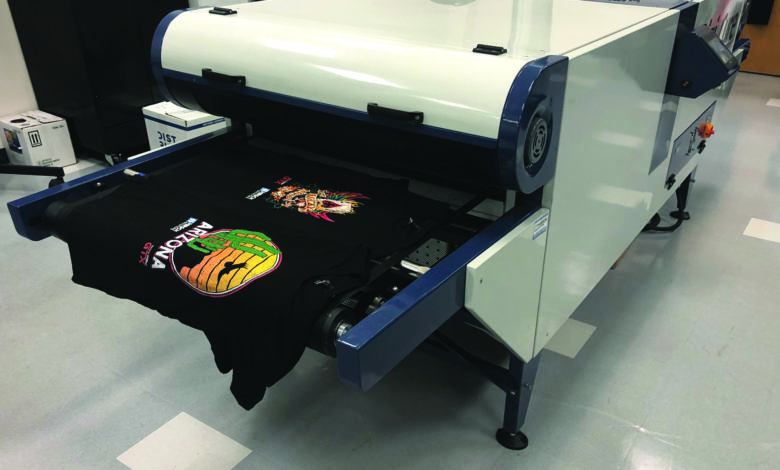
Most direct-to-garment (DTG) printers utilize a water-based ink. Water-based ink creates a smooth hand and is environmentally friendly. However, because of these characteristics, water-based ink lacks heavy opacity. This means that a color such as red that is vibrant on a white shirt will become less vibrant and visible as the garment gets darker. This also occurs on a lesser level with plastisol and screen printing, which is why screen printers lay down a white base to create colors that are vibrant on dark shirts.
The white ink, which contains titanium dioxide (for opacity), requires a pretreatment to be applied to the garment. The pretreatment serves two primary purposes.
The first is that it provides a layer for the ink to bond to, and second, it serves as a primer coat for the CMYK. The standard rule of thumb for pretreatment is to use it whenever you print on dark garments or use white ink on any color garment. Since the pretreatment creates a base layer, many DTG companies offer one suitable for all garments for that added vibrancy.
Historically, white ink is what soured many people’s opinions of the DTG process. Since it contains titanium dioxide and is a thicker consistency than CMYK, there were many issues regarding head clogging to the point where the print head was destroyed. While it is still possible to destroy a white print head in today’s DTG environment, the odds are that if you do end up destroying one that it would most likely be traced to user negligence.
One of the most important things to remember with DTG is that the market segment is still relatively new. Change has been significant, but the early days are still fresh enough in people’s minds. Following the manufacturer’s recommendation for usage and maintenance ensures that you have a smooth experience with DTG as a whole.
Once the garment is printed, the ink needs to cure. There are several ways to cure the ink. The most popular is with a heat press. The heat press uses both heat and pressure to remove the moisture from the ink and cure it. Another option for drying is a conveyor dryer. A conveyor dryer uses heat only (no pressure). The curing time is typically longer than a heat press, but due to the size of a conveyor dryer, it can handle higher volumes of work.
DTG is a great way to offer high quality, high color, low (and high) quantities, and fast turnaround. When searching for a printer, look for a brand that is designed as a production machine, offers excellent training and support, and is specifically designed to be a DTG printer. While there is a learning curve, it is easy to output incredible designs and generate revenue right from the start.
For more on DTG, check out GRAPHICS PRO’s Direct-to-Substrate Report.