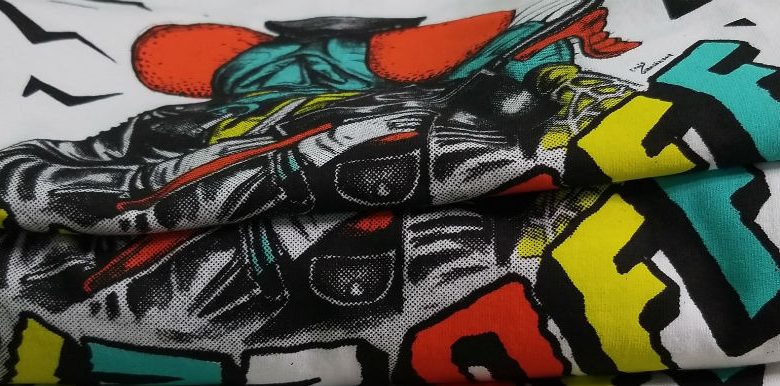
A couple of years ago, we started noticing a shift in what our clients wanted. Most of our clients were searching for soft, breathable, vibrant prints. If you haven’t started getting requests for water-based inks, I’m sure it’s coming.
We run water-based ink on 95 percent of our jobs. The biggest thing we’ve come to figure out is that every job comes with its own headaches and challenges. This article will touch on standard water-based and high-solid acrylic (HSA) inks, as discharge ink is its own encyclopedia of horrors.
Common issues on-press
If you’ve been printing plastisol for a long time, there is a high chance that your current stencil is not water-based ink resistant. Water-based inks will destroy an improperly exposed screen, especially with emulsion that is not water resistant.
Proper exposure and even proper post curing is the first step to making sure you can print water-based ink successfully. As much as our shop hates tape, it is an ally in the war on water-based printing. Water-based ink loves to find any nook, cranny, crevice, and hole, and run full force into and out of them. We find taping the inside of the screen where our squeegee and flood bar run, as well as where they chop, helps alleviate any premature wearing of emulsion during the print run. There is nothing quite like having to fix a pinhole on 500 printed shirts, only to realize you cannot fix them.
Water-based inks are becoming more and more popular among customers, so knowing how to best work with them is an important issue for all screen printers. (All images courtesy Night Owls)
Next up, water-based ink is not plastisol ink. It’s that simple. Water-based ink typically uses dyes or pigments in a suspension with water as the solvent. And just because it has water in the name doesn’t mean it’s eco-friendly and drain safe. There are still chemicals inside of your inks.
The water in these inks is meant to evaporate, leaving the dye behind. These inks need to be flowing, moisturized, massaged, or put back in the container and sealed tight. These inks will dry on the press if they are not handled correctly. This also means they will dry in your screen, clogging or blocking the open areas and making the screen unusable. On top of that, if not handled properly, your life will be horrible and end in nightmares of cakey, dry, and just plain unusable ink if your press is not running. Climates can also play a big role in how this ink is handled, confirming the tale that no two shops are alike.
Water-based ink typically uses dyes or pigments in a suspension with water as the solvent. The ink in the solvent is designed to evaporate to leave just the dye behind.
If your inks are wet and printing correctly, the next issue you have to worry about is curing. Most manufacturers of water-based and HSA inks will recommend a forced air (although gas is a bit better) dryer with your garments sitting in the chamber of your dryer, soaking in that sweet, sweet heat for two to three minutes. The longer, the better. That translates to most dryer belts at a slow pace. Without this conveyor belt in the heater, you run the risk of under-curing your prints and having adhesion issues, as well as washfastness issues.
Most manufacturers will make ready-for-use colors, but in our experience, very rarely is an ink ready to go straight from the bucket. We custom build all our inks and include additives to help combat in-screen dry time, washfastness, and sometimes we’ll add in low-temperature cure additives for difficult fabrics. These additives are resourceful tools to help ensure your hair stays intact during your print run.
We tend to constantly refresh ink on the screen, whether it’s moving the ink on the screen into the print area or adding fresh ink. One of the most common problems we deal with is overloading the screen with ink, but without mixing that ink into the production, it can start to dry out. Misting the ink with water can help as well but be careful because over misting can lead to bleed outs.
Clean up
After you get all sweaty printing these shirts in the glowing rays of the heat from the dryer, you now have to worry about cleaning up your press. Your shop is great at cleaning up screens and tools, immediately after every job, right? Because with water-based ink you have to be. If this ink happens just to sit around, you will deal with the aforementioned dry ink, ruined screens, and a bad attitude because you just threw a bunch of money away.
When we tear down our screens, we’ll leave the print area open after the last print. We typically walk around the press wiping our print areas out with a damp rag until our quality control team has confirmed that the order is indeed complete. Once we get that confirmation, screens are taken down and immediately stripped of ink. The ink is put back into its container, with a little bit of water to ensure it stays fluid. It’s mixed and then sealed, ready to be put back on the shelf. Once the ink is off the screens, we’ll use a damp sponge or cloth with some ink degradant to loosen up any dried ink left on the screen. From there, screens go straight to the reclaim sink, and any remaining ink is rinsed off with a pressure washer.
Left: By wiping your print areas with a wet rag on-press, you can help alleviate stains and screen/ink drying before screens even come off the press. Right: Proper exposure and even proper post curing is the first step to making sure you can print water-based ink successfully.
Water-based inks are meant to dye into fabrics, so be aware that you will likely have stains on your screen mesh, especially if you leave any ink in your print area. By wiping your print areas with a wet rag on-press, you can help alleviate these stains and screen/ink drying before screens even come off the press. Keeping buckets around your press with water and rags for cleanups and wipe downs is also a timesaver as you don’t need to run back and forth between sinks and press. A soaked cloth is much handier than a spray bottle, and typically a little less messy.
These are just a few tips and tricks we’ve picked up along the way. Every day, aside from being a winding road, is a new thrill ride. We are constantly working with our ink manufacturers asking them for advice and documenting what is and isn’t working for us. And, again, what we are seeing in our shop may not even be close to what you are seeing in yours, but, hopefully, these points can help alleviate some of your headaches along the way.