The Common Causes of Thread Breaks
First, identifying how the sewing variables work together
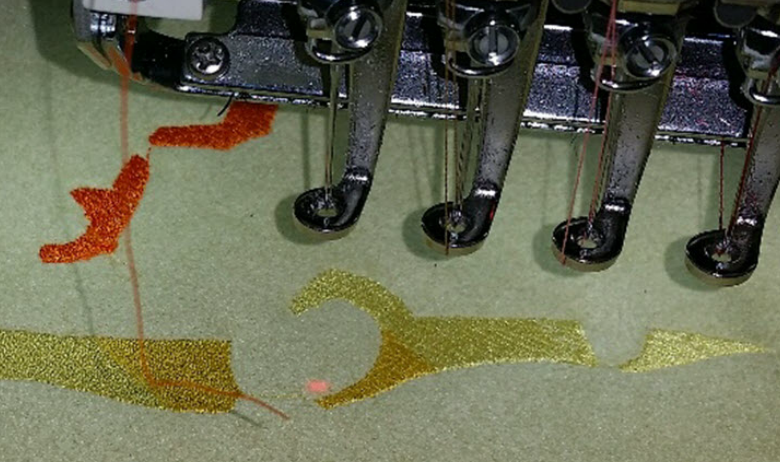
To narrow down the possible causes of your thread breaks, you must identify how the sewing variables work together and affect each other. Regarding thread breaks, all of the potential reasons will fall into one of four categories: lower thread path and bobbin components, upper thread path and needle components, the garment, or the embroidery design.
FINDING THE SOURCE
Examine these four categories and their relationships with one another to start to solve the basis of your thread breaks.
Lower thread path and bobbin components: The bobbin components are common to all needles in the machine. In other words, if there is a bobbin or hook problem, then it will affect all of the needles.
Upper thread path and needle components: Each needle and its components are stand-alone items. If thread breaks are only occurring on a few needles, then it’s probably related to the needles or some component of the thread path for that needle.
The garment: If the garment is extremely thick or stiff, it can lead to thread breaks. Also, if it’s hooped improperly, “flagging” can occur during sewing, which will lead to thread breaks.
The embroidery design: The design is common to all components of the machine. If thread breaks are occurring in the same areas of the design on each successive run, then it’s probably a design problem. On the other hand, a design with tightly-packed stitches may have random thread breaks throughout the entire design.
COMMON CAUSES
The next step is to identify each of the potential sources of thread breaks and identify characteristics that will help eliminate or identify it as a problem. The following are the most common culprits of thread breaks.
Improper hook timing: Improper bobbin hook timing gets blamed for a lot of things, but it’s rarely the culprit. If thread breaks are frequently occurring on all needles of a sewing head and the design is ruled out as the problem, then the timing or some component of the bobbin is most likely the cause. If the thread breaks on a couple of needles, bobbin hook timing is probably not an issue because each needle on the head is dependent on the same bobbin hook relationship for sewing.
Improper needle depth: This is a more likely cause if frequent thread breaks are occurring on just some of the needles. If the needle depth is incorrect, it will affect the relationship between the specific needle and the bobbin much the same as if the bobbin hook timing was incorrect.
Defective thread: Most people never suspect that a cone of thread is defective. However, like anything else in manufacturing, defects can certainly happen.
Defective needle: If you feel a needle could be causing thread breaks, simply replace it with a fresh needle. Be sure that it is inserted properly as per your manufacturer’s instructions. An improperly installed needle can affect the timing.
Upper thread path problems: Occasionally, the upper thread comes out of the proper thread path. Trace the path and make sure the thread is following the correct path from cone to the needle.
Lower thread path problems: Start with the bobbin and verify that it is properly installed and smoothly feeding out of the bobbin case. Look for dirt or lint buildups. Also, verify the thread trimmer is fully retracting.
Incorrect thread tensions: Thread tension is always a factor with just about every embroidery problem. Incorrect thread tension does not always cause thread breaks, but it is certainly a potential cause. For example, if the upper thread is too tight, it may lead to missed stitches.
Fabric too thick or stiff: Extremely thick or stiff fabrics can lead to thread breaks. One common occurrence is that the needle slightly bends as it passes through the fabric, causing it to graze the inside edge of the hole in the needle plate. This grazing results in the thread rubbing against the edge of the needle plate hole, which shreds the thread. Changing to a larger needle may improve penetration. The same problem happens with six-panel caps as the needle makes contact with the center seam, causing the needle to deflect slightly.
Hidden obstructions in the garment: The item being sewn may contain some hidden obstructions, such as plastic “stays” in collars, interior seams, or inside pockets.
Fabric or hoop bouncing while sewing: The item being sewn must be hooped such that the fabric is not too tight or too loose. Loosely hooped fabric will bounce up and down while sewing. This problem is a very common situation with six-panel caps as well. A machine with a digitally-controlled presser foot can solve a flagging problem.
Too much design density: The design may be the underlying cause of multiple thread breaks. Too much density in an embroidery design is much like fabric that is too thick or stiff. It leads to needle deflections, which can cause thread shredding and breaks.
Stitch lengths are too short: Extremely short stitch lengths may lead to thread piling up in one area, which leads to needle deflections and thread breaks.
For more on thread breaks, check out this video.