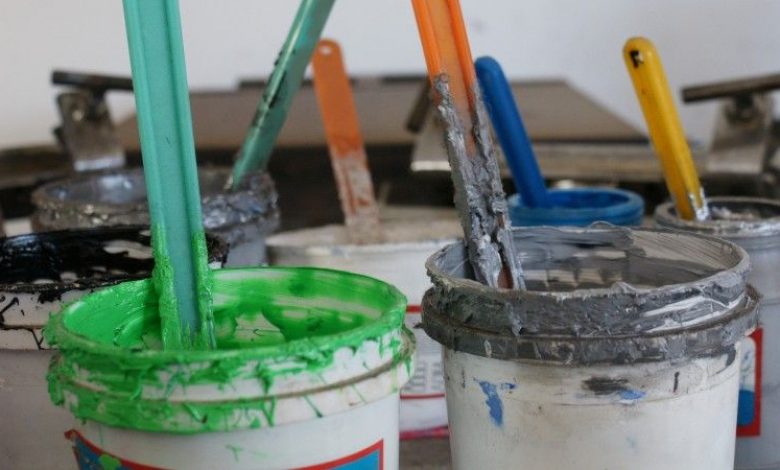
1. Use an infrared flash vs. coiled resistance heater: Infrared panels offer more consistent heat across the entire panel, minimizing the chances of cool spots. They also tend to output more thermal energy, resulting in a faster cure and more resistance to impact from the environment.
2. Use a flash with adjustable temp control and do not run it on high: Always run at least a half notch or more down from the highest maximum setting. These controls work by regulating the voltage going into the flash cure. By setting this as directed, you will minimize temperature fluctuations due to voltage fluctuations throughout the day.
3. Be wary of extension cords: Mainly if you are using one not rated for your flash cure. For example, the most common heavyweight extension cords sold at any hardware store are 120V 15-amp. If you have a 17-amp flash and you use the incorrect cord, your flash cure will not be getting enough power/amperage to operate at maximum temperature. This amperage gap can slow down production and also magnify any variances in power in your building, causing your temperature to fluctuate. The longer the extension cord, the less amperage will arrive in your flash cure. So, a 20-foot extension cord will increase your chances of temperature fluctuations.
Learn more: 7 Deadly Sins of Curing Plastisol Ink with a Flash Cure