Printing Greener: How to Make Screen Printing More Earth Friendly
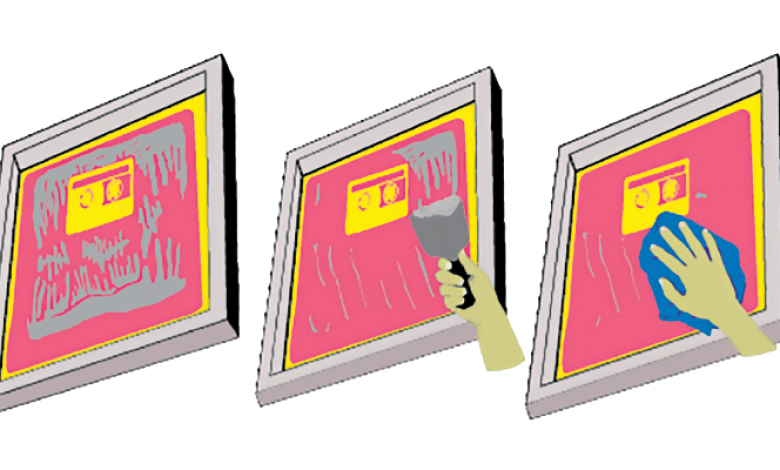
Whether it’s to meet compliance or just to do your part in working towards improved sustainability in our industry, most of us have been looking ahead to consider our best options when it comes to environmental responsibility. In this article, we’ll look at a few places on your production floor where you may find some opportunities to work toward better sustainability.
When I try to zero in on where apparel decorators doing screen printing can improve their inefficiencies, the first things that come to mind are the garments we print on, the ink we use on those garments, and the chemistry used throughout the process.
Starting soft
Let’s jump in and start with the garments made accessible to us for printing. Apparel companies have spent years developing better offerings for you to choose from and have provided countless articles and advertisements to educate you on these ever-growing options. You may notice that the bigger the company, the more options available, therefore, the more resources they have put into development and compliance.
As decorators, we are often attracted to the underdog. Many of us started in garage or basement shops and are actively building our businesses, so it’s natural that we would want to seek out other underdog companies to support. While it may be good business sense to look for less expensive options to lower our operating costs, these copy-cat brands who offer similar products at reduced prices are not the same companies putting the money into research and compliance. Bargain brands from abroad are more likely to have restricted substances in them that can cost you far more than you saved when a customer you print for gets nailed for noncompliance on an item they hired you to print responsibly.
Many of these restricted substances are known as environmental threats. For instance, APEO has been banned from apparel production in Europe entirely, due to factors including its impact on aquatic life and the human body. APEO has been identified as an endocrine disrupter, causing aquatic species to change sex and as a skin and respiratory irritant to humans. I could go on with more info concerning restricted substances that some of the more widely recognized brands are actively addressing, but the main point is that you get what you pay for with bargain alternatives. And that doesn’t just include the product’s questionable performance and the potential liability you pass on to your customer. It circumvents financial support into research for more sustainable future options.
The Nitty Gritty
I want to remind you that screen printing implies that both the screen and the printing aspect of our industry must be of some importance. And it’s true. We are only as good a printer as the screens we produce. So, when evaluating how you can improve the quality of your screen making process, don’t forget to ask yourself if you are reducing waste. The most overlooked part of this process is the light source in your exposure unit. If you are using a bulb-type exposure, ask yourself these questions:
- Is my emulsion the correct type for the light source I have?
- When was the last time I verified my exposure times with an exposure calculator test?
- How old is my light source? Is it curing the emulsion properly?
If you are unsure of your answers to the above questions, reach out to your local supplier and tell them you would like to speak to an emulsion representative. They will be able to evaluate whether you have the correct exposure, light source, and emulsion to get the best screens for your shop’s production parameters.
When you optimize your screen-making process, you send less unexposed emulsion down the drain. This means you retain more money, lessen your impact on the local water treatment facility, and get more life from your in-house water treatment system. In the end, you produce better screen stencils, which make better prints, thereby reducing your stress levels and increasing productivity.
In the previous paragraph, I refer to an in-house water treatment system. If this is a new phrase for you, then it is time to speak to your emulsion chemistry rep to see what your options are to capture solids and pre-treat the water you are discharging into your municipality’s water treatment system. There are several systems that you can add to your existing reclaim process that will help meet or exceed your local requirements. If you are concerned that reaching out to an emulsion or reclaim chemistry company is just inviting a new sales pitch, keep in mind that their role is as much about keeping customers informed and compliant as it is to sell their products. A sales rep is a company’s first line of defense in making sure they avoid legal issues related to misuse of the products they offer. When doing your research to see if you meet local requirements, reach out to your chemical companies for their guidance before inviting unwanted attention to your business.
In addition to systems that you can purchase or even build yourself to capture solids before they go down the drain, there are also products offered by your chemistry companies to capture solids while cleaning your squeegees and flood bars. These products provide solutions that range from capturing particles in filters that can then be cured in your dryer and disposed of properly to facilitating active enzymes to break down ink sludge. Speak to your local screen print supplier or attend a trade show to learn more about these and more options.
The goal here is to keep as much chemistry and uncured ink from leaving your facility as possible. By capturing and curing these solids, we prevent them from contaminating our drinking and groundwaters. By disposing of this waste responsibly, we minimize the impact we create from our waste. What about all those cut-up T-shirt rags you have been using to clean screens? As your printing process improves over time, you should notice less garment waste, which means you will need a new source for rags to clean screens.
Uniform laundering companies typically provide a rag reclaim service with a regular delivery of reusable rags, that they pick up to launder and dispose of the ink waste responsibly. This means we eliminate the impact caused by throwing away ink-covered rags. That responsibility now belongs to the laundering service, the cost of which is offset by the savings we see in our garbage haul away costs and time lost searching for and cutting up used garments for cleaning. So much of our productivity is lost running around the production floor, searching for various things versus working continuously and without distraction.
Chemistry
Now, let’s look more directly at the chemistry we use to clean and reclaim screens. Much of what you are paying to ship to yourself is water, so the most noticeable improvement that most shops can make is to switch to concentrates. For example, if a shop is buying three drums of a finished product per year, there is an obvious benefit to buying and shipping one drum of concentrated product and adding water to it on-site. Not only do you save on shipping, but you also reduce container waste.
One of the inefficiencies I regularly encounter is an employee who thinks that spraying more chemicals on a screen makes it reclaim faster. There is a point of diminishing return that you reach pretty quickly, meaning that your employee is just washing wasted product down the drain. And you paid for it.
When I began buying my chemicals in bulk drums, I was offered a free air delivery sprayer system. This system enabled me to create a standardized process that dictated precisely how many squeezes of the sprayer per chemical per screen were required. The illustrated procedure was then posted in the reclaim area for employees to reference during this step of the process.
Now, let’s address single-use chemistry and how to avoid it. The most obvious answer is to use a dip tank for your emulsion degradant. Why use the chemistry only once when it is strong enough to use again and again? The key is to remove all residual ink from the screen before placing it into the dip tank. By first removing the ink, you avoid staining the mesh, which negates the need for haze-remover.
I simply will not use haze remover, so the ink is removed then cleaned from the mesh with reusable rags before reaching the emulsion degradant tank. This extends the life of the tank chemistry by avoiding ink sludge build-up that can weaken the tank’s effectiveness. Make sure that you are recharging the tank with the properly pre-mixed product as the reclaim tank chemistry evaporates or loses efficacy. Don’t simply add more water or concentrated chemical. This will often work against you. If the product requires a 5:1 mixture, have a bucket of that mixture pre-made to add to the tank as needed.
Recirculating chemical tanks are a practical option for cleaning squeegees and flood bars. Some of the companies that offer these systems also provide removal and proper disposal of the used chemistry. Another tip to avoiding haze remover is to avoid using aerosol screen openers or press wash. You are wasting money on the can and the propellant inside that can. Buy concentrated chemistry that you add water to in a reusable spray bottle. The propellant in your aerosol accounts for a portion of the weight you are unnecessarily paying to ship to yourself, never mind the fact that the aerosol chemistry can lock red and black ink stains into your screen mesh.
While we are on the subject of tanks, consider adding a clear water dip tank to your screen making process. This tank is what it sounds like, just a tank of clear water. As soon as your screens come off the exposure unit/system, place them in the clear water dip tank for no more than one minute. This will stabilize pure photopolymer emulsions from further exposure in ambient room light. More importantly, it will soften the unexposed emulsion on your screen so that it requires less energy and less water when applying your final rinse to the exposed screen. This also helps retain small details without washing away your screen stencil gasket.
Water Works
Now that I’ve got you thinking more about how you can produce better screens with less impact on your local water treatment (and hopefully less impact on your budget) let’s talk about your ink. We talked about buying your ink from a responsible manufacturer earlier in this article. What we did not cover are the different types of ink chemistries.
The two main ink categories are plastisol and water base. Plastisol offers you the ability to store and re-use leftover ink. If you buy your ink from a reputable brand that produces ink to be internationally compliant, plastisol affords you many options to prevent any uncured ink from leaving your facility. But what if you are required to be a PVC-free facility? There are PVC-free plastisols available, but they need a different approach to printing that requires more flashing. With that being said, we may as well look at water-base.
Water-based sounds earth-friendly, right? Well, again, that depends on who you source your water-based inks from. Water-based inks require their own chemistry to stabilize the product and keep it fresh. Depending on where that water-based chemistry came from, the word “water” does not promise the product is any less impactful than plastisol. Again, you want to be selective with what brands you choose.
While responsibly developed water-based products are designed to eliminate restricted substances from their formulas, they can produce more waste. You can control this by keeping your ink buckets sealed with lids, using an accurate scale to mix your inks, and by making use of the appropriate ink mixing calculator provided by the ink manufacturer. I know many of us are proud of our “mixing-by-eye” skills, but remember that the only way to correct color is by adding more pigment. This means you are creating more waste at the end of the day. Use your ink calculator and reach out to your ink company’s color matching labs. You are paying for that service when you pay for the ink, so you should use it.
The benefit of water-based that shines the brightest, aside from a soft hand, is that the cleaning chemistry is simply water. This means you are not paying for additional cleaning products, you are putting less stress on your water treatment system, and at the same time reducing your exposure to aggressive chemicals.
There is no perfect way to produce anything without having some sort of impact. The goal here is to identify and make use of responsible printing options. More importantly, we have to reexamine our current print practices and determine where we can be more efficient and produce less spoilage and waste. Sustainability is a big picture issue. Clinging on to hot phrases like “green” and “eco” in product names is not enough. Considering how much wasted energy that can be eliminated in the form of electricity, gas, water, and human movement is just as important. Ask yourself if you are getting the most out of what you put your money and time into.