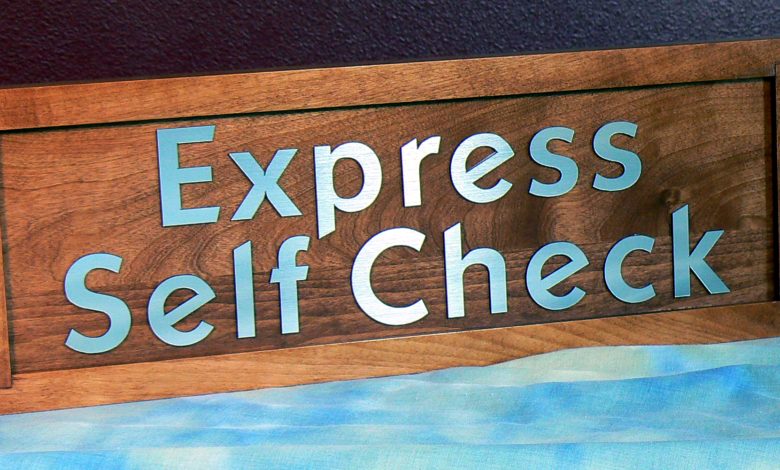
Acrylics are a type of plastic. Acrylic is typically very hard and durable. For our industry, acrylic is either manufactured with an extrusion process or is cast by pouring liquid into a cast in the shape of the product. Cast acrylic is very scratch resistant, yet metal tools will scratch it and scratches are difficult to remove. Extruded acrylic can be made thick and cut into shape. Cast acrylic can be cast into sheets. So, don’t look at a product and assume how it was made.
Extruded vs. cast acrylic
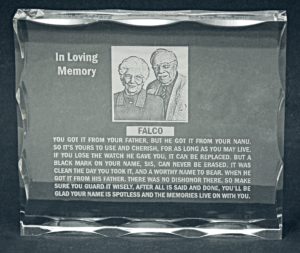
Why does it matter whether acrylic is extruded or cast? Cast acrylic laser engraves white, does not easily melt, and lasers with precise edges allowing for high resolution. It is easy to clean and holds great detail. Clear cast acrylic is very opaque and has great visual qualities.
Extruded acrylic can be cut with a laser to make letters or other shapes. Yet, if it is laser engraved, it cannot be easily read, will melt, and is not presentable. It is less expensive to manufacture.
Both types of acrylics have their uses. Buying acrylic plastic products from our industry is the safest way to make sure you have the right product for the use you have in mind. Products will typically say they are “laserable” (engravable) or can be “laser cut.”
Choosing the right product
Make sure the products are for lasering and not for print or another process. You may find acrylic plaques that are lasered from the reverse side removing a paint layer to reveal the text and graphics. Make sure you read directions and reverse your text and graphics when needed. Ruining expensive acrylic products because you rush through a job and don’t read the instructions will leave you feeling foolish and perhaps with an order that is not profitable.
Why acrylic plastic? Acrylic plastic does not give off harmful gases like some other plastics do. Polyvinyl chloride (PVC) is one of them. Lasering certain plastics can be harmful to your laser operator and other employees, as well as damage your laser and invalidate its warranty. PVC gives off chlorine which is very harmful to the body and your laser’s optics. If you laser your customer’s products, do not laser any plastic products that you cannot identify the type of plastic it is made from.
Products that appear to be leather can also be plastic and melt when lasered. I had a high school football coach bring me several footballs that he said he guaranteed were leather. They were not! Many book covers, such as bibles, have what appears to be leather covers that are made from plastic. I only made those mistakes once.
Working with sheet acrylic
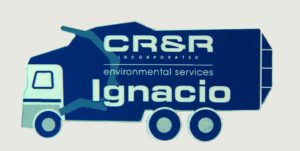
Sheet acrylic can be lasered and laser cut into your own custom products. Shapes cut from sheets is a great way to add color to a wood-based custom decorative product. There is also a very limited number of color combinations of 3-ply sheets available. It is laserable on both sides and can be used for signage that needs to be read from both the front and back sides.
Mixing acrylic laser cut from sheets with wood and even metal pieces can make for some very interesting and creative decorative products.
I sold thousands of name badges each year, mostly made from lasered sheet goods, in a variety of color combinations. They can be highly profitable, especially with repeat orders from organizations and independent business owners. The biggest challenge is getting a good quality graphic file of the logo.
Learn more about lasering and selling acrylics in the December ’21 issue of GRAPHICS PRO.