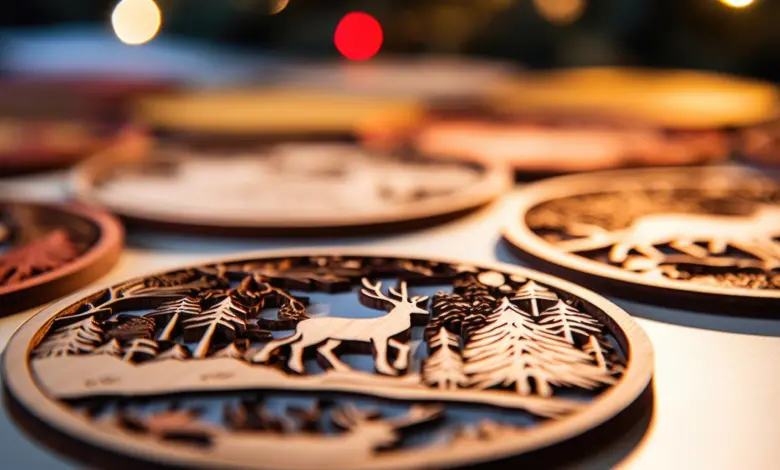
I don’t know whether it is because my dad was a genius with wood or not (he once built a garage in an upstairs bedroom, as well as almost every cabinet, display case, trunk, and more in our house — all with hand tools), but I find working with wood to be my favorite process on my machines. I could never come anywhere close to his level of skill, so I take pleasure in my laser work.
Whether you’re using hardwood, softwood, or specialty wood — and whether you’re engraving and/or fabricating — the opportunities are virtually limitless. Although different types of wood all have different characteristics, the basic operating principles apply. Together with your graphics software, you can create a myriad of shades, textures, and shapes to make your pieces stand out.
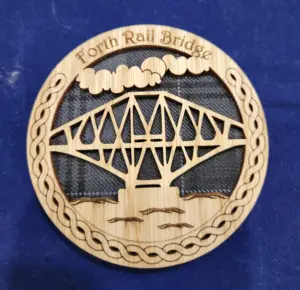
The list of products you can produce will be as long as you want, and there are opportunities to create added value to pieces supplied by your customers. As always, settings are going to depend on both your machine as well as your own preferences.
I almost always work with medium woods, such as alder, but I also like working with hardwoods, such as maple, cherry, and mahogany. I’ve also tried my hand with specialty woods, such as purpleheart. Softwoods like basswood and balsa have produced great results, too. Basswood is an example of a wood that just can’t seem to make up its mind. American basswood is considered a hardwood species, although its sapwood is very soft. And then there is wood that isn’t actually wood. Technically, bamboo is a grass, but when it has been shredded and then bonded, it produces a material that behaves like hardwood.
I’ll start with the more popular pieces I’m asked to produce: plaques for awards or special occasions. For cost reasons, I’ll usually opt for red alder for these projects. It’s a pretty consistent wood, relatively inexpensive, and good to work with overall. Once you figure out your best settings for what you want to produce, it’s easy to set up and run. Due to a fairly fine and consistent grain, it’s very amenable for shading and texturing. I also use alder sheet stock for things like ornaments, awards, and the like.
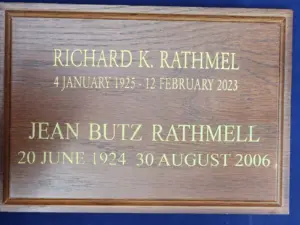
This article details a couple of things I’ve learned over the years that may help you enhance your pieces. I create the graphic, and then run a first pass at a slightly reduced power and speed. I then adjust my focus so that the piece is closer to the lens and run a second pass. This creates a slightly 3D effect enhancing the graphic. I’m also frequently asked to add things to a standard plaque, such as challenge coins. For the coin recess, use an outline thickness of 1.5 points. I’ve found that it doesn’t pay to try and get the coin flush to the surface of the plaque. You start to get into the glued areas where the plaque has been assembled, which creates a very inconsistent base. Two passes — rarely a third — are enough to seat the coin and keep it level.
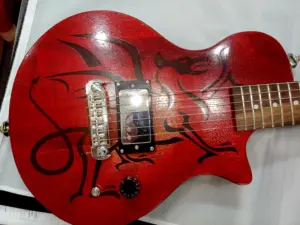
Use a cement of your choice and remember to keep the adhesive well inside the recess so that any excess doesn’t overflow onto the surface of the plaques. If this does happen, clean it off as gently and quickly as possible. I put some weight on the coins to ensure the best adhesion.
I’ve used basswood for “novelty” items, and balsa wood to fabricate parts for model aircraft and boats. I find that softwoods present my biggest challenges. These woods burn easily, so it’s crucial to get your settings just right to avoid spoiling the appearance of the finished article.
When you’re manufacturing components for model planes or boats, for example, you need to remember that tolerances are very tight to maintain the strength of the part. So, again, you need to get settings just right and not remove any more wood than is necessary. Let’s say you’re making spars and frames for a wing or hull. If you are out of tolerance on each piece, it’s possible the wing won’t assemble properly.
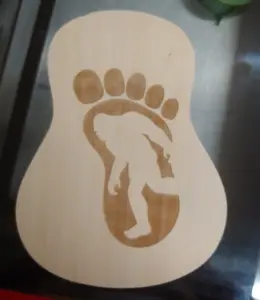
I use hardwoods in a variety of pieces. For example, I work with a partner to produce custom guitars and ukuleles. Using mahogany for bodies and maple for necks, there are a wide range of options available to produce custom inlays and artwork for the bodies, necks, and headstocks. I’ve used hickory for custom pickguards.
Our store features a Heraldic research feature where we can identify the coats of arms for family names. We reproduce these on a variety of items, my favorite being engraved shields using maple blanks. Maple generally engraves beautifully, but be careful if you get a piece with wide-grain sections. The difference between dark and light grain on maple can be extreme, and the result can be a very inconsistent finish. A graphic with very fine details can result in a very poor result if you engrave across these thicker grain divisions.
The following is a breakdown of types of wood and how they perform when engraving:
- Bamboo — Bamboo items are constructed using shredded bamboo, which is then bonded. This results in a material that has a very inconsistent finish. Using a standard focal length can result in widely varying engraving results, but by adjusting the focus by as much as a ¼”, the result is much more consistent. There can still be some variations, but all in all, the finished piece will look much better.
- Mahogany — Mahogany can vary in shade from light to very dark. My only advice here would be that if your customers want a dark plaque, they need to be advised that the engraving will be very difficult to see. This makes it a great candidate for color fill. When done correctly, this results in a classy finished piece.
- Cherry — This engraves beautifully. The only long-term challenge with cherry (incidentally, maple is the same), is that it actually darkens over time. If you have it in a place with varied shadows, you eventually get a “stripey” appearance. Just advise your customers on the topic so they can choose the best placement for the piece in their home.
- Hickory — Hickory engraves beautifully, but it is very hard and requires great care when cutting with lower- powered machines.
- Oak, ash, and poplar — I’ve worked with all three woods. The pronounced variation in the grain of these woods makes them unsuitable for most of the work I do, but in other applications, and with the right settings, great results can be obtained.
- Purpleheart — This is an example of a specialty wood and is very expensive. My experience has been that you’ll only be asked to engrave a finished piece supplied by the customer. Great care should be taken when working with these woods, and I always use a high-quality masking film with pieces made with specialty woods.
Woods will release oils during the engraving process. These produce a dark, sticky shadow around the graphic. Rather than apply a cleanser directly to the piece, I use a cloth dampened with the cleanser to gently remove the film. I have found that applying the cleanser directly to the surface of the piece can damage the edges of the engraving. When the cleanser has been removed and the piece allowed to dry, I gently rub in some furniture oil. (The exception to this is when I am working on an item for food use. Then, I’ll use a light coat of vegetable or olive oil.) As always, happy engraving!