Mark on a Curve without Rotation of the Work Piece
The market offers a variety of methods to engrave drinkware, so how do you know what's the best method for your shop?
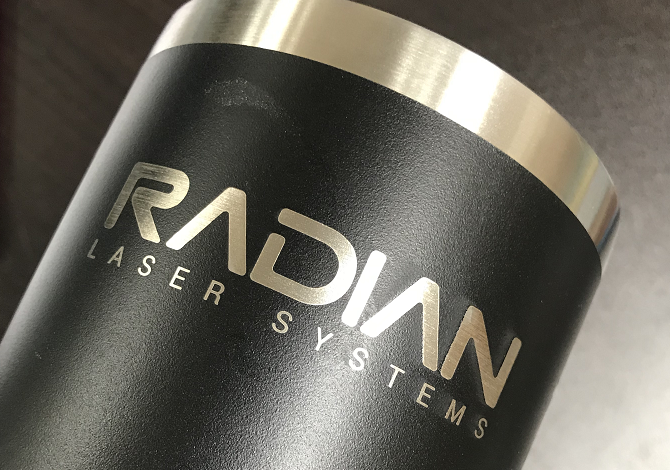
Radian Laser Systems, Anaheim, California, was established in 2002 to produce high-quality industrial laser solutions utilizing galvo-based CO2 and fiber laser sources. Radian designs, manufactures, and distributes customized laser marking machines, laser cutting tables, and work stations utilizing CO2, fiber, and UV lasers. Radian serves a wide range of industries and in addition to selling machines, the company provides machine customization, applications engineering, system repair, and production marking services. For more information, visit www.radianlaser.com.
Customized drinkware is all the rage! At a recent NBM SHOW, our team spoke with many customers looking to explore new markets or improve upon their current operations. Several of these customers were specifically interested in drinkware. Product suppliers offer an endless array of tumblers with various shapes, colors, sizes and finishes. Furthermore, the market offers a variety of methods of which to engrave them, so how do you know what’s the best method for your shop? Let’s review the technology and some ways to improve your operations.
FLATBED LASER VERSUS 3-D GALVO
The most common way to mark the drinkware (remove the powder coating to create the desired image), is with a flatbed laser. Other traditional methods such as using a flatbed CO2 laser and a rotary chuck are slow and sometimes produce mediocre results. This is often due to the fact that flatbed lasers are really cutting machines that also mark/engrave. In other words, they weren’t originally intended for fast marking, especially over curves. Customers are coming to us seeking different results, since Radian offers a 3-D solution that allows for marking on a curved surface without rotation of the work piece.
Using a 3-D galvanometer-based (galvo) solution for marking is preferred over flatbeds, as they are designed to be marking/engraving systems as opposed to a traditional cutting system. The high-speed galvos steer the laser beam over the work piece using fast-moving turning mirrors as opposed to a gantry cutting lasers that are moving mirrors and lens around the work area. As a result, CO2 galvo-based systems are typically four to six times faster than flatbeds for marking and engraving over almost any surface, especially over curves. Oftentimes, they are faster than that. So, if a single-sided mark is taking 3 1/2 to 4 minutes on a flatbed, expect the mark to take less than a minute on a galvo-based CO2 system.
Adding 3-D, or real-time dynamic focusing, in combination with the galvo moving mirrors is a fast and easy way to mark or engrave quickly without the complication of using a traditional rotary attachment.
Radian’s 3-D marking systems can do single-side marking on a curve without having to rotate the work piece.
With Radian’s 3-D marking platform, it’s as simple as selecting the type of curved surface to mark on. In this case, we’re going to select a cylinder. See Figure 1.
Figure 1
Once the proper diameter is selected the mark will take on the curve of the item to be marked. See Figure 2.
Figure 2
Then, simply place the item to be marked in the making field. Finish setting up the focus and any other laser marking parameter settings for the particular powder coating to be removed.
Note: Fill parameters such as line pacing (hatching), repeat rate, spot speed, laser power, and pulse frequency need to be set properly based on the type of material to be marked to receive optimal results.
The end result is unlike anything that you can produce on a flatbed without having to rotate the item to be engraved.
To learn more about 3-D marking on a curve using Radian Laser Systems, please visit www.radianlaser.com.