Heat is king in the dye-sublimation world. To fixate the dyes to the fabric, they must first be heated to approximately 400˚F for at least 30 seconds. For that, you need a good-quality heat press or calendar unit. Any variation in consistency of time, temperature, and/or pressure can impact color, ruin the job, and in the end, cost you money. Thus, understanding the equipment necessary to achieve effective dye sublimation and rich output is one of the most important steps you can take.
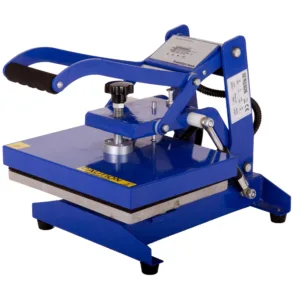
This is the third in our five-part series that explores the intricacies of dye-sublimation with Mike Syverson, National Textile Manager for Durst Image Technology. Mike has more than 20 years of experience in the printing industry and was instrumental in the development and implementation of the first grand-format dye-sublimation printer in 2001. In this article, we will discuss the heat press and calendar equipment that is used in the signage and graphics industry, as well as other applications. The final articles in the series will explore finishing, marketplace economics, and workflow.
Q: What does a heat press/calendar machine do, and why is it important in the dye-sublimation process?
A: The primary purpose of a heat press or calendar is to facilitate the sublimation of dyes into fabric. These devices have a heated element and some sort of feature to apply pressure to the transfer paper and fabric to convert the ink to gas (sublimate) and have it permeate the fibers of the polyester fabric (or polyester coating). This is a required step in the dye-sublimation process as the dyes are not fixated until they have been heated at a certain temperature for a certain amount of time.
Q: The terms “heat press” and “calendar” are frequently interchanged. Can you explain the difference?
A: Although the function of a heat press and a calendar in dye-sublimation are basically the same—fixate the colors into fabric—the fundamental difference is that a calendar is designed for roll-to-roll sublimating, typically for rolled textiles and more commonly used in the graphics and apparel industries. A heat press is designed for one-off images. Heat presses come in many different sizes and designs depending on the specific application. There are flatbed-heat presses that can be used for one-off flat prints such as mouse pads, glass or ceramic tiles, or other specialty small graphics. There are also circular heat presses with a curved heating element for imaging on to a mug or a baseball cap, for example.
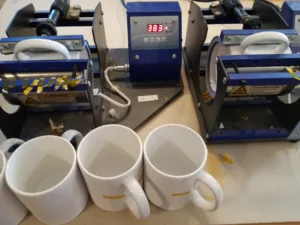
The most common heat presses are clamshell and swing-away units. A clamshell opens from the rear and the platen opens at an angle to allow access to your image area. This is good for small imprintable items and garments. The swing-away style raises and lowers the platen vertically and swings to one side and is usually used for rigid surfaces. Some of these presses are automatic in that they will close and open on a timer, so you have precise control of your transfers. Many units are fully manual. These are much more popular as they require a lower initial investment. Finally, there are units designed for transferring onto T-shirts. These have a shuttle-type system so you can stage a T-shirt on a jig while one is transferring. If you are producing short-run T-shirts, this is a good method. On the larger scale, there are also large format flatbed heat presses that work very similar in principle to the smaller clamshell systems but are designed for producing sublimated graphics up to 5’ x 10’ (and even larger on some custom units).
There are many choices for calendars, as well. They are available in several different widths and can come with many options, such as a staging table for setting up flexible sheeted goods, multiple roll functionality, different diameter drums, auto shutdown timers, blanket or belt lengths, and a variety of other enhancements. There are also beltless calendars specifically for direct printing that don’t require transfer paper. However, you may need protection paper if you’re working with delicate fabrics.
Q: What is a flatbed heat press, how does it work, and what applications is it best used for?
A: Flatbed heat presses are designed for sheeted applications only. The presses can range in size from small 11”x14” presses to 5’ x 10’ presses with two full-size beds. They usually have a bed where the substrates and transfer paper are laid out.
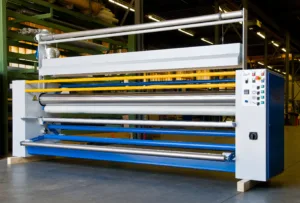
Above the bed is a heated platen that is lowered on the substrate. This bed is heated to approximately 400˚F and is lowered on to the substrate with an amount of pressure sufficient to sublimate the inks into the donor substrates. The pressure and time can be changed based on the substrate. Some of these devices are manually actuated, while some of the more sophisticated devices have electronic or pneumatic systems for raising or lowering the platen. Many of the smaller products, such as gifts, promotional items, and specialty graphics are imaged with the smaller units. Some larger shops use the bigger presses for higher volume products. A 4’ x 8’ press can be used to set up 32 12” tiles with one large sheet of transfer paper to create custom tiled mosaics, for example. The units with two 4’ x 8’ beds are designed so you are laying out one print while the other is sublimating, creating a more efficient workflow.
Q: What is a rotary calendar and how does it work? What applications is it best used for?
A: A rotary calendar is designed for output onto flexible substrates, such as rolled fabrics. Its operation is similar to a laminator. There is a continuous blanket (or belt) that wraps around a heated cylinder. Fabric and transfer paper are put together and set upon this blanket. The blanket carries the fabric and paper and presses it against the heated drum for a given time to sublimate the image to the fabric. The blanket also has pressure applied to it against the drum to help facilitate the process. The advantage of this device is that is can be used for high-volume rolled goods (and some select sheet materials).
Because the material is wrapping around a heated cylinder, items such as coated tiles or other rigid materials cannot be sublimated with this process. For rigid materials, you must use a heat press. Calendars are ideal for the big production textile industry as well as large-format graphics such as exhibition signage, banners, exterior/interior design displays, and upholstery.
Q: What is “protection paper” and why is it used? Is it different than transfer paper?
A: Protection paper, or tissue paper, is used on a calendar or heat press to protect either the drum/platen or the blanket from ink sublimating onto it. It absorbs excess gases that do not sublimate into the substrate. If, for example, you did not use tissue paper on the blanket of your calendar and ink sublimated through the fabric into the blanket, there is a possibility the ink in the blanket would re-sublimate back into the fabric the next time that spot in the blanket wrapped around and contacted the fabric. This is a very important component to use on the calendar to extend the life of the blanket and prevent any unwanted offsetting of ink onto your printed graphics.
Q: What should a print shop owner look for when purchasing a calendar and/or heat press?
A: There are many things to consider when choosing a calendar or heat press.
For calendars you need to consider:
- The width—The calendar should match up in terms of width with the output device being used. Calendars are available in sizes from 64” up to 16’ wide. Many shops will purchase a calendar that is wider than their current output device in the event they decide down the road to purchase a wider printing device. Companies will purchase the calendar and keep it many more years than a printer so anticipated growth should be considered when purchasing.
- Maximum capacity—Calendars have a cylindrical drum that is heated. The diameter of this drum determines the speed of the calendar, as fabric needs a certain amount of contact time with the drum to achieve proper fixation. The bigger the diameter, the faster it will produce graphics.
- How the drum is heated—Most calendar units these days have a drum filled with oil that is heated to approximately 400˚F. You want a calendar that uses oil because it produces a very even heat across the width of the unit and the temperature will stay very stable. Calendars with electrically heated drums can cause hot spots in the fabric and some units cannot keep up with the transfer speed in terms of heat. Hot spots can cause color differences and a variance in temperature from the beginning to the end of a print.
- The length of the printing blanket or belt—The longer the belt, the steadier it runs through the calendar. The belt will tend to wander and move which must be corrected and different machines have different ways of handling that. Some machines use a pushing and pulling mechanism that tends to damage the belt over time. Others use an electrical steering arm that moves up and down which doesn’t damage the belt and extends its lifetime.
Image courtesy of Klieverik. For heat presses, the following areas need to be considered:
- Size of press bed—How large do you need the press to be? It again depends on the application.
- Heating element—Most heat presses use an aluminum upper heating element with a heat rod or heating wire attached or cast into it. Make sure the heating element heats evenly and can keep consistent heat. Where many heat presses are one-off type machines, it is easier to maintain heat as you can let the press heat back while you are staging your next print.
- Warranties—You should expect at least a one-year warranty on your purchased piece of equipment in addition to training and installation.
Q: How does using a transfer press differ from an inline sublimation solution?
A: Transfer presses have historically provided better-finished products than their inline counterparts, although the latest generation of inline dye-sublimation printers have dramatically closed the gap. An inline system is designed to directly print on the fabric and sublimate it on a board printer, without having to move the printed fabric to the stand-alone heat press. This has many advantages in terms of lowering the operational and capital costs of the heat press in addition to the extra labor and wasted material loading and unloading two devices can create. That said, there are still many reasons to have a stand-alone heat press. Some fabrics, such as high-stretch fabric, or most décor fabrics, are not suitable for direct printing and benefit from a traditional transfer paper workflow. Additionally, any rigid item much be printed with transfer paper if it’s to be sublimated.
Q: How can a shop owner justify the cost of the calendar versus that of a heat press? What are the particular benefits?
A: The choice between a flatbed heat press versus a calendar unit is rather simple. It depends on the applications. If a shop owner is producing soft signage (banners, flags, etc.), then a rotary calendar is the way to go. If a shop is producing nothing but small garments, gifts and promotional items, then a flatbed press is more appropriate. Several shops that have rotary calendars may also have a small heat press for proofing small files or testing different applications. The smaller heat presses are relatively inexpensive and cost much less to operate than a 10’ rotary calendar.