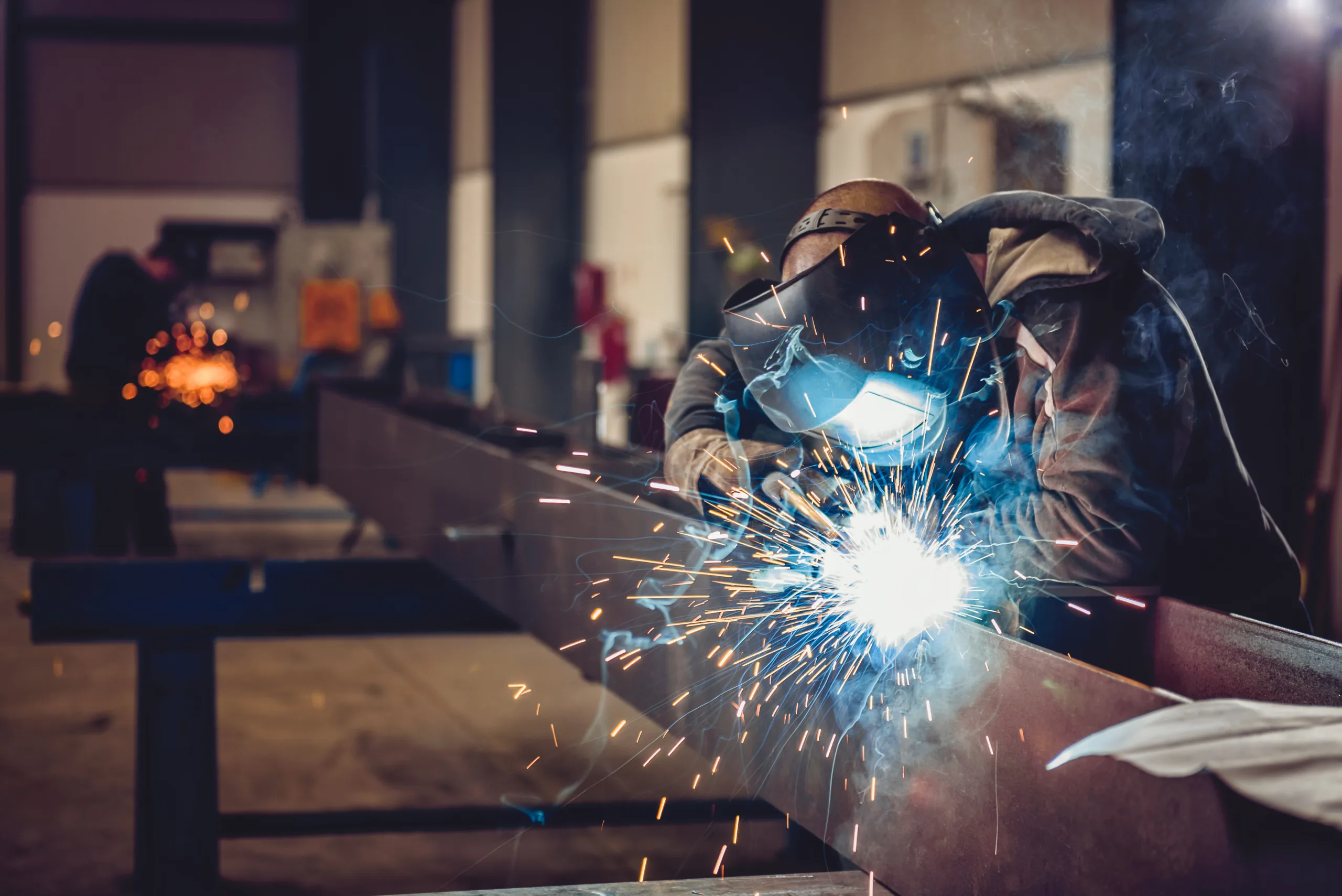
Ahhh, I remember it like it was only 15 years ago. To set the stage, envision in your mind’s-eye oversized golden harps played by chubby little cherubs with puffy white clouds that appear to be parting – opening to a daydreamy fuzzy image of days gone by.
It was the spring of 2007, and I found myself, once again, carefully planning the ultimate article topic that would impress my editor at Sign and Digital Graphics magazine. Each month it was the same struggle to make the traveling team, which was my term for getting my story published in the magazine that month. With so many seasoned writers already filling the pages, I had to be on my A-game if I wanted to even stand a chance.
It’s not as easy as it seems; I mean, sure, we see it almost daily on the social networking platforms; stories and pictures of how the contributing writers for GRAPHICS PRO Magazine are living the glam-leisure life that seems to soar past the lifestyles of the rich and famous.
Oh sure, during the initial years of writing for the magazine, it was a lot like pulling tissues out of a Kleenex box. My head was packed full of unexplored topics and story ideas that seemed to roll out of my head faster than the tongue of a diabetic in a candy store. However, as the months passed, I soon came to realize that producing sign design articles of that caliber every month was not easy.
Add to that pressure the newly realized and highly unexpected dilemma of making sure I didn’t accidentally contradict myself on a process or opinion from some previous article. I’ve come to realize that past notions, which seemed logical in nature at the time, even opinions formed from actual product failures in the field can change.
New discoveries are made, and just as I was initially nervous about the use of VHB tape (by 3M – Very High Bond adhesion product) for certain aspects of sign fabrication, I found out my fears were not valid at all. My opinion was most likely due to early versions of the product that failed, possibly due to improper surface prep, overall limitations of the tape, a host of variables I may not have considered, or that had not been discovered yet.
More on that VHB Tape topic later on in this article.
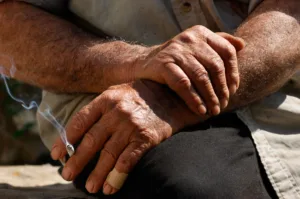
But once I learned that using it for aircraft fabrication produces a safer, stronger hold than rivets, I had to reconsider my opinion and look into it further. Not that we build many airliners, but the principles of aluminum expansion and how to make it work in your favor make that study a significant consideration for wind load calculations. And yes, it turns out to be stronger and more versatile than I and others within my circle of sign professionals had presumed. I mean, quite frankly; this one made me think of a lot of areas that I may have considered as set in stone.
Now back to the article. I had an idea that I felt would help new designers improve their electric sign design projects so they could avoid fabrication and/or installation issues.
I truly felt that this was one of the most important considerations for all sign designers to pay attention to (unless being called out by fabricators and installers is something they enjoy).
After the article was published, it hit a hot button with some fabricators as I remember getting a few thumbs-ups during subsequent shop visits.
Fortunately for me, the editor way back then is the same editor I have the pleasure of working with today at GRAPHICS PRO magazine, and he has made my world easy this month because he has asked me to revisit this insightful topic. I cannot tell you how much fun this is going to be. I finally get to revamp the original article on Wrench Room to include some of the new discoveries I have made on the subject.
I must confess, I am adding in this chapter to say what an assumptive fool I have been. I really thought this second time around, the article would be so easy to write, like pulling a tissue out of a box! Nope! Not at all, and that is because there have been not just a few, but at least 1,000 or more scenarios in which I’ve said… way back in ‘07, I wrote an article about Wrench Room for designing electric signs, and blah, blah, blah, and my biggest problem is which anecdotes do I include to further expand on the subject? I’m lost in my own forest of the trees I planted in my own brain! I am at least two days late to meet the deadline, and my incredibly understanding and almost Gumby-like Editor for being so flexible with a brain like mine that’s enslaved by the strengths and challenges of A.D.D.
Wrench Room II (Wrench Room Revisited)
As an electric sign designer, you have been assigned the task of reading minds, predicting what everyone needs, and spitting it all out in no time at all and with enough forethought that it can be built under budget.
Sometimes, the last thing you naturally consider is how this will be assembled and installed — forgetting to consider this can be not only costly to correct, it can create an unsafe situation in the field.
I appreciate your wading through my introduction as it allows me to get to the meat of this article without all the previous articles’ scenario setups, so here we go!
Wrench room
The area, space, and or clearance provided by design for the fabricator and installers to reach, connect to, weld, screw to, fasten, attach, and adjust all the components of the electric sign, all the while remembering and adhering to UL guidelines.
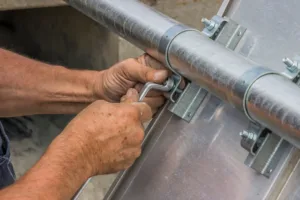
Fabricators’ and installers’ hands
Have you ever shaken the hand of an electric sign frame fabricator or pylon/monument installer? Male or female, the differences are instantly noticeable. Rough, calloused, strong, and larger than the hand of the average person who isn’t using them daily to lift and steady a 100-lb piece of I-beam while it’s being welded in place.
Cold, heat, wind
Sure, you may say that working conditions are not much fun but are part of the job. So, as designers, we have the opportunity to help the situation by paying attention to things like reach. How far does the service tech need to reach into the sign cabinet to get the wrench onto the bolt? What if the cabinet is black, it’s downtown Houston, in July, with 100-degree temps. The length of time it takes to be inside the box in those conditions makes all the difference to the service tech alone. Be the unsung hero by placing access panels where critical attachment elements are easily reachable.
Maturity + wisdom = arthritis
Now, here is the new discovery I want to add to this visualization: the tolerance for pain. Those hands for some fabricators are also dealing with mild to severe arthritis. Holy cow, that’s a game changer when it comes to Wrench Room in cold weather. I speak from absolute authority on this subject.
When pain limits what the installer can and can’t necessarily hold, turn, or maneuver as easily as it was when they were 21, young, fast and fearless, planning for and providing Wrench Room can mean a less-painful installation process.
All of this involves looking beyond the 4 o’clock deadline to double-check that you have considered most of the things that matter the most. Paying a bit of attention to the work conditions, the challenges, and the struggles of those who actually use the files you create is not only kind, it’s cost-effective for the company. It provides happier team members, rather than grumbling disgruntles who are tired of telling them they can’t reach the saddle in that design without removing the whole face.
At the end of the day, a happy team member is what our jobs are all about as designers. (Yep, I said that!)
Wiggle room and welding room
Two of Wrench Rooms’ favorite cousins, they too are part of the Wrench Room family of fabrication considerations. Will the installers be required to weld at the job site? If so, have you provided a removable panel or panels so that the installer is not required to invent one on-site?
Heat is the killer of welding on-site, so making sure that installers can do the required welding without compromising the painted finish is absolutely vital to a profitable installation project.
Wiggle Room is what makes every fabrication and installation team member smile. Providing files that fit together with tolerances that are tighter than the specs for the door seals of the space shuttle does nothing to foster friendships in the shop. Understanding tolerances for assembly-style fabrications requires a lot of up-front communication and is one of the benefits that adequate Wrench Room can help to alleviate.
So, I mentioned VHB tape earlier in the article, and I wanted to add that the use of VHB tape can almost eliminate the attachment-connector access dilemma by creating 99% permanent bonds between materials. Planning for Wrench Room can get exponentially easier if VHB is able to be used for certain attachment challenges. Its strength is amazing when used according to its limitations.
I saw a documentary where VHB was used on aircraft aluminum, and the results were amazing and scary. Reason leads us to presume that strategically placed rivets are as strong as you can get, mechanically, other than welding. Here is a chemical that does a better job as it eliminates tears in the aluminum from the rivet hole that punctured the aluminum, creating weak points that can tear across the aluminum sheeting under extreme conditions.
I was also privy to hearing about this being used by machinists who needed a permanent bond between two pieces of titanium when welding them or tapping new attachment points could warp both surfaces. So yes, I have a new opinion on this based on new developments in research and actual use in the field. That’s what makes this industry so interesting; change is constant.