This article appears in the November issue of GRAPHICS PRO. To make sure you don’t miss out on other industry-focused pieces, subscribe today.
I believe that to understand the future, you must look at the past. This is my 18th year developing products specifically for the electric sign industry, and there has been a tremendous change.
When I started developing LEDs for commercial signage in 2003, I made a statement to a newspaper reporter that neon was a dinosaur. I was subsequently lectured by a few sign makers and tube benders that I was way out over my skis and that this LED thing was a flash in the pan.

Early LED systems were bare PCBs with wire in between. There were various voltages and power sources (everyone who has been around a while remembers the GE dip switches that set the voltage depending upon the color). As with most disruptive technologies, early systems were overpriced and underperforming; however, unlike their neon predecessor, they could adapt and create new form factors. LEDs stuck.
Early years
If you look back at the early years of LEDs in signs, the mission was simple: replace neon. Between 2000 and 2005, product development was focused on replacing the incumbent technology with modules in channel letters and rigid tubes in border applications. Between 2005 and 2010, flexible light tapes came onto the market to address needs in indoor signage, and flexible neon was developed as an alternative to exposed neon script. This second period really was around reducing costs, and around 2008, LEDs surpassed neon as the new lighting medium for the sign industry.
With LED manufacturers now in the pole position, they set their sights squarely on T-12 fluorescents, and again, everyone was skeptical. Just like during the heyday of LEDs in channel letters, there were a lot of systems out there for sign cabinets that varied from lattice to rail and module systems. What changed the cabinet market, particularly for sign retrofits, was when Principal LED came out with Stik that went straight into a socket. This product was preassembled in the USA, which allowed for a range of products “just in time” at a cost point that tipped the system. By the end of 2015, LEDs surpassed T-12 fluorescent lamps as the preferred technology of sign makers.
In 2015, however, technology development started to change, and between 2015 and today, direct material of LEDs and power sources began to be a smaller and smaller piece of the overall cost. It was now about system costs, and two major trends started in the industry.
The first was the development of 24V systems to reduce installation times and cost in large signs; the second was the use of kitting and preassembled systems for sign makers to reduce labor and time. Layered on top of this was a trend toward lower profile signs and the blurring of signage and architectural lighting, particularly in outdoor applications on and around building and gas canopies.
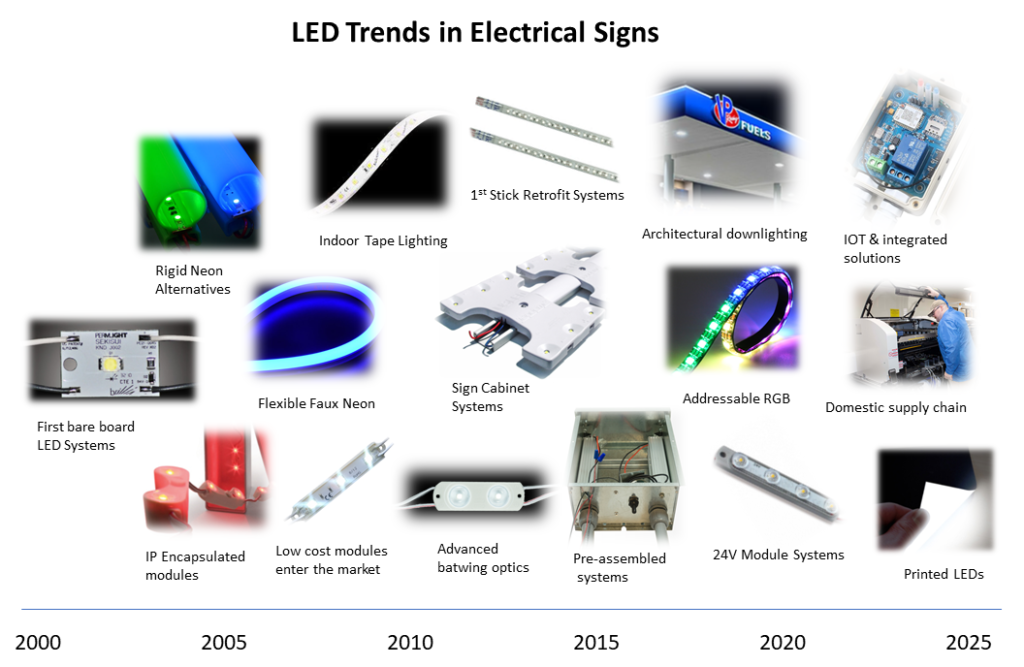
4 major trends
Now that we have looked back, it is time to look forward. I want to highlight four major trends that we’ll experience over the next five years. These trends are a natural extension of application expansion and sophistication of offerings.
Growth in the domestic supply chain. With the current tariff situation and continued geopolitical risk with China, I believe more LED, and electrical manufacturers will onshore a portion of their production to North America. Domestic products mean that the just-in-time benefits that U.S. assembly created in the retrofit and kitting market can be applied at the module level. This will result in more readily available product options in stock for the sign maker, such as a full range of colors and color temperatures, spacing options, and lens choices.
Blurring of the lines between signs and lighting. As LEDs have become commoditized and the costs are a small part of the overall sign system, end users are looking to light everything up on or around their building. Sign makers are the trusted advisor for those customers. They have a great opportunity to move beyond signs into a range of interesting architectural products, including downlighting, linear lighting, and RGB and color-changing systems. With the cost-effectiveness of addressable RGB modules and IP-rated strips, sign makers can now design and create a range of unique lighting effects. Bitro Group offers full-color animation with its LightSymphony Signature system. I anticipate this area of the market will continue to grow.
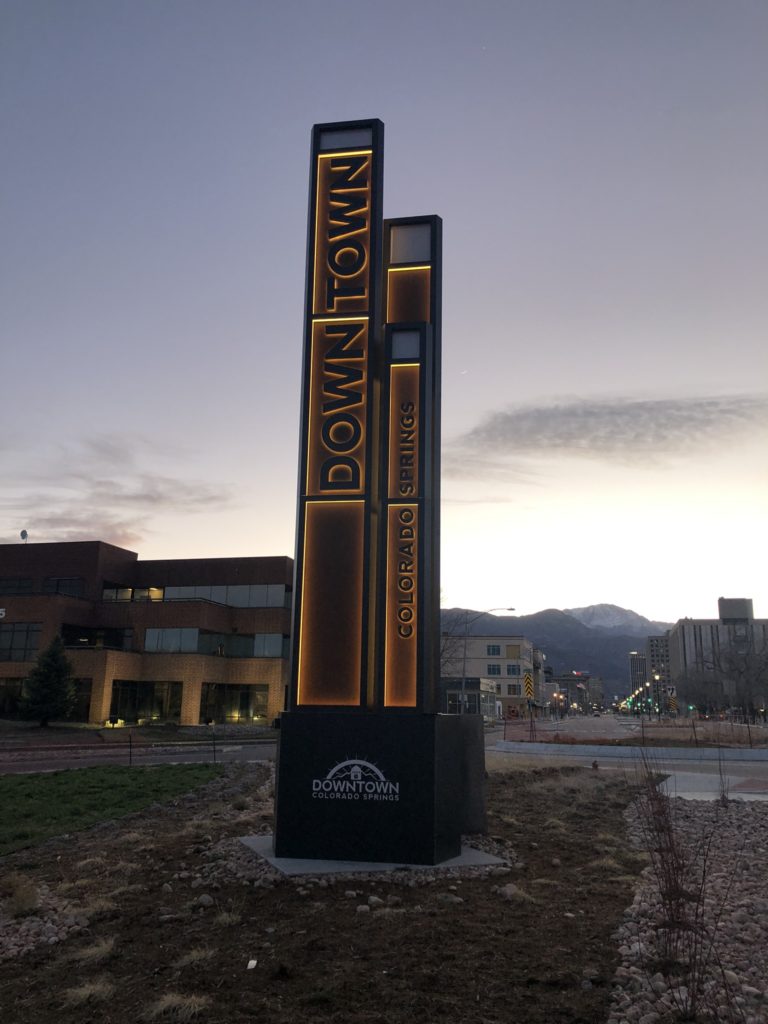
Integrated systems and IoT. One growing trend that will continue is the integration of systems and tools for sign makers. Most LED suppliers have a range of tools to help sign makers sell to end-users. These include ROI and energy savings calculators, as well as estimating software. At Principal LED, we have a rebate group that helps sign makers take advantage of energy rebates. Sign/LED Wizard, provider of LED layout software, now offers its integrated desktop product free of charge to sign makers. “…our production version allows sign makers to estimate costs of other materials and can be easily uploaded into a router to cut faces, and score and cut the back of the sign. We have plans to incorporate additional tools to assist in project management and sales,” says Jeff Fassett, VP of business development.
Another part of integration in the future will be incorporating IoT into sign applications. The idea of smart signs that monitor energy consumption and can report outages will continue to grow. Colite has developed its own cloud system called Signalytix for monitoring and tracking of signage programs.
Printed LED technology. Interestingly, I ended up learning about and helping develop printed LEDs when I worked at Dow Chemical 20 years ago. The technology was very new and has been slow to develop. However, there is no question that end-users and sign makers want lower profile signage, and LED modules are inherently point sources. The name of the game is light distribution, and printed LEDs could be a disruptor to discreet LED modules in the sign industry over the next five years. Several companies have recently made real improvements in this space, and though not a current trend, it is something to look out for.
Trendsetting
When you look back at the history of LEDs in the sign industry (or any technology for that matter), you see a classic cycle. LEDs have gone from replacing existing technology in neon and T-12 fluorescents to integration as a system, and now expansion of applications that offer a range of more sophisticated ways that they can be used. Lines between traditional architectural lighting and signage will continue to blur, and systems will continue to be more integrated and streamlined. Finally, be on the lookout for new technologies that move the cheese by creating new form factors or new manufacturing technologies and processes.