As wide-format inkjet printers continue to become more powerful and complex in terms of speed and what types of jobs they can produce, shop owners still need to keep their investments up and running and well-maintained. This is especially true when it comes to the unit’s ink system. Recent innovations in wide-format printer ink technologies have significantly enhanced performance and versatility.
“Ten years ago, signage printers (solvent or UV) were not capable of producing the higher-quality applications, expanded color gamut, or durability they are today,” said Reed Hecht, group product manager, Professional Imaging at Epson America. “This is in large part due to the improvements in ink formulas and printhead capabilities that have resulted in better color capabilities, durability, media compatibility — all which led to improving overall print quality and expanded applications,” he added.
More color options
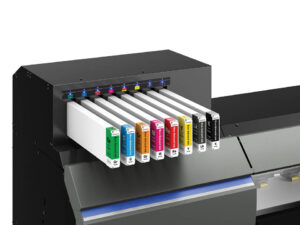
“One major trend is that solvent inks expanded their color gamut by adding additional colors such as green and improved print speeds,” reported Patrick Donigain, senior manager, LFP Business Planning & Strategy Group at Canon USA.
He pointed out that resin and latex inks offer environmentally-friendly options and have adopted the use of additional consumables such as optimizers and overcoats to improve dot gain control and scratch resistance.
“In addition, UV inks have evolved with greater adhesion and increased stretch. UV-gel inks combine UV curing principles with gel-based formulations, enabling instant curing, precise dot control, high print speeds, and versatile finishes like matte and gloss. These advancements collectively boost productivity and print quality across diverse applications,” he explained.
Sohil Singh, president of business development at StratoJet USA said the printing industry is undergoing remarkable transformations, with advancements in ink technology leading the charge. “From improving performance to addressing environmental concerns, ink manufacturers are developing formulations that cater to modern demands. There have been significant improvements in ink formulas, the types of inks suitable for different printing systems and applications, and essential maintenance practices to ensure excellent print performance.”
Singh noted that ink manufacturers are developing inks with better durability, adhesion, and versatility. “Modern inks adhere more effectively to various substrates, including plastics, textiles, and metals, ensuring superior resistance to environmental factors such as UV rays and moisture.”
“At the same time, eco-friendliness is a key focus, with water-based and soy-based inks reducing volatile organic compound (VOC) emissions. Innovations in pigment formulations are also contributing to richer, more vibrant colors, while faster drying times, achieved through UV-curable inks, are enhancing productivity in high-demand industries,” he added.
Brian Phipps, president and general manager at MUTOH America, agreed that ink manufacturers are making major strides in several key areas to enhance performance and meet evolving industry demands.
Eco-solvent ink
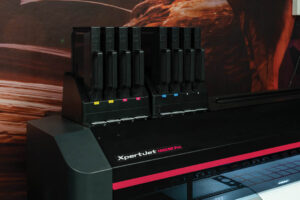
“Eco-solvent inks are seeing improvements in cure time, specifically in reducing the ‘outgas’ period before applying an overlaminate,” Phipps pointed out.
“Outgassing is critical to prevent silvering and separation. Traditional inks, depending on the vinyl manufacturer, recommend up to 24 hours of outgassing time before lamination. The big push as of late is getting toward the concept of ‘same day’ lamination or printing a piece in the morning and laminating before leaving for the day. Printer manufacturers have been working on ink chemistry, in tandem with vinyl manufacturers modifying the coatings, in some cases, outgassing has been reduced to six to eight hours,” explained Phipps.
He said that MUTOH’s eco-solvent ink is GREENGUARD Gold certified; this certification provides assurance that these inks meet stringent and comprehensive standards for low emissions of VOCs into indoor air. “Prints made with [these] inks are perfectly suited for indoor applications including office, classroom, and health care environments.”
UV ink
Phipps said a major improvement ink manufacturers are making to their UV inks is a longer shelf life, ensuring inks remain stable and usable for extended periods, reducing waste and costs. Additionally, an expanded color gamut allows for richer, more vibrant hues, providing greater accuracy and consistency in high-end printing applications.
MUTOH offers two distinct UV ink formulations to meet different application needs, Phipps noted.
“Rigid ink is designed for adhesion and durability on rigid materials like acrylic, glass, wood, metal, and PVC. It delivers high-opacity white ink, making it ideal for backlit and multilayer printing applications. Rigid ink is optimized for sharp detail, vibrant colors, and long-term outdoor performance, making it a top choice for ADA-compliant Braille signage, industrial labeling, and promotional products.”
He continued, “The other is flexible ink, which is engineered for applications requiring flexibility and stretch. Flexible ink adheres to curved, flexible, and roll-to-roll substrates. It prevents cracking or peeling, making it perfect for packaging, soft signage, and vehicle graphics. Additionally, it maintains excellent abrasion resistance and color stability, ensuring prints remain durable even under stress.”
Dye sublimation
Phipps said that dye-sublimation inks always seem to push the boundaries of a higher release with as little ink density as possible. “As dye-sublimation can become a waste-heavy, minimum-margin enterprise, using an ink formulation that releases more ink from the transfer paper and therefore allows less to be thrown away is key.”
Phipps noted that MUTOH’s dye-sublimation ink is engineered for high transfer efficiency, allowing for maximum color vibrancy with minimal ink consumption. “This results in reduced waste and lower production costs while maintaining sharp, vivid prints. [These] inks provide outstanding washability and colorfastness, ensuring that textiles and soft signage retain their brilliance even after repeated washing. These inks are also designed for smooth operation in MUTOH’s printers, reducing nozzle clogging and improving overall print consistency.”
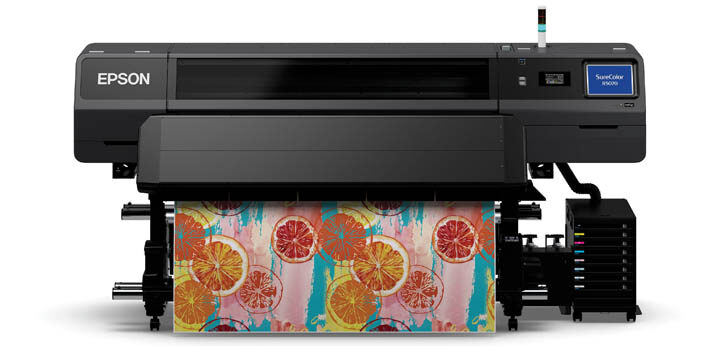
The right system for the right job
Different printing systems require specific inks for optimal performance and longevity. Phipps said, for example, that piezoelectric printhead systems offer versatility and precision, supporting UV, dye-sublimation, eco-solvent, and multipurpose inks.
“UV inks cure instantly under UV light, making them ideal for both rigid and flexible substrates. Dye-sublimation inks produce vibrant, long-lasting prints on textiles and coated materials, ensuring sharp detail and high color release efficiency. Eco-solvent inks deliver durable, weather-resistant prints, making them the preferred choice for signage, vehicle wraps, and outdoor graphics. Multi-purpose inks provide flexibility across different applications, ensuring strong adhesion and high-quality results on various substrates,” he explained.
When looking at applications, Donigain said that UV-cured inks are perfect for durable, versatile applications like signage and packaging due to their vibrant colors and quick curing. “Textile inks such as dye-sublimation and direct disperse dye inks are ideal for soft signage and apparel, offering vibrant colors. Latex, eco-solvent, and UV-gel inks are great for indoor/outdoor signage, vehicle wraps, and trade show displays,” he added.
Singh said when it comes to matching inks with printing systems, a thoughtful selection is crucial. “For example, dye-based inks excel in delivering vivid colors for inkjet printers, while pigment-based inks offer durability and water resistance. Offset printing benefits from oil-based inks, which produce sharp and consistent images. In screen printing, plastisol inks dominate textile printing, whereas water-based inks cater to eco-conscious applications.”
“For specific applications, UV-curable ink is a game changer, offering durability and color vibrancy on rigid substrates like glass, acrylic, and metal. Clean/latex/resin inks are versatile and eco-friendly, making them ideal for both indoor and outdoor applications,” he added.
Phipps agreed that the best ink choice depends on the printer type and application, and using the proper ink formulations ensures exceptional performance, durability, and color accuracy across all printing needs.
It’s all about the printheads
Roberts noted that when choosing the best inks for specific printing applications such as UV-cure, textile, latex, and eco-solvent, it’s essential to consider how the ink formulation interacts with the brand of printhead. “As both the manufacturer of the printers and the inks, we design our ink formulations to work perfectly with our technology, ensuring optimal performance.”
“We create inks specifically tailored to complement the capabilities of our printers. This strong relationship between ink and printhead technology guarantees excellent performance across various applications, delivering high-quality results that meet our customers’ needs,” Roberts said.
Hecht noted that Epson recognizes that customers have diverse needs and use printers differently, varying by application, even within the same product family. “Epson has traditionally offered customers a choice for ink cartridge size. For example, one of our models allows customers to select and install different-sized ink cartridges, ranging from 110mL to 700mL per cartridge, giving them options of price per mL and replacement timeframes. Similarly, our 64″ solvent printer offers customers the ability to install either 800mL or 1,500mL of any color ink packs to best suit workflow needs.”
Jay Roberts, UV specialist/application engineer at Roland DGA, added that Roland prioritizes the balance between ink formulation and printhead technology in their UV and eco-solvent printing systems, as this significantly influences print quality and durability.
“We ensure our UV inks are compatible with our printheads to prevent clogging and deliver consistent results. We also prioritize compatibility with our eco-solvent printheads to ensure reliability and high-quality output,” Roberts added.
Maintaining your investment
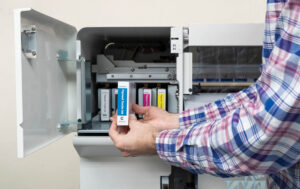
One of the biggest challenges with large-format printing is keeping heads clean and nozzles unblocked. “Evaporative inks have a higher propensity to dry on heads, so additional care needs to be taken by equipment manufacturers to ensure print quality,” explained Donigan. “White ink can be even more challenging, as its larger particles create more opportunities for clogs. Understanding how much manual head maintenance is needed and how much waste ink is used to maintain print quality is essential to understanding your productivity and running costs. Neglecting print head maintenance can be very costly.”
Donigain added that the type of preventative maintenance needed is very dependent on the printer and ink technology. He said that some printers can require 10-20 minutes per day of maintenance, while others might only need 10-20 minutes per month. “The most important thing is that you do the maintenance. If the manufacturer supplies a care-and-use poster, hang that next to the printer with a maintenance tracking sheet that operators sign off on. Too many print companies don’t put emphasis on this, which causes significant, unpredictable downtime and higher costs when parts fail prematurely. Automated maintenance is key and should be on your checklist of must-haves for your next printer.”
Many unique challenges
Singh said that wide-format inkjet printing presents unique maintenance challenges that demand attention. “Printhead clogging, often caused by ink residue, can compromise print quality, while contamination from incompatible or low-quality inks may damage the ink system, especially in UV inks. Environmental factors like temperature and humidity fluctuations can affect drying and adhesion, while regular wear and tear of components like wiper blades and capping stations require timely inspection and replacement.”
Singh pointed out that preventive maintenance practices are key to achieving consistent print performance and extending equipment lifespan. “Regular cleaning of printheads, rollers, and other components prevents ink buildup and ensures smooth operation. Shops should always use genuine consumables recommended by manufacturers to avoid compatibility issues. Maintaining optimal temperature and humidity levels in the printing environment is equally important. Routine checks, including nozzle inspections and calibration, can detect potential problems early, while scheduled professional servicing ensures that equipment runs at peak performance.”
Singh said the advancements in ink technology and the emphasis on maintenance are reshaping the printing landscape. “By selecting the right inks for specific applications and adhering to preventive measures, businesses can achieve superior print quality while optimizing operational efficiency. As the industry evolves, staying informed about innovations and best practices will remain a cornerstone for success.”
Roberts said it is good to make it a habit to clean the maintenance station daily. “Regularly wipe down the capping and wiper blades to avoid dry ink buildup and clogs that could lead to print head failures. Keeping print heads capped when not in use helps prevent ink from drying and causing blockages.”
“Also, be sure to remove any debris regularly. Clearing away ink residue and debris around the print heads and maintenance station helps avoid contamination and ensures smooth operation. By following these simple maintenance steps, shops can improve print quality and extend the lifespan of their wide-format inkjet printers,” Roberts added.
When in doubt, check the manual
Hecht said all wide-format printers will come with their own set of recommended preventative maintenance, so users are advised to consult the user manual and their dealer to best assess what is needed. “The most common preventative maintenance includes timed printhead cleanings and replacing user-replaceable parts such as maintenance tanks, capping stations, and fabric wipers. If the printer uses white ink technology, then it will require timely agitation to ensure no sediment settles in the ink cartridge (or pack). The dealer/installer should tell customers all recommended preventative maintenance. Staying on top of these tasks will help to prolong the life of the printer and ensure consistent, high-quality output.”
Phipps said that consistent maintenance is essential to ensuring high-quality output and maximizing the lifespan of both the printer and ink system. He said most UV-LED printers require daily maintenance, including ink agitation to keep pigments properly dispersed, ensuring consistent color and adhesion. Regular cleaning of printheads, wipers, and cap tops prevents nozzle clogging and maintains sharp, high-resolution prints.
Phipps added that preventing downtime and ink settling are two things to look out for. “Wide-format inkjet printing systems are designed for continuous operation. If the printer is idle for too long, liquid inks can change in viscosity and chemistry, leading to nozzle clogs, color shifts, and print defects. [Some inks] are engineered for stability and smooth ink flow, reducing the risk of settling and ensuring vibrant, reliable output. Automatic cleaning cycles in printers help maintain proper ink flow and prevent common maintenance issues.”
Phipps offered several tips for shops:
- Protect the printhead: the heart of the printer
To maintain peak performance, regular cleaning of printheads, capping stations, and wiper blades is essential to prevent ink buildup and nozzle obstructions. - Optimize ink flow for consistent results: Replacing key components such as cap tops, dampers, and wipers at recommended intervals helps maintain ink consistency and prevent drying or clogging. Additionally, built-in automatic cleaning cycles keep the ink system running smoothly with minimal intervention.
- Maintain a stable environment: Monitoring environmental factors like temperature and humidity also helps maintain ink performance. It’s best to keep your printers in a controlled environment, where temperature and humidity are regulated to prevent ink viscosity changes and ensure accurate color reproduction. Proper ventilation also extends the lifespan of both the printer hardware and ink system.
- Manufacturer-supported guidelines and training: Phipps said most companies provide detailed written and video maintenance guides, ensuring operators have the knowledge needed to keep their printers in peak condition. Intuitive printer design, combined with easy-to-follow maintenance steps, helps shops reduce downtime and maintain consistent, high-quality output.
“By following these preventative maintenance steps, shops can keep their printer running at full capacity, extend the life of their printer, and achieve consistently stunning print results,” Phipps concluded.