Ink Technology: Ink Choices for Wrap Shops
Learn how different chemistries can impact your work
The vehicle wrapping industry is maintaining its strong growth momentum as more and more print service providers (PSPs) add this special segment of commercial graphics to their revenue stream. No one would have believed that the first auto wraps done in the early 1990s (credit to KPMF in the UK, based on most accounts) would be so pervasive in our everyday life.
The improvement of media—primarily vinyl (PVC), as well as urethane and other non-PVC films—in conjunction with adhesive improvements, and the addition of air-egress technology has created a practical solution to perfectly wrap a vehicle. More recently, evolutionary changes to the printing process (inks and print technology) have made tremendous inroads contributing to the explosion of wraps from the early beginnings, to the continued growth trends and market expectations into the future.
This article looks at the types of digital inks used for the creation of primarily vehicle wrap graphics. It also looks at some of the developments to print technology at a very high level, and how these changes have made for greater adoption of transforming technologies. There also has been a migration from some of the original pioneering technologies as newer technologies emerge or competing technologies improve. The inks described either are current proven technologies used in vehicle wrapping or are new entries looking to make a mark.
True solvent inks
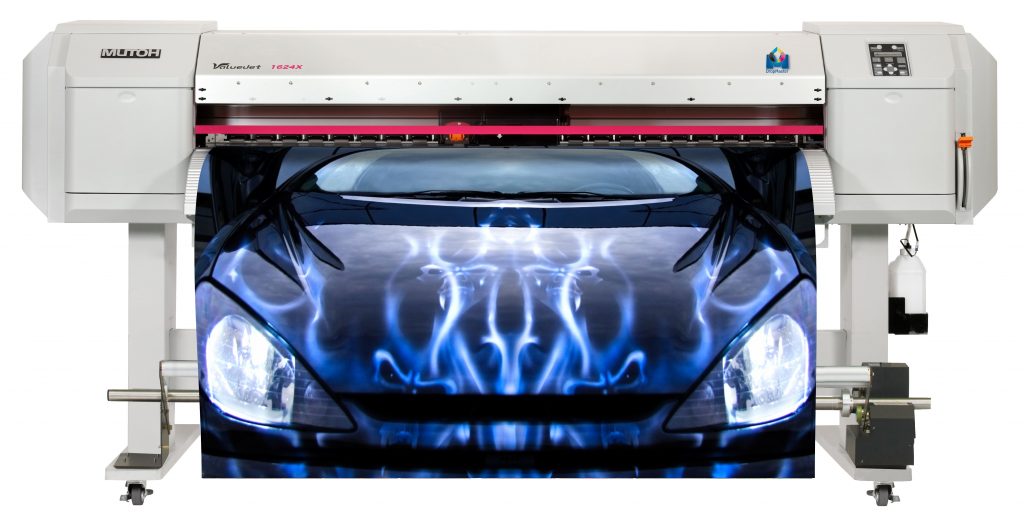
True solvent inks were the first inks that could print directly on uncoated vinyl and films. When looking at the ink formula, it typically has a combination of solvents, pigments, and resins. The strong VOCs (volatile organic compounds) of these inks (like cyclohexanone, or 2-butoxethanol acetate) are very flammable, require venting from the printer platform, and need long periods between printing and lamination, or even baking. These inks are very durable and have been used for vehicle wraps in the past. They adhere well to most vinyl-based print media without issue. However, because of their volatility, VOC issues and related venting requirements, and the sometimes-high investment in the physical printer, the technology has been on the decline-especially as better solutions become available.
Eco/light-solvent inks
The advent of eco/light solvent inks revolutionized the digital commercial wide-format printing world for wraps. Changes to the types of less-intense VOCs (like some glycol ethers, and lactone solvents) in these inks have eliminated the need for venting and the need for baking to cure the inks.
Typically, many of these inks still require 12-24 hours of drying before lamination, but this could be achieved by loosely unwinding rolls and allowing proper airflow to evacuate the solvents and cure the inks.
However, some ink and equipment manufacturers have reformulated newer generations of these inks, changing the solvent packages. These newer developments in the inks now require significantly less time to cure/dry, from 1/2 to 1/4 of previously recommended times before lamination. These and other improvements have made the eco-solvent and light-solvent inks very popular in the commercial vehicle wrap markets.
UV-cure inks
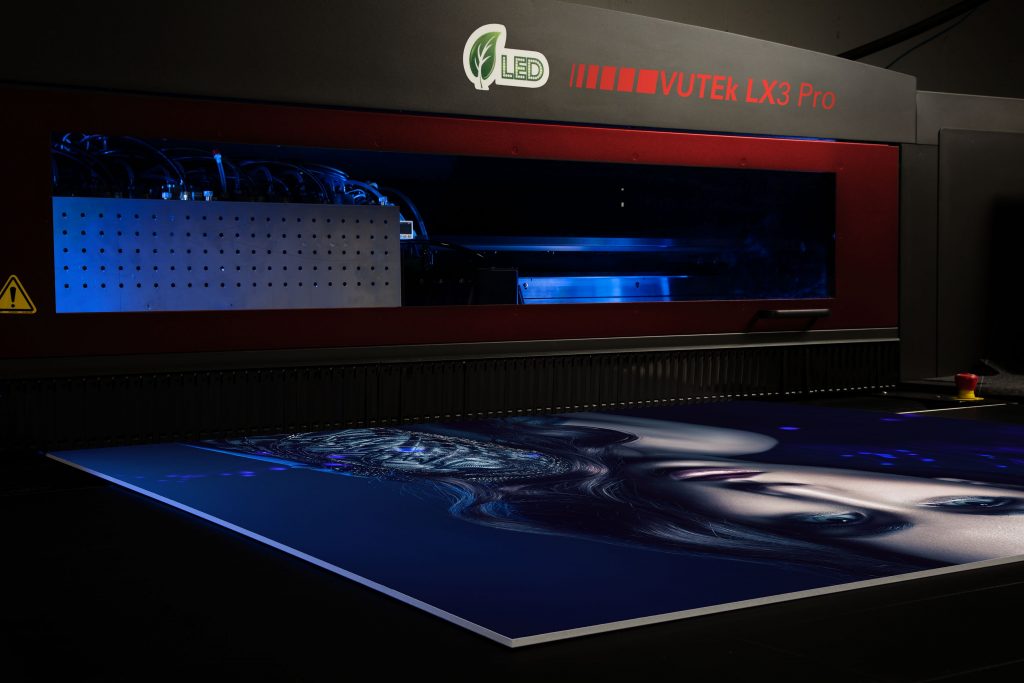
The technology behind UV-cure inks is complex. Rather than a solvent-based carrier that needs time to dry, UV-cure inks combine a variety of photo-initiators, oligomers, and monomers (and pigment-based colorants) in a suspension that instantly cures into a solid polymer when exposed to UV light. Basically, the UV light excites the photo-initiators, which causes the monomers to chemically bond with the oligomers to form a polymer. Very different from solvent or eco-solvent ink chemistry.
Original UV inks required the UV source to come from high-powered arc lamps that created an intense wide-spectrum of UV light and extreme heat outputs. These features made it difficult to print onto many heat-sensitive substrates as the media could be distorted by the heat. In addition, the inks were very thick and created a “texture” as the ink piles do not flatten out like many other technologies. Also, the ink of a UV-cured image tends to be too brittle for vehicle wrapping requirements—though it has proved a perfect solution for rigid-board printing.
In recent years, manufacturers of printers, UV-cure units, and inks have changed over to low-heat LED-based UV cure-lamps (and new LED-sensitive ink sets) in order to reduce temperatures, increase image quality, and have greater elongation (stretchability) of the inks.
All these factors have helped UV-cure printers and inks make inroads into the commercial wraps markets. New LED UV-cure units and ink developments make compound curves and other difficulties encountered in wraps no longer the impediment they used to be for UV-printed media.
Latex inks
Latex inks (also known as aqueous-resin inks) and the printers that deliver them are relatively new on the market when compared to solvent and eco/light-solvent inks—newer even than digital UV-curable inks. HP was the first to develop this latex printing technology and has made steady inroads into the wraps market ever since. Steady printer improvements and step-change formulation advancements in the inks have helped latex printing systems to become the growth leader for printer sales among commercial PSPs.
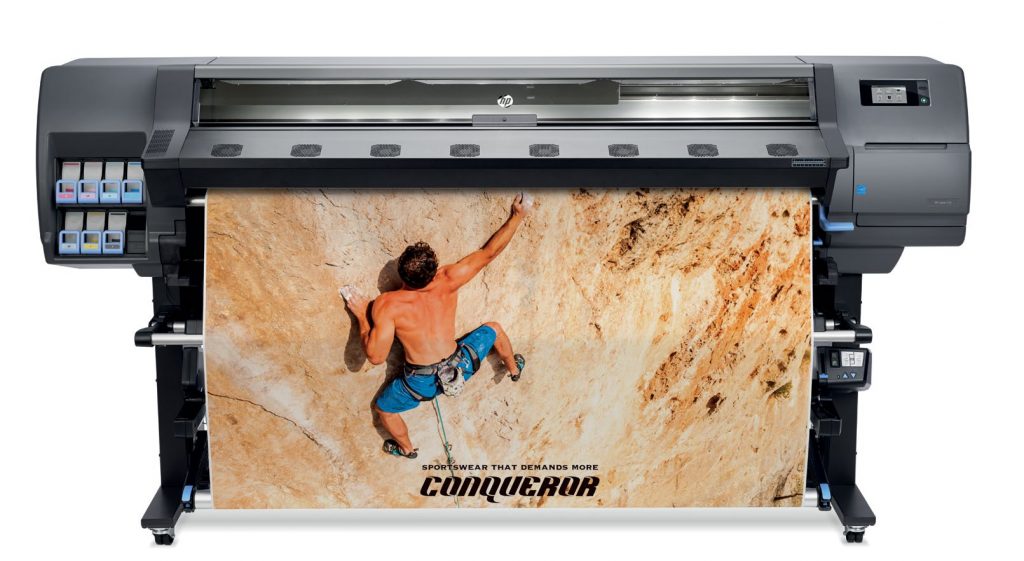
The inks themselves do not have typical VOCs, do not require venting and are dry right off the printer. The printer does, however, require a heating platen on the printer to drive the water out of the ink formula after printing.
Besides being a “greener” solution for commercial printing, latex printing allows fresh prints to be laminated within minutes of printing, which allows for a quicker turnaround of customer requests.
Presently, there are relatively few latex printer/ink manufacturers in this technology space. HP continues to improve performance, processing, and speeds with new generations of inks and printers. However, the competition looks to increase in this technology space, providing additional viable alternatives for PSPs to consider.
UV gel
New on the scene are UV-cured gel inks. The system is very fast, high quality, and an interesting technology that uses gel UV inks that do not produce dot gain on the printed surface. Developed by Canon/Océ, these specialized LED UV-curing inks have the safety profile of LED UV-cured systems, excellent color gamut, and are attracting a great deal of attention. Although this technology has not yet proven itself in the vehicle wraps market, it will certainly be a participant in display, wall, and floor wraps applications. The new method of drop and cure is a harbinger of technological advances that we can come to expect from the major printer and ink manufacturers in the future.
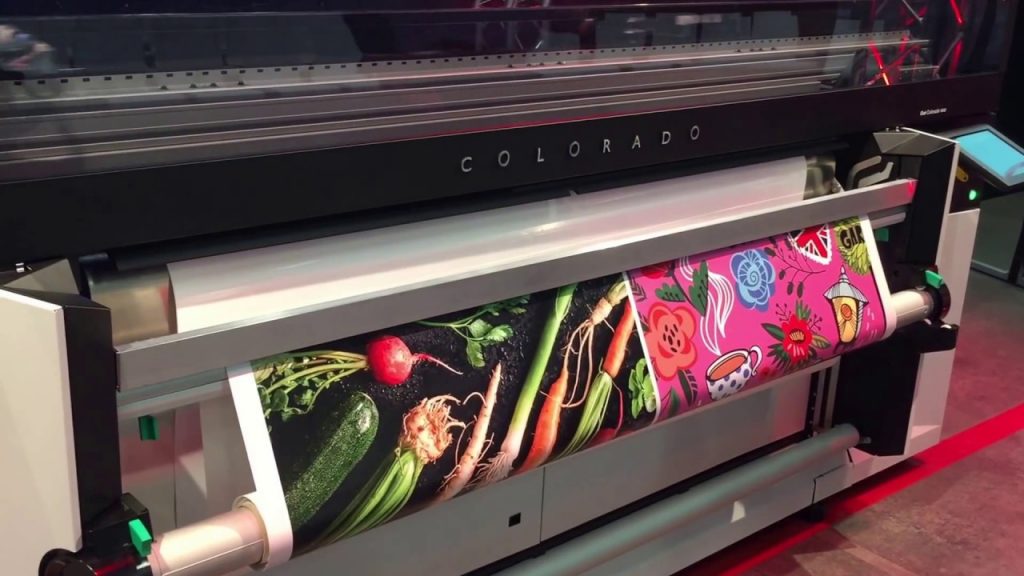
The future of ink and printing technology looks exciting as we see manufacturers invest in technological improvements in equipment and formulations. All the competitors in the digital print market are looking to change the paradigms, and show us new technologies to make us rethink how we look at graphics creation.
Ever-increasing demands for greener alternatives, faster technologies, and greater durability will drive change, and as the costs of newer and greener printing come into closer alignment with existing technologies, adoption will increase. History has shown us that as we improve technology through speed, ecological, durability, and end-value proposition improvements, PSPs and end-user customers will embrace the evolution.