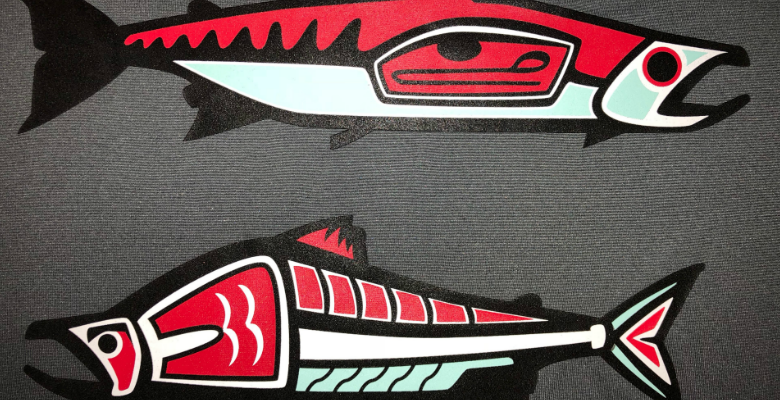
Silicone inks have been screen printed in the embellishment market for well over a decade but are still considered a specialty ink by most printers. Let’s simplify the science behind silicones and add this ink system to your toolkit.
The primary uses of silicone inks are in the athletic and athleisure market. Silicone inks use a low-temperature cure (260 degrees F) that is perfect for polyester, nylon, and blends. The stretchability of silicones is unmatched in screen printing inks and is ideal for elastic garments used in the sports apparel markets. Migration of dyes in polyester garments is another problem that silicones are well suited to control through low-temperature cure and bleed-blocking underbases.
Here’s a quick primer on using silicone in your shop.
MIXING
Silicones must be catalyzed to cure. Generally, 3-5 percent catalyst is sufficient, and retarders extend the screen life of inks in screen. Pigments are used according to the manufacturer’s recommendation or mixing systems. Reducers and thickeners are used to adjust viscosity. Other additives are available for special effects through different dealers. It’s essential to mix silicone inks until a homogenous ink is obtained.
Only catalyze the amount of ink you need for the job at hand. Keeping excess catalyzed ink in a closed container will help control ink waste costs.
PRE-PRESS
Standard screens and emulsions used for plastisol inks are equally applicable for silicone inks. Since silicone inks are solvent-less, emulsions do not need to be dual-cured or post-hardened. Most silicones can be printed through a variety of mesh from 81 to 305 tpi, though viscosity and opacity of the system you are working with will determine the best fit. For best opacity of whites and colors on dyed synthetic fabrics, use 86-110, as finer mesh will give a smoother finish. A 2+2 emulsion coating technique should give you 40-60 microns film thickness to optimize opacity.
PRINTING
Silicones are generally used in spot color printing of vector images like sports logos, names, and numbers, but don’t let that keep you from applying it in simulated process jobs. Always be creative!
Generally, silicones print similar to plastisol inks while adopting ink management techniques similar to water-based systems. A 65/90/65 squeegee helps to deposit enough ink for opacity while transferring evenly over large open images.
One property that sets silicone apart from other inks is that silicones are a thermosetting (crosslinking) material, rather than thermoplastic (melting) materials. Without taking a chemistry refresher, this means that once the ink cures there is no going back. It is set. This is a great attribute when it comes to durability, wash fastness, and stretch but leaves gaps in areas like fibrillation control.
For ultimate stretch without cracking, you cannot beat silicone inks. Deposit a thicker ink film to increase stretch for high elastic content fabrics. This can be done with multiple layers or thicker emulsion.
Synthetic apparel continues to grow at solid and steady rates in today’s market. Silicone inks will open up a whole new world of printing technology for your shop. Print on!