Ditch the Defaults for Ink Savings
Find out how adjusting your RIP settings could help reduce ink consumption.
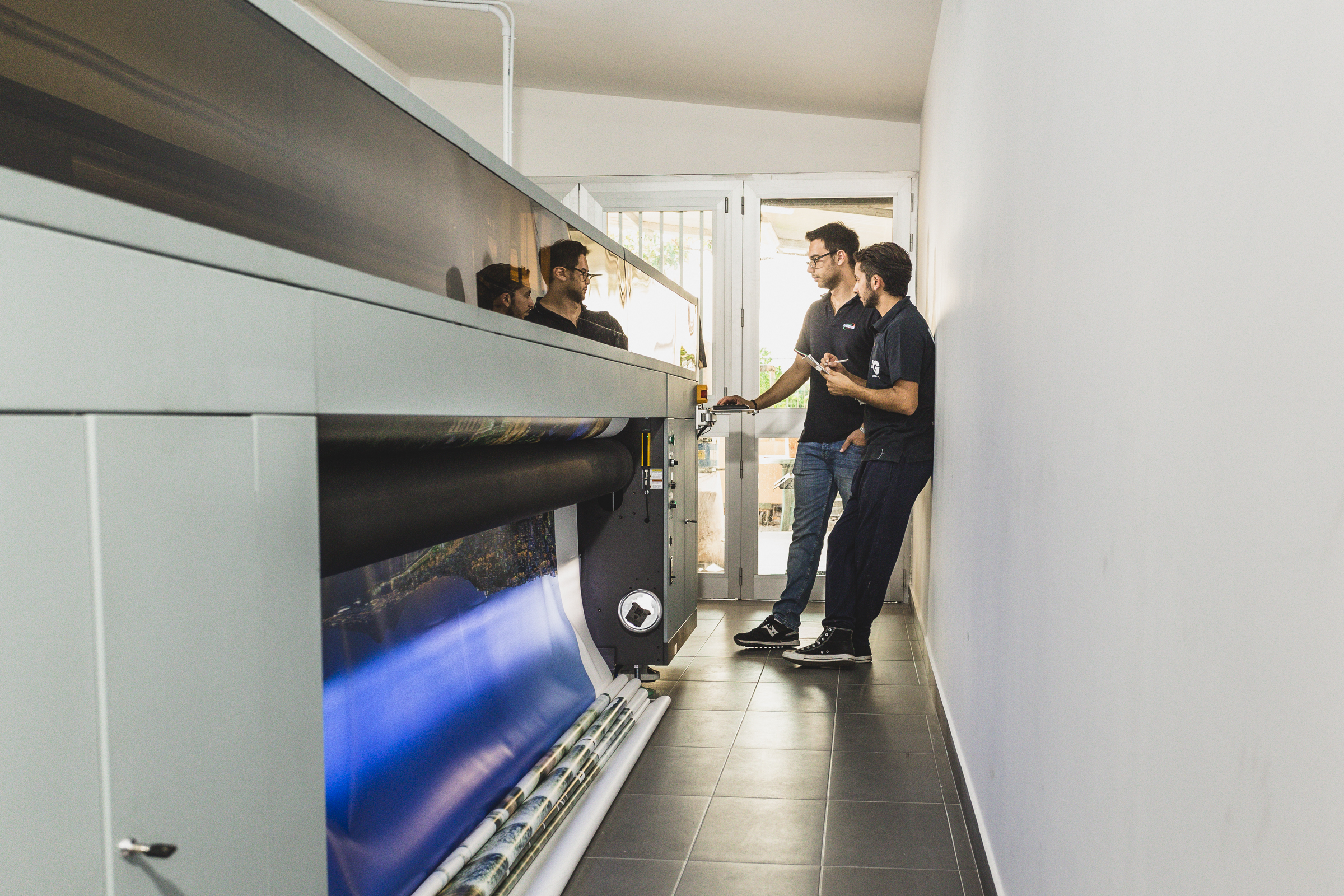
Each time you examine your fixed costs-especially when you spend an evening doing some “what can we do to save money this year” budgeting-you’ll probably find that ink remains a considerable, unavoidable, and ever-increasing expense.
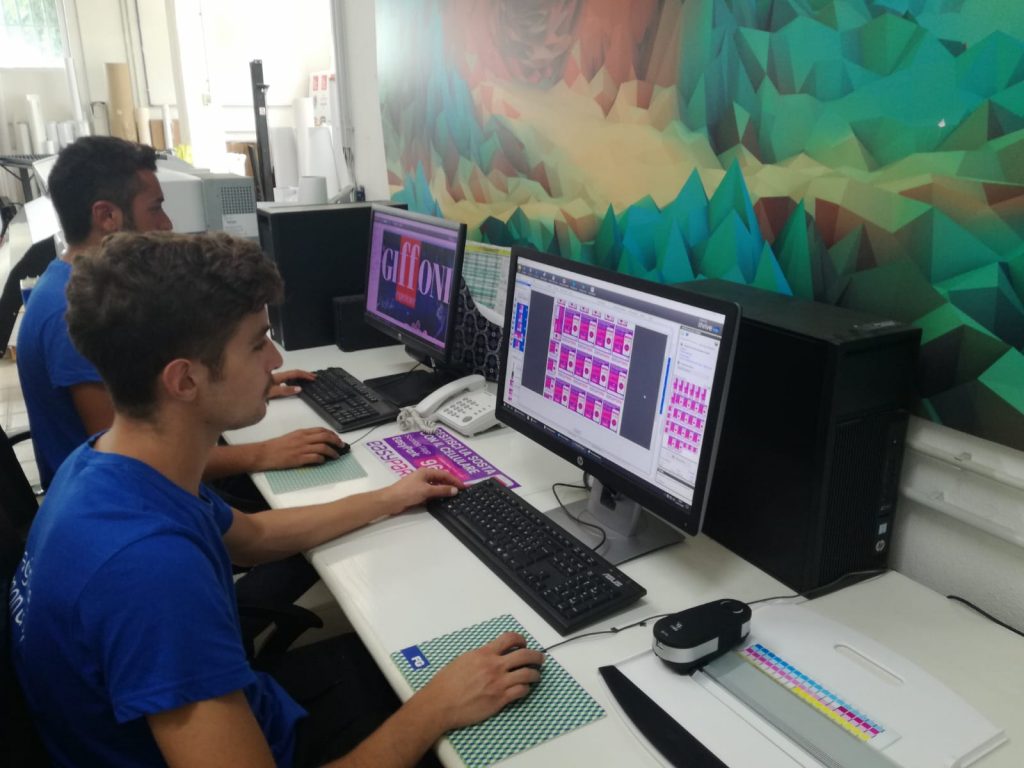
But what if you could take a few simple steps for each print job, no matter whether you’re using eco-solvent, UV-cure, or latex inks, and save as much as 30% of your overall ink bill? Would that be enough incentive to take the time to tweak those settings, or make sure your operators are up to speed on best practices for ink conservation?
A quartet of industry experts, including those in the ink-manufacturing end of the business, say the secrets lie in your printer’s own built-in capabilities to use less ink. And if you’ve been simply using the built-in defaults on your RIP software, customizing those settings can provide noticeable savings.
Tim Mitchell, HP, says that the many benefits of latex printing technology also produce plenty of redundancies in the CMYK process, often causing you to use more resources than necessary.
“Don’t print with more ink than you need,” Mitchell says. “The goal of printing is to hit your maximum gamut with the smallest amount of ink possible. That way, your printing can be more efficient and your runs faster, and the ink will also dry faster.”
Mitchell’s three must-do moves for saving ink on latex jobs include modifying your settings governing ink restriction and global ink limits, as well as switching from six-color CMYK to four-color, when possible.
“Those light hues, light cyan, and light magenta do not get used a lot, especially on large volume printers, where everything matters,” he says. “Ink restriction is also important-you could achieve maximum density or a maximum chroma value much earlier than 100 percent. If the restrictions are too high, that could result in a distortion of linearization. Ink restriction is a key factor for high speed when liquidity is crucial, as well.”
For UV-curing printer equipment, Mark Goodearl, EFI, says purging and ink waste management is critical, and that means proper operating training can ultimately produce big savings.
“Customers who invest in training their printer and pre-press operators are able to prepare their own custom ink profiles to get more mileage from their ink,” he says. “Knowing proper head-tending procedures-when to purge and how to do it properly, or knowing when to use certain print modes or the various types of multi-layer printing-can also reduce ink consumption without reducing the quality of the print.”
With the right training, Goodearl says purging can be virtually avoided, cutting back on a substantial source of waste.
“Incorrect or excessive purging may be the single most wasteful and expensive thing an uneducated printer operator can do,” he adds. “One excessive cause of waste may be that it seems easier to perform a ‘purge all’ for 20 or 30 seconds instead of opting to run a jet test, evaluate the issue and take more appropriate action.”
Goodearl also recommends printers put a little more focus on their inventory, monitoring and maintaining supplies to avoid running out entirely-resulting in expensive downtime-or ending up with surplus or aged-out inventory, leading to expensive waste.
Better ink usage can also be achieved by working with the software that drives your image-making. Jonathan Rogers, Onyx Graphics, says that using that built-in color management software as part of the end-to-end RIP and print workflow is a very efficient way to maximize ink usage. Too many users, he says, start with the wrong default profiles, bad color management or simply too much ink, resulting in unnecessary waste.
“Within the software solution, these concerns can be alleviated with correct ICC profiles for the type of ink and media used for each print job,” he says. “We’ve seen customers with up to 30 percent savings by using technologies such as GCR+ found in Onyx software. Combine this with the ability to correct color for accurate and consistent output, removing bad prints or the need for reworks, and the savings can be significantly higher.”
Rogers says using new process control tools such as ColorCheck in the preview process will help ensure color accuracy and consistency, and can validate the output quality long before printing, reducing waste.
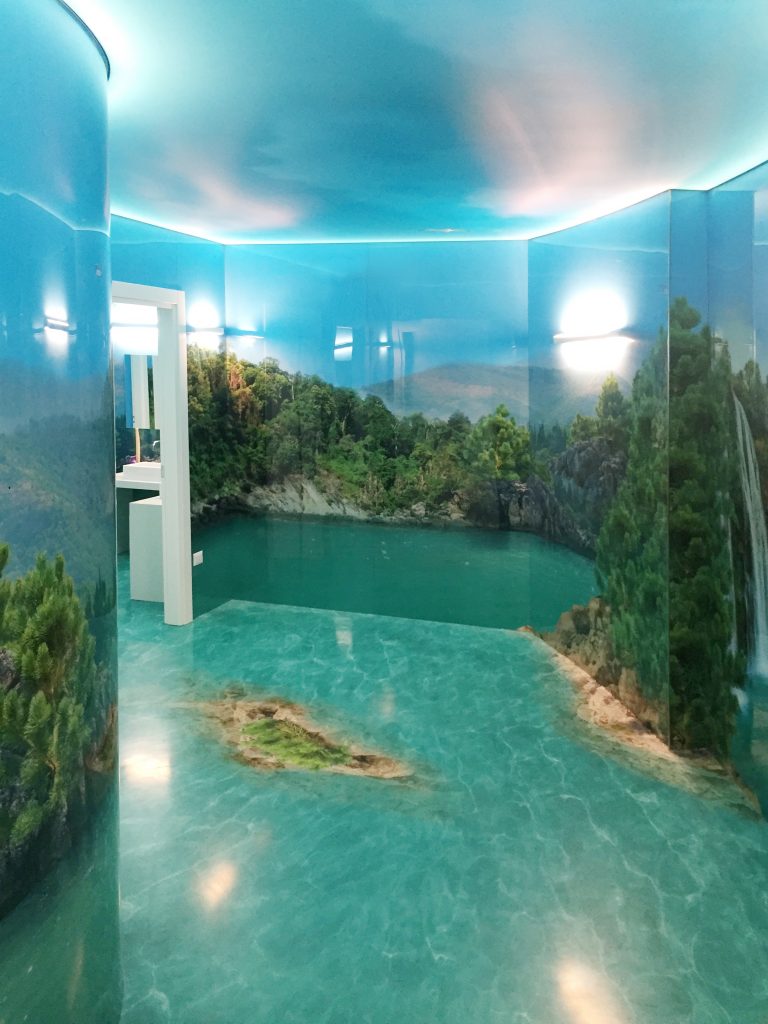
HP’s Mitchell is a big advocate of using solutions such as Onyx’s technology to cut down on ink usage before a file is even sent. He’s had great results using GCR+ in the ICC creation process, helping the printer to optimize the quality and look of single colors, using the Color Engine, designed specifically for wide-format printing.
“Latex inks are very rich, especially black, and you honestly don’t always need to use cyan, yellow and magenta, which used to be the case with solvent ink. You’re really just making the printer work harder.”
Mitchell says the ICC process also provides the opportunity to program to print entirely in pure hues, which is once again very helpful and ink-conserving in primarily black jobs.
“Your RIPs provide the ability to send in a single color, by programming the black text as 000100. The RIP sees that and prints in black only, which will produce beautiful, rich text without needless waste of ink.”
Even the ink-makers are keen on printers optimizing their process to cut down on waste. Javier Robles, INX International, is also an advocate for software that avoids multi-color overkill for single color black output, saving users between 5 and 30 percent of their ink spend. And don’t forget some old-fashioned, hands-on maintenance, he says.
“Keeping equipment in optimum condition can also reduce ink purges and improve appearance, allowing faster print modes and reducing ink usage at the same time,” Robles says. “People get into problems when there is a lack of a comprehensive maintenance plan, or regular measurement and tracking of print quality using some sort of control strip.”
And what’s the best way to train your staff, especially new operators? Onyx’s Rogers says employees can take certified training in color management, which will help operators understand common mistakes and avoid them, as well as optimizing automated workflows to reduce manual error. An array of online tools and even a dedicated YouTube channel also provide up-to-date tips.