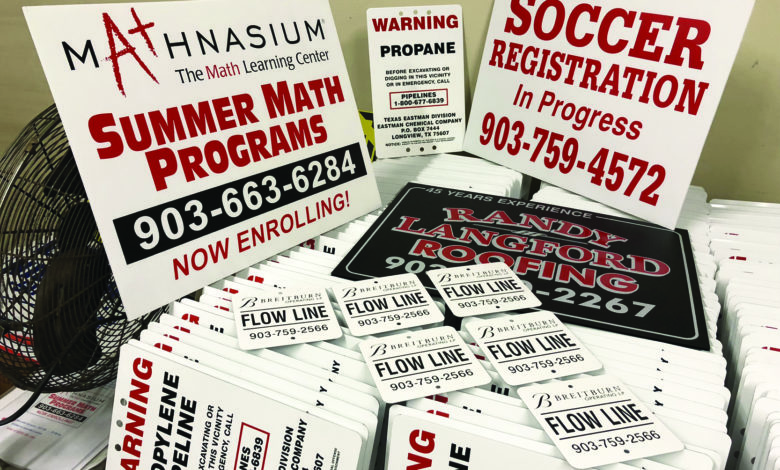
Last May, during the holiday weekend of Memorial Day, it became clear that I would not see any holiday at all. Why? Because I don’t have any local competition in a viable and demanded type of sign shop work: traditional sign shop screen printing.
In the last couple of years, we have been working only three full-time skilled sign makers at the shop, myself included. And of these three, I am the one who does virtually all the screen printing.
What had stacked up and had to be dealt with ASAP was a backlog of screen-printed jobs of all kinds. Where was my competition for this work? Again, there isn’t any.
Now, that situation isn’t because there is no demand. We’ve always had a large portion of our workload come in as screen-printed jobs, and we still do.
Of course, in the big picture, flatbed printers and digital printers of all kinds have reduced the amount of work that will likely be screen printed. That does not mean that sign shop or flat substrate screen printing is dead, or even about to be. If the longevity and outdoor durability of a print job matter, screen printing is, hands down, the winner over any digital printing. This especially applies to pre-finished metal signs, such as pipeline signs, danger, and warning signs, and so forth. They need to last and do their job for years to come, and if they are screen printed, you can depend on them doing exactly that.
Also, the speed and efficiency of simple one- or two-color screen-printing jobs in quantities of 50, 100, or more makes screen printing even short-life signs like corrugated plastic signs for contractors, political campaigns, or special events still practical and economical to be done by screening.
That weekend back in May, I found myself needing to print metal pipeline signs of different sizes, and coroplast signs for contractors, event signage for soccer season sign-ups, and more. Over that extended weekend, one man, yours truly, completed about $3,000 worth of screen-printed sign work, and I still had work yet to go.
Some people who are not very familiar with sign shop screen printing may think it’s hard to learn, inordinately messy, or just plain old fashioned. None of the above is really the case. We primarily use film positives that are just IP black vinyl applied to clear polyester sheet, which is typically the saved clear back sheet from the rolls of capillary direct film we use for our photo stencils. The vast majority of our screens are exposed outside since our lightbox is underpowered and really not large enough. The process is fast, simple, and free.
Our screens are aluminum framed, and we have them professionally stretched by a vendor a few miles away. They are re-used probably 50 times before the mess needs replacing, which is very cost-effective, as are the inks that we use.
When printing on metal, we use an air-dry enamel ink and let the ink cure a couple of days before boxing up a job. We use an all-purpose screen-printing ink with a catalyst for printing on fluted plastic, which does a great job and does not dry excessively fast. The same type of ink can be used on vinyl and some plastics.
Only a few of our screen jobs are actually printed by hand, though. We have an M&R Saturn 25/38 clamshell press for 20 years or more and get a lot of use out of it. Machines like that are available new but can also be purchased used from $5,000 to $10,000, typically found online, and if in good working condition, a used unit like ours will be well worth the price.
That weekend, I burned stencils in multiple screens, made sure my pipeline sign blanks were cut and punched, and figured a game plan that would not overwhelm my screen print work area. The metal signs, several hundred, would have to stay in drying racks for a while, but the fluted plastic signs would dry quickly and could be boxed up after a few hours.
Our dying racks are all basically homemade. For drying metal pipeline and safety signs, a collection of 4′ L pieces of 2X4 with multiple grooves cut in them with a radial saw have been drying our smaller-sized metal signs for decades.
Standard 18″ X 24″ corrugated plastic signs go in a set of drying racks I had my dad make from scraps of MDO, finish nails, and small strips of fluted plastic. This drying rack system, which holds more than 100 signs, is also shown in the photos above. I have another metal version of this rack for drying corrugated plastic signs, which is on castors and is pulled from storage whenever needed.
So, for many years we have offered in-house screen-printed sign work to our clients, and we have a modest investment in the equipment needed to do this type of job and have never run out of work to do. It is just a part of our commercial sign business, but it has been a reasonably consistent part for a very long time.
I am putting out the message that there is plenty of this work to do and a few sign makers who are skilled and equipped to do it. That’s certainly the case here in our backyard, but I would not be surprised if it is the case in other markets too. Smells like an opportunity to me.
After all, why should I, and other old sign guys be doing all this work? I have to believe there are young folks out there who would do well to add to their skills and capabilities and take advantage of the many sign jobs that even today are really best done by screen printing, something traditional sign makers have been doing for a very long time—and the pay is not bad either.