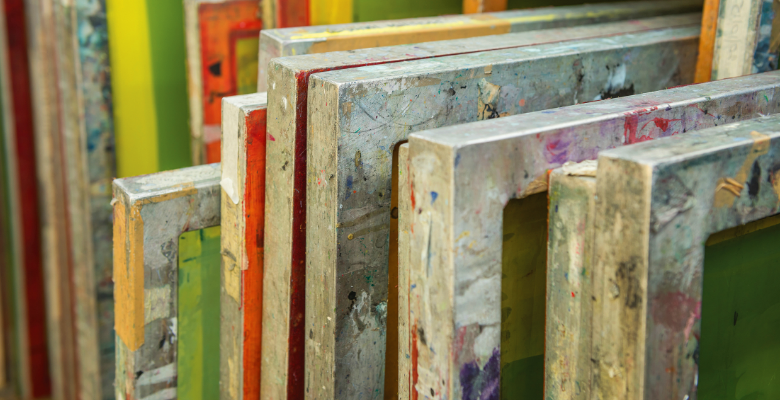
Recently, I’ve been reading a lot of forum and Facebook group posts about whether or not shops should be using a dip tank system to reclaim their screens. The answer to whether or not you should be using a tank is yes!
Now, I don’t want to sound condescending to non-dip tank users, and I’ve had many conversations with printers and employees on why they have reservations on using the tank over hand cleaning. I hear you, and I think they are entirely valid points. The unfortunate part to me is there is a huge amount of misinformation and lack of education on how the system works. This leads to misuse, dead chemical, and a stinky vat of sludge that ends up taking up space in your reclaim area.
Reclaim chemistry takes precision, patience, and an acute understanding of how these compounds and agents work together to do a specific task in the reclaim process. And to top it off, it’s all happening on a microscopic level that we can’t see. Pretty daunting stuff, right? I think so. Not the kind of things I’d seek out for fun, but with a little knowledge of how the compounds in the reclaim area can work for us, we can save ourselves a lot of headaches, time, and best of all-money.
First, here’s a quick overview on what a dip tank system actually does if you are not familiar. A dip tank system is a two- to three-step process that involves dipping used screens in a bath of solution that breaks down the ink and emulsion to a point where they soften enough to be liquefied and drain safe once sprayed with a pressurized water stream. The purpose of the tank is not to take anything off of the screen. It is just meant to begin the breaking down process. Tanks are their own ecosystems and need to be maintained and cared for as such. The addition of things left in tanks (due to screens sitting for too long) overworks the chemicals that are trying to break down the ink and emulsion. If you neglect to care for your tank, its performance will suffer.
How long should my tank last?
Hypothetically, with proper care, a tank should last indefinitely. Realistically, the average I’ve seen a tank remain effective and efficient with only small amounts of “dosing” is six to eight months. I’ve seen them last longer, but with regular use, you are going to inevitably experience a weakening of product effectiveness due to outside compounds building up inside.
Here are some tips for prolonging your chemical’s life in the dip tank:
- Keep the lid on whenever you are not using it.
- Only allow screens to soak for the recommended time your chemical manufacturer suggests.
- Use a fish net with an extra-long handle to scoop any residue from the tank before use. In between uses, any solids will sink to the bottom and become easier to strain out.
- Keep your tank in a temperature-controlled environment if possible. Typically, the tank will react slower in colder temperatures, so ideally keep it near room temperature.
- Don’t mix with other cleaners or other chemicals. If you use an on-press cleaner to do a color change or clean a trouble area on a screen, make sure you rinse any chemical off before putting it in the dip tank.
- Don’t allow any foreign metal objects in your tank. Aluminum, of course, is acceptable, but chemicals and metals don’t usually play nice together. Remember, the less foreign “agents” you introduce to your tank the more stable its ecosystem will be.
- Sing love songs to your tank at the top of your lungs while using the power washer. There’s no hard science that this will help but it can’t hurt, and no one can really hear you over the power washer.
How many screens should I expect to clean per hour with a dip tank?
If ink globs and tape are removed from the screens, you should be reclaiming somewhere between 20-30 screens an hour with one dip tank and a single screen washout booth. I’ve done this myself and have worked with a lot of shops to get there. To some, this number might seem high, but honestly, if you are not getting close to these numbers you are likely spending too much on labor during reclaim.
Reclaim isn’t an area where you want to sink a lot of labor cost, but it is also an area that needs to have a high standard of quality control. If screens are not being correctly reclaimed and cared for, you are destined to deal with headaches somewhere down the line in your process.
How many screens should I put in my tank at a time?
I’m going to let you in on a dirty secret. Chemical companies want to sell you as much product as possible. Crazy idea, right? This includes extra-large dip tanks that will fit many screens at a time. It sounds great in theory. More is better, right? Not so fast. Knowing what we now know about maintaining our tanks, loading them up with as many screens as possible shouldn’t be something we do. You should only “dip” as many screens as can fit in your washout booths. If you load four screens into your tank and only have room to wash out one at a time, the other three will sit for too long leaving behind ink and emulsion that your tank will keep processing and it will eventually struggle to keep up.
Also, be wary of specific emulsion/ink remover combo products. While it can be a huge benefit to cut down on cost by having a two-in-one product be sure the chemicals will not “battle” each other while in the tank together. The best solution I’ve found is emulsion removers with a detergent or surfactant that helps liquify the ink without using another acid. These compounds don’t seem to have any issue working together over time.
Now that we know a little bit more about how dip tanks work and how they can better work for us, I’d encourage everyone to give it a try or second chance. Again, reclaim isn’t an area where you want to sink a lot of money, time, or labor costs. We should be working towards making this process as efficient and cheap as possible while still maintaining high, quality standards. The faster you can get this process figured out the quicker you can focus on printing and making money.
See an example video of a dip tank system and how it works: https://youtu.be/YuklhOnQRLc.