A sign shop laser cutter can be used for a wide variety of applications, from basic engraving to cutting acrylic letters and logos. But, one substantial part of the market for laser work is industrial items and labeling, from product I.D. and service record items to entire control panels.
At our commercial sign shop, we like industrial work and try to do our share of it, and part of the reason is this type of work is likely to be repeated. After decades in the sign business, I am more convinced than ever that the one-of-a-kind sign-making business is seriously inefficient and if it weren’t for repeat and duplicated orders, we might as well be flipping burgers.
We have done several projects for local industrial clients, and they have pretty well covered the types of work I am trying to describe for this Shop Talk, so we’ll look at some of them and try to suggest some ways to make these kinds of projects make sense and make a decent profit.
Perhaps the most challenging of them are the jobs we are asked to do that involve producing custom control panels from stainless steel, generally 16 gauge (about 1/16″) to 12 gauge (about 1/10″) sheet. Stainless steel in any thickness is expensive, so prototypes are definitely required.
Fortunately, if your graphic software can read a CNC (.dxf, .dwg, etc.) accurately, prototyping can be done very well using thin posterboard. Our software will import these files, but does not connect the lines or create paths-but can be made to do so with a bit of tweaking-and the dimension accuracy is very good.
For quick yet accurate prototyping, we keep some thin white posterboard (available in full 4′ X 8′ sheets) and is cut into smaller sheets to fit our laser (24″ X 39″). Before engraving and cutting, we simply spray a light coat of fast-drying spray can primer over the sheet. The engraving shows up as white, and the laser makes short work of cutting out our control panel mock-up, with all inside holes and accurate outside shape.
If the client makes changes to the first version, which is quite likely, alterations are incorporated in our design and another paper version is produced. Only after the customer has approved the final version, which may require more than one revision, is the real item cut on a CNC waterjet. After that, it is cleaned, surface prepped, and coated with laser marking spray (CerMark), which is water-soluble but leaves a totally indelible black mark on stainless. This coating only works on stainless, but it really does work and cannot be removed or weathered off.
There is a trick to making these stainless items clearly readable, since stainless steel is quite reflective, even with a brush finish, and lettering on its typical surface is hard to read.
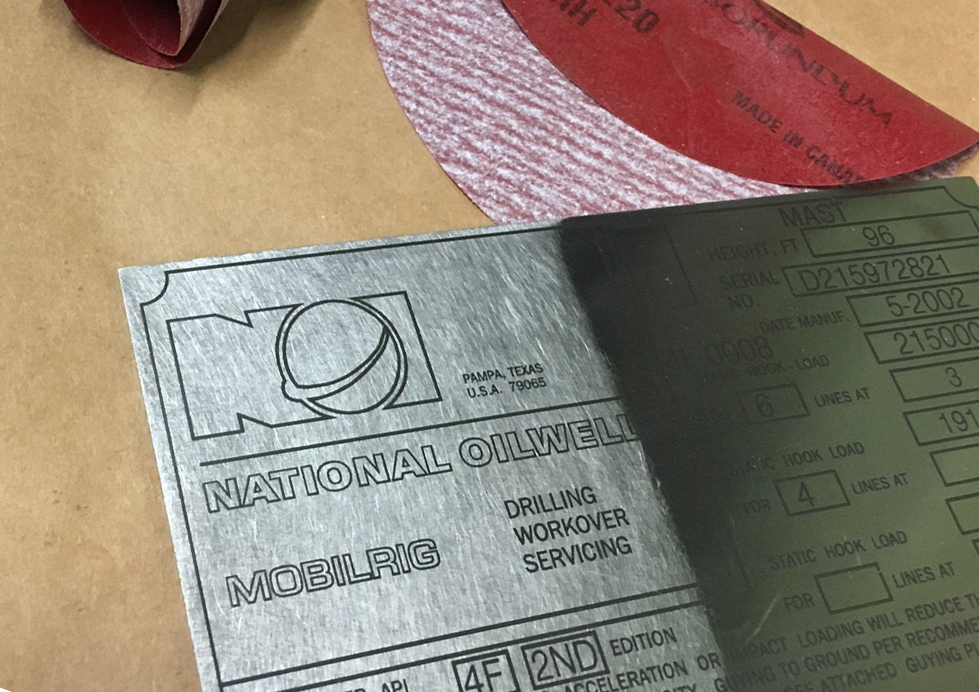
We have found, through trial and error, we can produce a fine satin finish that is not reflective and has much improved readability if we etch the surface of our control panels with a random orbital sander. The sander must be “random orbital,” and we like using 220 grit sanding disks, going over the surface until it is evenly etched and uniform in appearance. Our customers have been very satisfied with this satin silver patina and the clarity of laser marking on it.
Often we are making new tags, but sometimes clients will bring their pre-printed (screen printed) tags to us to engrave. We coat them with CerMark the same way, and after setting up a very accurate version of their item in our software, simple cardboard guides are cut on the laser to hold the items in a very exact position, and the tags can be laser engraved multiple times into their cardboard fixtures.
Some of the best industrial laser-engraved jobs we get involve us creating a manufacturer tag, generally with fields where the clients stamp information, and often these can be prefinished .040 black aluminum. To remove the black coating sufficiently, the laser may have to go over it twice, but the final result is quite good and a laser requires little babysitting.
Other tags, made the same way, may have generic information, and we are basically producing very permanent labels that will far outlast any type of printed tag. These are good jobs, and generally, for the aforementioned advantages, that is they are easily produced and have a high likelihood of repeatability.
We are fortunate to be connected to a company that has some CNC cutting equipment, so coming up with blanks tags of any shape, size, hole pattern, or configuration is relatively easy and fast, but sign makers in most markets will be able to find a vendor who will be glad to do cutting of thin items like these, especially if you can set up a cut file they can import easily.
Most vendors can work from a standard vectored file (.ai, .eps, .pdf), or certainly CAD (.dxf, .dwg) if one can be provided. It may be best to provide the blank metal material if they don’t stock what is specified by the client. And perhaps the most important aspects of building a good relationship with a local CNC cutting service are to allow a decent amount of time to get your work done and to always pay for your work on the spot.
The bottom line and that is what we need to be watching, is that in most any area there are local manufacturers who need this kind of work, and may not know you can help them with it in their own neighborhood. Some marketing may be required, and a little practice, but over time a healthy and profitable business can be built up catering to these industrial clients, who may well become some of your best laser customers, and possibly your best and most profitable customers period.