Using Silicone Inks on Dye-Sublimated Apparel
Overcome printing challenges on synthetic dye-sublimated garments
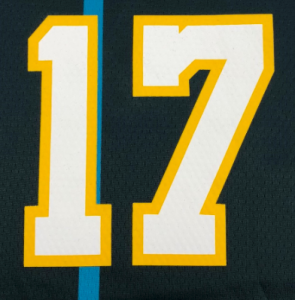
Silicone printing inks have been a staple within garment embellishment of performance wear for years. The use of synthetic fabrics made of polyester, elastane, nylons, and cotton blends has contributed to the steady growth of silicone ink in the market. The end-use of many of these garments is for athleisure and sportswear printing, and as such, moisture management, antimicrobial capability, and stretchability. As these needs continue to prevail, screen printers must tackle some of the challenges that come with them. These challenges open up opportunities for growth and utilizing silicone inks for this market.
While silicone inks are used in a wide variety of screen printing shops, they can still be hard to find in your local market. Having one more tool in your kit, especially one tailored for jerseys and other sublimated polyesters, that provides a distinct look and feel can set your shop apart from your competition.
Showcasing your shop’s ability to overcome printing challenges on synthetic garments is crucial. Let’s take a closer look at one major problem with these synthetics that silicone inks are naturally suited to solve: dye sublimation.
Sublimation by definition is a material passing from solid-state to gaseous without first becoming liquid. This transformation is important in printed embellishments because it allows the sublimated dyes in garments to ‘exhaust’ into and through your print.
How many of you have printed an order of jerseys for the local team, or used one of the many digital patterns available only to have them come out of the flash or dryer “grinning” at you? ‘Grin-through’ or ‘peek-through’ of these sublimated dyes will discolor your nice, bright white print and sacrifice your invested time and resources.
Dyes used in these polyester and polyester/elastane blends are by very nature, mobile. These garments are made by sublimating the dye or heating it until it is in a gaseous state to transfer onto the blank fabric. Silicone inks are also known to transpire gases, so the embellishment is working in conjunction with the moisture-wicking properties of the polyester garments. The stability of these materials requires low-temperature management when we embellish and launder (look at the use tag!). As long as we can keep the temperature below the activation temperature of the dyes, then the inks will stay in place.
Silicone inks cure at 240 F using a one-minute dwell time to help achieve a crisp, winning look. Use an underbase bleed blocker for bold, stubborn colors that act as a barrier layer or sponge that soaks up the bad-acting dyes.
Though curing temperature and settings are critical, you should also consider your ink quality. While you will pay more for a premium ink, remember that coverage using the right silicone system is generally obtained with 30% less ink than with other polyester inks. Less expense in ink and energy to cover and cure the garment offsets the cost for this innovative and still novel technology. With these considerations in mind, silicone printing inks can make a great addition to any product line.