I first got involved in screen printing after learning lithography in high school. Lithography felt too rigid and mechanical for my taste, but screen printing — whether on paper or T-shirts — immediately resonated with me. The process itself felt like an art form, not just a means to an end.
I never set out to get rich from screen printing. I did it because I loved it. Over time, I printed millions of tees — sometimes, over 3,000 per day — before transitioning from running automatic presses to sampling and sales. As my experience grew, so did my ability to refine techniques and increase efficiency, turning my knowledge into profits.
The value of experience often lies in knowing what not to do. Just like a mechanic’s worth isn’t just in labor but in diagnosing the problem, a skilled printer understands what mistakes to avoid. Many of the troubles I encountered early on stemmed from cutting corners. If I had planned better, I could have spared myself a lot of wasted time and money.
So, let me pay it forward and highlight some key fundamentals that can keep your operation running smoothly and profitably.
Your screen printing shop is a money machine
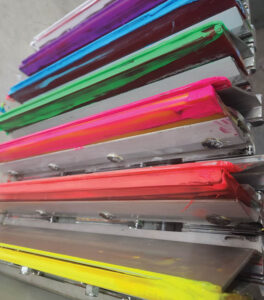
Imagine you had a printing machine in your garage generating $500 per hour. Would you let it run out of ink or use subpar materials? Of course not! You would do everything in your power to keep it running optimally.
Yet, in screen printing, many shops try to cut costs by using lower-quality supplies, thinking it will save money in the long run. But it doesn’t work that way. Just like using cheap oil in your car can lead to costly breakdowns, using inferior inks, screens, or emulsions can slow production and increase waste.
High-quality ink, for example, is more opaque, flashes quickly, minimizes buildup, and cures at the correct temperature. In contrast, low-quality ink often leads to frequent screen cleaning, multiple print strokes, longer flash times, and curing problems. The small cost difference per print is easily outweighed by the time and efficiency gained with better materials.
Mesh tension: The foundation of a good print
Every year, when we print detailed images for our trade show displays, we hear the same question from visitors: “How do you get your prints so sharp?” The answer, more often than not, comes down to mesh tension. A properly tensioned screen ensures that fine details stay crisp, halftones remain consistent, and ink is deposited cleanly. Without the right tension, even the best artwork and screens can fall short.
It’s a simple but often overlooked factor that separates an average print from an exceptional one. If your screens don’t sound like a drum when you flick them, they may be too loose.
Consistent screen tension is also crucial for proper registration. Before coating screens, test them by flicking them with your finger; they should all produce the same high-pitched sound. Loose screens require more off-contact, slowing down production and reducing print quality.
Clean screens are more profitable
Before coating screens with emulsion, ensure they are properly cleaned and degreased. Dust, debris, and grease can cause pinholes and emulsion breakdown. Store freshly-coated screens in a clean, horizontal drying area with the ink side facing up. Avoid using fans or outdoor drying to prevent dust contamination.
Darkroom: Protect your screens from the silent killer — light
A properly controlled darkroom is critical for consistent, high-quality screen exposure. Position it close to your washout area to minimize light exposure and ensure no stray light leaks in — tiny gaps around doors or vents can degrade your emulsions. Blackout curtains or plastic sheeting can help eliminate contamination.
Use your existing in-house air conditioning to help condition your screen room’s environment. This air is filtered and dry and, in most cases, readily accessible. In case your darkroom cannot access the building’s air conditioning, a dehumidifier is essential, as controlled moisture levels speed up drying and improve stencil integrity.
Be mindful of your light sources — Rubylith film works best for covering bulbs, as some amber filters may still allow UV light to expose your coated screens. Even stored emulsions can slowly degrade if exposed to improper lighting over time. Just like unwanted heat can ruin your ink/prints, unwanted light will ruin your coated screens.
Emulsion: More than just a blocker
I sometimes scroll through social media and come across so-called screen printing “influencers” coating screens with emulsion on camera. More often than not, the videos are cringe-worthy — not because of their technique, but because they’re doing it in a space contaminated with light, sometimes even under regular neon lights.
Emulsion needs to be applied in the darkroom in order to function at its best. Exposure to stray light — even for brief moments — can start the curing process prematurely, weakening the stencil before it even reaches the exposure unit. Over time, constant light contamination can degrade emulsion in storage, leading to unpredictable results on press.
Emulsion doesn’t just block areas of the mesh — it creates a gasket that controls ink flow. A properly applied emulsion layer provides clean edges and improved ink opacity. To maintain quality, store emulsion in a cool, dark place and keep it free from dust, moisture, and contaminants — any impurities can lead to pinholes, weak stencil edges, or premature breakdown during printing.
Different mesh counts require different exposure times. Shops should dial in exposure settings for each type of mesh they use. Since each person coats screens slightly differently, exposure times should be tested and adjusted accordingly.
Film positive: The blueprint for a perfect print
A sharp, high-quality print starts with a dense, opaque film positive. The darker and more impenetrable the image, the more precise the stencil on your screen. Any light that sneaks through the dark areas can compromise detail and extend washout times, leading to subpar results. Even with newer technologies like direct-to-screen exposure units and laser systems, the fundamentals remain the same.
Many printers struggling with fine details don’t realize that poor film density is often the culprit. Simply put: bad film equals bad prints, which means lower quality and lost profits.
Pallets: The unsung hero of ink opacity
Screen printing on rubber-coated pallets can improve ink opacity and consistency. Unlike metal pallets, which absorb and release heat quickly — causing ink to gel on the screen — rubber-coated pallets provide better insulation and ink performance. If using metal pallets, consider adding rubber mats or adjusting ink placement to prevent premature gelling.
Proper curing: The key to durability
Every ink has a recommended curing temperature, typically between 275 F and 320 F. The entire ink film — not just the surface — must reach this temperature to ensure durability.
Excessive heat can cause dye migration, ghosting, shrinkage, and scorching. Instead of increasing heat, extend dwell time in the dryer. A longer cure time at a controlled temperature results in better prints and fewer issues. Time is your friend, and excessive heat can be bad.
Squeegees: Your quickest adjustment tool
Having a variety of squeegee durometers on hand allows for quick print adjustments. Need more ink deposited? Switch to a softer squeegee. Need less? Use a harder durometer.
Instead of double-stroking — slowing production and increasing costs — opt for the right squeegee. The small investment in extra squeegees saves time and money in the long run.
Don’t forget — the sharp edge your squeegee had when you first bought it will dull over time and needs to be either sharpened or replaced. Unless you just unboxed a brand-new press, the squeegee that came with it likely needs to be updated.
Invest in quality, reap the rewards
Screen printing is both a craft and a business. Cutting corners might seem like a way to save money, but, in reality, it often leads to wasted time, lower quality, and reduced profitability. By focusing on the fundamentals — quality materials, proper technique, and consistent processes — you set yourself up for long-term success. Remember, every shirt you print is a reflection of your art. Take pride in it and never stop refining your craft.