Earlier this spring, a houseboat named Miller Time was disassembled and transported 800 miles from Lake Powell, in Arizona, to Bullards Bar Reservoir, in Dobbins, California, where it received a new facelift and a new name. Now named ‘AVI8TER’, this 60′ Sumerset houseboat boasts an open entertaining upper deck with two radar arch structures and an additional captain’s control seat.
Having weathered several decades under the scorching desert sun, AVI8TER arrived with a stressed gel coat, cracking paint, and oxidizing characteristics, akin to older RVs or trailers, albeit floating on water. Despite the challenges, we accomplished this labor-intensive project with the right equipment, team, and execution plan.
When my company, WrapStar Pro, received the request for an estimate, I felt that as an experienced boat wrap expert, I brought a wealth of knowledge to the table. With 12 years of experience wrapping boats of all sizes, including houseboats, our company was well-equipped for the task ahead. Despite shifting focus towards large commercial fleet accounts post-COVID-19, my own personal passion for water and wake surfing motivates me to undertake boat projects whenever possible.
After a thorough evaluation of AVI8TER’s conditions and precise measurements, the client and I devised a comprehensive installation schedule. This included coordinating with a professional mobile detailer, Something Vicious Detailing, to perform an acid wash, effectively removing oxidation from the boat’s surface where the wrap would be installed.
Acid wash, known for its efficacy in eliminating the white chalk film on old gel coat/composite bodies, requires a combination of heavy-duty acid and cool temperatures for successful removal. Fortunately, the weather cooperated, and this crucial step was completed quickly. Recognizing the importance of addressing other potential issues, such as silicone and flaking paint, we ensured that all flaking paint was meticulously sanded, and all silicone removed before the wrap installation. Understanding that proper preparation is key to success, we emphasized the significance of thorough prep work and the additional labor involved.
Wrap challenge No. 1
Three weeks before the scheduled installation date, the client notified us that the marina had imposed a hard deadline of April 8 for the boat to be transported to the water. This marked the onset of challenge No. 1. The unexpected development presented a challenge for my team and required a new strategy for wrapping the boat while it was docked on the water. Despite the urgency, the primary focus was on installing the stripe on the side of the hull before the boat’s immersion.
Recognizing the potential risks associated with direct heat on a metal hull and the likelihood of rubbing against the dock or adjacent boats causing scratches on the vinyl, we opted for FlexiShield Gloss black PPF for enhanced protection and durability. However, weather conditions took an abrupt turn from cool to snowing during the installation of the FlexiShield black stripe. Undeterred by the adverse weather and the lack of power access, our team worked diligently, using torches to ensure the stripes were installed with the utmost precision and adhesion.
Challenge No. 2
The second challenge involved selecting the appropriate vinyl for the project. With my involvement in assisting Arlon Graphics with the development of their new VITAL product line, emphasis was placed on the superiority of non-PVC films for aquatic vessels. Unlike traditional PVC films, non-PVC options don’t brown or crack, ensuring longevity and durability in marine environments. These films offer extended horizontal and vertical protection, along with added heat resistance for enhanced UV and acid dew protection.
Think of it as a printable paint protection film. After thorough evaluation, VITAL DPF V9700 and series V3370 media from Arlon was recommended for its FLITE technology, guaranteeing slidable adhesive and lite initial tack. The combination of FLITE technology, lite initial tack, repositionability, and easy liner release made it the optimal choice for the project.
Challenge No. 3
Challenge No. 3 centered on selecting the appropriate printer for the task. WrapStar Pro uses Roland printers, specifically VG3s with CcMmYKkO solvent inks and AP printers with CMYK resin inks. Given the boat’s gel coat surface and the presence of silicone, which can hinder vinyl adhesion if not adequately removed, careful consideration was required. The design’s predominantly dark color scheme necessitated the use of printers with heavier pigment ink, such as the solvent printer, to ensure optimal adhesion. Solvent inks, known for their deeper penetration into media, were preferred over resin inks, as they closely approximate the adhesive layer.
Additionally, the black and light black ink combination produces true grays, ensuring they are free from hues of blue, magenta, or green, thus maintaining color accuracy. Moreover, the use of cyan and light cyan inks enhanced the vibrancy of the blues in the design.
Print production proceeded smoothly for the team, and we meticulously planned the installation process. The side of the boat, referred to as the “container,” measured 40′, which equated to 10 to 11 52″ vertical panels. With a team of two installers working on the side, we strategically pre-seamed three panels at a time, specifically panels one through three, four through six, and seven through nine, while tape registering panels three through four, six through seven, and nine through 10. This streamlined approach significantly expedited the installation process, eliminating the need to align each panel individually.
Given the uncertainty of weather conditions, our team prioritized efficiency to avoid wasting time aligning panels in adverse conditions such as wind or bright sunlight. Furthermore, we opted to begin with the panels displaying the name ‘AVI8TER’ (panels four through six) to ensure the alignment of the word before proceeding with the installation of the remaining panels. Seam direction was deemed unimportant in this installation, as the boat primarily remained stationary or moved to a new anchor spot, minimizing any potential impact from directional wind or boat speed on the seams.
Challenge No. 4
A fourth challenge arose as the threat of rain loomed on the horizon, scheduled to arrive on day two of the installation. On day one, the team encountered another minor setback as the boat was not docked upon their arrival, delaying their progress. Consequently, we anticipated needing to compensate for this lost time on day two. Despite knowing that rain was imminent, the forecast predicted only 0.05″ of precipitation and only in the early morning hours.
To preempt any potential issues, the team secured all finished edges with silicone and taped exposed seams to prevent water infiltration under the wrap. They also strategically left the panels untrimmed at the bottom, allowing water to slide off the sides rather than pooling on top of the rub rails.
Day two brought pouring rain, posing a significant setback. While waiting for the rain to subside, our crew utilized their time by tending to trim pieces on both front and rear patios, as well as wrapping the rear side of the container. They carefully navigated around the rain showers, managing to install the next major panels on the side when conditions permitted. Despite the challenges, by the end of day two, both 40′ sides, the rear, and part of the front were successfully completed. However, half a day was lost due to weather delays, extending the originally planned three-day project to three and a half days.
On day three, the team smoothly wrapped up the lower sections before moving on to the upper deck. By midday on day four every detail, from the radar arches to the nose cone and captain’s control dash, received meticulous attention.
Project complete
As AVI8TER emerged from its transformative wrap project, it revealed not just a new look but also underscored the dedication and expertise of the WrapStar Pro team. Through careful planning and innovative problem-solving, our crew navigated unforeseen challenges, showcasing our resilience and commitment to excellence. With the final touches completed, AVI8TER now embodies a perfect blend of style, durability, and functionality, ready for countless adventures on the water.
For me, the AVI8TER project reaffirmed the WrapStar Pro crew’s leadership, and it proved that with passion, ingenuity, and a skilled team, any vision can become reality. This project helped set a new standard of craftsmanship in boat wraps, and it has left a lasting impression on both the client and admirers of AVI8TER’s stunning transformation.
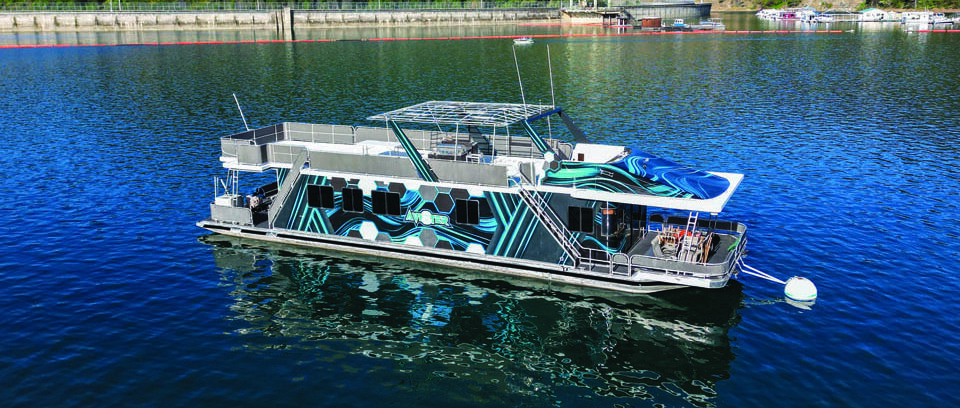