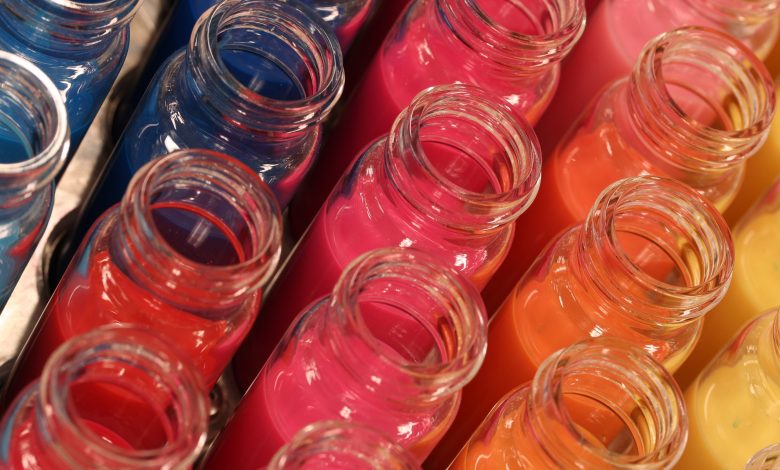
As advances in inkjet technology have progressed for wide-format and grand-format display graphic applications, developers have strived to provide high quality, increased productivity, better image durability and lower cost. Safety and environmental responsibility have also been considerations. Here we will discuss UV-curable inks and how they have attempted to meet these needs better than alternative technologies; where they have excelled and also where they have fallen short.
What’s in UV-Curable Ink?
Today there are at least four different types of UV-curable inkjet ink technologies. The early versions were designed for arc lamp curing and had several drawbacks due to the high heat the lamps produced and their generation of ozone, and the toxic outgassing from vinyl media.
Today UV inks for LED curing systems are quite common and avoid these problems. Like all UV-curable inks, they contain acrylic polymers called monomers and oligomers. They are the organic chemicals that make up most of the ink. When crosslinked they form the polymeric structure encapsulating the colorants and bonding the ink to the substrate.
The process of curing requires the formation of “free radicals” that act to crosslink or chemically bond the acrylic polymers to one another and the substrate. To generate the required free radicals, a photoinitiator chemical is incorporated with sensitizers in the ink formulation. They absorb the UV light and use that energy to create the “free radicals.” The sensitizer is a dye selected to efficiently absorb the UV light emitted by the arc lamp or a LED to provide it to the photoinitiator to initiate the crosslinking reaction. Though basically the same, ink formulations are somewhat different for arc lamp and LED curing systems.
So, in summary, the ink composition incorporates the acrylic polymers (monomers and oligomers), sensitizers, photoinitiators, pigments and other additives needed to adjust surface tension and viscosity.
Advantages and Disadvantages of UV-Cure Inks
Unlike water-based or solvent-based inkjet inks, UV-cure inks are much thicker, and higher in viscosity. The printheads are heated to reduce the viscosity so they can be efficiently jetted; and for this, industrial piezo printheads must be used. Thermal inkjet or low-viscosity piezo inkjet printheads like those sold in printers such as the HP DesignJet or Epson SureColor cannot be used. Industrial printheads for UV-cure inks are much more expensive, and the printers that incorporate them are as well.
UV inks do offer a significant advantage in that the inks do not evaporate in the nozzles like water-based or solvent-based inks, so the capping and wiping are much easier to manage and clogging is much less a problem. On the down side, the inks are very susceptible to stray UV light (such as ambient light) which can cause premature crosslinking which can clog up the nozzles. Equipment features in UV-curing printers are designed to avoid stray light, and other features keep nozzles free by randomly ejecting drops from nozzles not frequently used-critical features in a reliable printer design.
Another UV ink challenge is the fact that oxygen in the air competes with the monomers and oligomers for the free radicals that are formed upon UV exposure. Excess photoinitiator is usually incorporated into the ink to compensate for the oxygen degradation. If the oxygen consumes the photoinitiator before the crosslinking reaction then the crosslinking will be incomplete. To avoid this problem and allow for much higher printing speeds and more complete curing, EFI employs a nitrogen “blanket” the printing area of some of its printers to provide an oxygen-free printing environment.
To achieve a good cure and durable result, the UV light must get to all of the ink all the way down to the substrate. Since yellow and black pigments absorb UV light very effectively, care should be taken to be sure enough UV light is used when high coverage is printed. In addition, printing onto fabrics and other porous substrates poses an additional problem. If the ink penetrates the fabric or porous substrate before it is cured, unreacted ink can remain behind the fibers or deep within the porous surface.
How Safe are These Inks?
Whenever one handles or uses inkjet inks, the user should get a copy of the manufacturer’s Materials Safety Data Sheet (MSDS) and read it carefully. Liquid UV-curable inkjet inks are hazardous materials to humans. These are highly reactive chemicals, and they will react with you and your skin or eyes should you come in contact with it. If the liquid must be handled, then eye protection and skin protection measures are required.
Some people react to the components in UV-cure ink even at the low levels of vapor from the inks. This sensitization can be serious, and people handling these materials have been known to experience problems breathing and skin rashes.
When completely cured the UV-cure ink poses little problems for most people, however an odor is frequently experienced and may be offensive to some. Human sensitivity to the very low levels of vapors from cured UV inks is very high but the vapors do not cause a problem with VOCs or other concerns for the environment.
Summary
UV inkjet inks provide a durable high-speed printing alternative to water-based or solvent-based inks. No solvents, so no drying or VOC problems, better nozzle reliability with no evaporation are definite advantages. The inks are 100 percent solid polymer systems which is more expensive to produce than water- or solvent-based systems which have only 10-20 percent solids. Durability can be superior since only UV inks are chemically crosslinked polymers.
There is no need for the coated substrates required in water-based inks, so they provide lower cost media solutions in that regard. However, some substrates may require a treatment or primer to achieve good ink adhesion. For all inkjet systems we should remember it is a system, and for optimum performance the ink and the substrate along with the curing processes should be designed to work together.