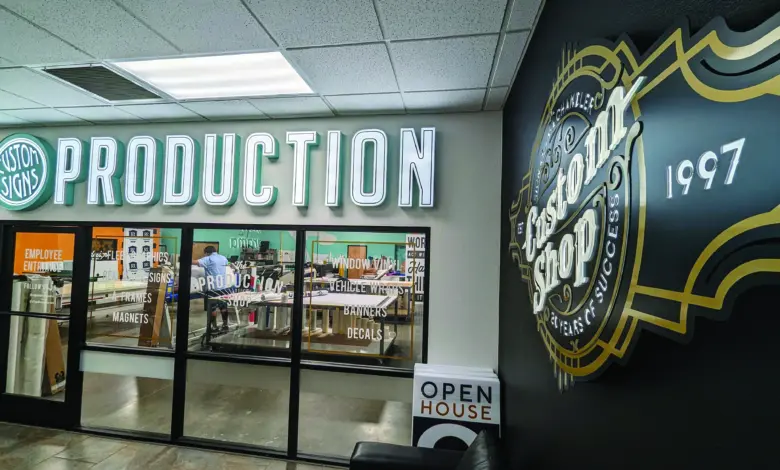
CNC routers offer sign shops flexibility and versatility, opening up many new opportunities in the sign and graphics space just based on the types of substrates used. The most popular sign substrates are acrylic, aluminum, PVC foam board, exterior grade medium-density fiberboard (MDF), and sign foam, but new substrates are being developed all the time.
Wood is still a popular CNC substrate for certain applications, but mostly it has been replaced with composite materials, such as MDF, that have the strength and carvability of wood but are more durable,especially outside.
The right match
Jim Eichenberg, owner of Signarama Chandler, in Chandler, Arizona, says the materials his company uses on the router are dictated by the kinds of signs it sells. The company, which was started by Eichenberg’s parents in 1997, targets small local businesses with brick-and-mortar locations that need fascia signs, window graphics, interior signage, and vehicle graphics. The company also works for larger out-of-state sign companies that need help with sign permitting and installations in Arizona.
The bulk of what Signarama Chandler produces is fascia signs and monument panels, Eichenberg says, which means plenty of routed aluminum for channel letters and acrylic for faces and monument sign panels.
Channel letters are in high demand for the inside and outside of buildings that can either be front-lit or back-lit with LED lights. The outline of the letters can be made with aluminum or stainless steel that can be brushed, painted, or mirrored. Signarama Chandler has a CNC router, a paint booth, and digital printers.
“I can make the most beautiful, creative creations you’ve ever seen. I can custom fabricate anything using great machines but what pays the bills is letters. We have letters coming out of our ears. That’s what people need. That’s what their signs are … just letters,” Eichenberg says. “Yes, you can dress up a letter and make it fairly fancy. You can add different layers to it, paint the edges one color and one color on the face. You can get creative if the client is willing to pay for the added cost.”
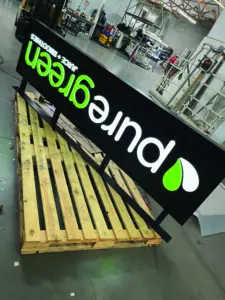
Jeff Voll, VP of sales for AXYZ, says that his company’s routers can cut all the main sign materials, including foam core, aluminum, acrylic, such as ACRYLITE, and even vinyl. Shops can make pop-up sign displays, aluminum signs, highway road signs, real estate signs, and adhesive signs for walls and windows.
AXYZ routers come with seven-tool, 10-tool, 14-tool, or 21-tool carousels for automatic tool changeout. They also have automatic height sensing, so if the operator makes a tool change, there is a sensor to verify the distance from the tip of the tool to the wasteboard that the substrate sits on.
“We make sure we are not cutting that part or going too deep, if you will,” Voll says. Shops want their tools to last as long as possible, and that won’t happen if they are plowing through the wasteboard.”
When AXYZ cuts ACRYLITE, it uses a cold air knife that blows onto the cutting area, where contact is made between the tool and the plastic, to keep it very cool.
“The reason you do that is to get an edged surface very smooth, and you’re also cooling down the knife. You don’t want the plastic to fuse to the knife,” he says. The added benefit of this is that customers
don’t need to buff, sand, or polish the outside edge of that letter or whatever they cut out.
Aluminum composite metals are another material that is prevalent in the sign industry. It is two sheets of prefinished aluminum sandwiched around a polyethylene core. The material works well for channel letter backing and indoor and outdoor signage because it is lightweight and durable.
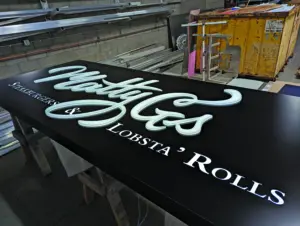
AXYZ makes CNC waterjet machines that use a 60,000-psi stream of water to cut aluminum, plastic, and even granite.
“You could never cut granite on a router. It would chew through tools so fast,” Voll says. With water, it isn’t that much faster than routing, but it is very precise. Another benefit of the waterjet head is that it can cut different angles than a router head.
Buddy Warner, who is in sales at ShopBot Tools, says that some substrates can be used inside or out, such as Sintra, an expanded foam PVC. Some sign makers use these more heavily indoors, particularly the 1/8″ sheets that come in red, green, yellow, and blue, due to their tendency to warp in the high heat of direct sunlight. Thicker sheets are normally available in white or black. Expanded foam sheets come under many brand names, including Azek, Palboard, Komotec and Celtec PVC.
“Some of these are gooier when cutting and not as dry and powdery as Sintra, and some imports will have small voids inside as well and are not as consistent throughout,” he says.
Other indoor materials include aluminum, brass, and copper. Warner says he typically uses phenolic-backed metallic laminate for indoor signage, although there are exterior grade metallic vinyls that can be applied and used in or outside.
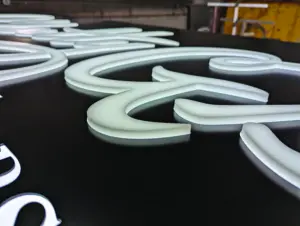
Acrylics can be used inside or out and are sold in cast or extruded varieties. “Cast engraves nicely, leaves the cut white when etched and is very clear, but is much more likely to crack,” Warner says. “Extruded acrylic is stronger and less likely to shatter and show cracks when drilled or cut. Either can be edge polished.”
Styrene is often used for indoor signs because it isn’t as durable outdoors as other materials. Foam Core or Foam Board has a layer of foam between various materials, like poster board. Ultraboard has a plastic-coated exterior. “These cut better with an oscillating tangential knife, but there are also bits that can be used,” he says.
Polycarbonate, such as Lexan or Makrolon, come in clear or white and are very tough, he says. “This material should be machined more like cutting aluminum, done in shallower passes.” While it can be used outdoors if it is UV-coated, this material is more commonly used for indoor signage.
One of the less expensive materials for outdoor signs is Extira, or exterior grade MDF. “This material is very dense and heavy and must be painted with the proper primer and paints,” Warner says. It is also highly water resistant.
Corrugated plastics, such as Coroplast, can be used outdoors for political signs, realtors, and others wanting a more temporary way to advertise. Sign foam, or high-density urethane, could be used indoor or out but is most commonly used for outdoor signage to “avoid the deterioration common with wooden signs,” he says.
ColorCore, which is two-color high-density polyethylene, is a great material for park signs or applications where only two colors are needed, Warner says. The material is high-impact resistant, durable, and doesn’t require any maintenance. Signs made with ColorCore are paint-resistant and can be cleaned with soap and water. Starboard is similar to HDPE and is frequently used in the boat industry for decks and signs.
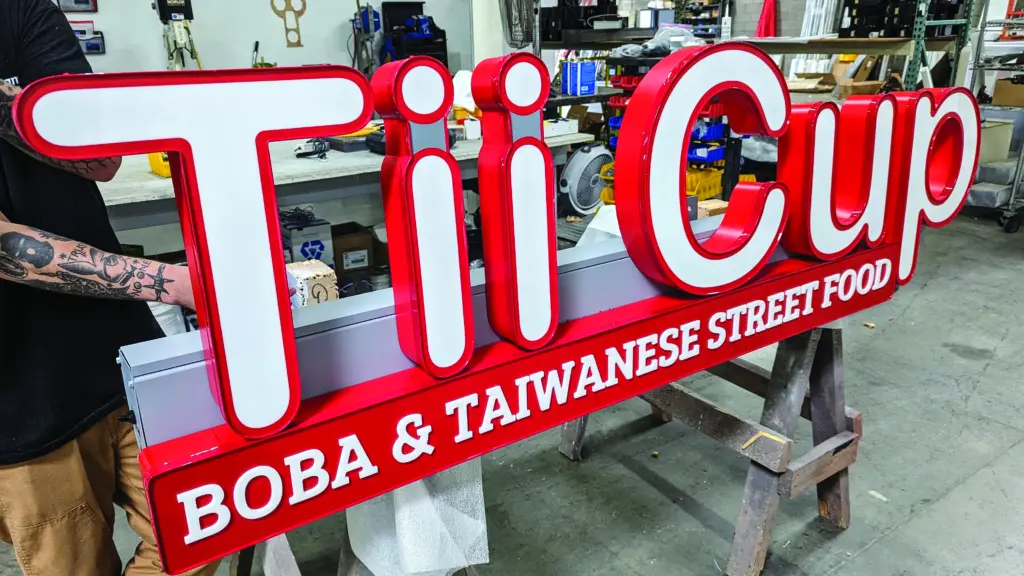
Router bits
Wes Bails, fabrication manager at Signarama Chandler, says that his company uses two standard types of bits for aluminum or acrylic in 1/8-inch, 3/16-inch, 1/4-inch, and 1/2-inch shanks. When cutting acrylics, Bails uses a 1/4-inch shank, and when routing aluminum backs, he uses 3/16-inch bits.
“When I was brought in and learning the machinery, I was taught to use the biggest bit you can get away with using because it is faster and more robust,” he says. “I only get down into 1/8-inch bits if I need detail, and I have to slow down speeds and feeds to accommodate the less strength of that bit.”
Bails orders aluminum and non-ferrous bits for aluminum and acrylic. If the shop has projects that require foams, he uses the acrylic bits for those projects. He prefers single flute upcut bits.
Eichenberg adds that “when it comes to routing, you can have the greatest router and the best tools for cutting, but if the speeds and feeds are wrong, you are not going to get a good product.”
It’s all about practice. He recommends that shops experiment on different types of substrates, using different cutting tools, to see what works best at different speeds. One important tip is to always do a test on materials coming from different vendors because the feeds and speeds may be very different from what the shop is used to using.
Bails created Google cheat sheets to give the shop’s router operators an idea of how fast they need to run the machine and feed in the material based on the thickness of the aluminum they are cutting.
As far as bit longevity is concerned, some bits can run for a very long time. Bails says he can run the CNC on one aluminum 3/16-inch bit for a month, routing aluminum. Typically, bits will wear out after a while, or a bit will snap at its weakest point if the material shifts unexpectedly.
Bits will last longer when cutting acrylic, he says, but once they get too dull, it is time to change them out.
When routing half-inch acrylic, a shop will get a poor edge finish if the bit is not perfectly sharp. When that happens, the fabrication department has to sand it down and make it clean. “It takes hours of manual labor, so we decide to recut pieces with a brand-new bit, which is less money in the long run than having guys spend time cleaning edges,” Bails says. Eichenberg adds that it is cheaper to buy a bit than deal with bad edge quality.
Warner says that most plastics are considered “soft,” but there are bits designed specifically for hard or soft plastics. The Onsrud 52-700 bits provide a great finish for the softer Starboard/polyethylene materials, and Amana has a great selection for plastics as well, he says.
“O flute bits, which have a circular cutting flute (rather than a flat one like a carbide tipped bit), tend to cut plastics better. Some plastics have a lower melting point and are more temperature sensitive, so less flutes, lower rpm, or faster feed rates work better on these. Harder PVC is temperature sensitive and cuts better with a low helix sheer cut bit,” Wagner says.
The Super O flute has a circular flute and is back-ground on the outside cutting surface to reduce friction and heat that causes melting and “re-welding” of chips back into the cutting groove or kerf.
“I generally do not recommend down cut bits for temperature-sensitive plastics as they create excess heat and friction, which adds to the problem,” he says. Denser or more abrasive materials like AlumaCore or Extira create more bit wear than Sintra, HDU, or HDPE.