-textile substrates such as wooden plaques.
In the case of the upper platen moving, the press retains its original clearance, often opening up more than sufficiently for any known textile or non-textile substrate, such as hoodies, jackets, sweatsuits, or thicker wooden plaques.
Cantilever lowers
“Cantilever” construction refers to the space below the lowers, allowing the operator to split every shirt. This makes it possible to print on one side of the shirt while keeping the other side below the press and away from the heat head. This is particularly handy when working with sublimation inks or when trying to stay away from buttons, zippers, and/or pockets.
With the lower-platen shuttle attachment, the cantilever is harder to achieve because the rail system, supporting the pressure and carrying the lowers, may be obstructing.
In the second solution, with the moving heat head as an original design, the construction lends itself better to a cantilever shape since, in this case, the rail system can be designed behind the press as it needs to carry no weight or pressure.
Inter-platen clearance
This refers to the space between both lowers. This needs to be designed in such a way that this clearance leaves enough room for hands and knuckles to pass through but not so far apart as to make the left-to-right movement prohibitively long.
Here both systems can accommodate this need.
Conclusion
The main advantage of a shuttle system is the time and labor savings created by not having to wait through each compression cycle. Instead, the operator simply moves on to the next project while the previous project is being pressed.
The shuttle system’s speed comes best to fruition when working with long transfer cycles. One application that requires such long cycles is sublimation. Shirts and other non-textile substrates can take one to several minutes to cycle. Having a second shirt or hard substrate to prepare while the previous one is still sublimating, together with handling and packing the previous item while the next one is already being pressed, will easily double the output per hour.
Even for substrates that require shorter cycle times — such as 8 to 12 seconds plastisol transfers — or for those that require longer cycles — such as sublimation on tiles — the savings in time are still significant.
Another advantage, depending on the type of construction, can be a cost-saving since it avoids having to purchase two presses instead of one (albeit at a somewhat higher cost).
In all, a shuttle system of either design is a perfect addition to any transfer shop and can either take the place of two older presses or be added to take on the more time-consuming plastisol/sublimation projects which may have hitherto been abandoned due to a lack of time.