No matter if you just started your career as an engraving/blasting specialist, there is always room for improvement on every level. There is no such thing as a “one material fits all applications.”
And yes, even for those of you who have been doing this for some time, we know how easy it is to get in a rut and stick with materials and procedures exactly the way we learned to do and use in the beginning. There is nothing wrong with that, except that you might be missing out on being able to work smarter and more efficiently, which ultimately means you could be earning more money for the time you spend on any given job. In this article, I want to focus on an important work component, which is the mask or stencil material you are using.
From the beginning
For a lot of people, the decision on which mask they are going to use is actually done backward. What do I mean by that? Well, for the greater number of those getting started, they usually end up with a masking material they received with the purchase of their blasting or engraving system.
The determining factor is usually made by asking a few questions about which products you intend to make. Fair enough, but what is usually ignored is the fact that hardly anyone sticks to the initial products they mentioned.
In fact, most of us quickly realize that there is a whole world of products out there that can be blasted/engraved, and guess what? The material you probably ended up buying initially may not be the best choice for some of the products you want to make.
The decision of the masking material to be used really should be made on the basis of the question: “What are you going to be blasting/engraving on, and what is your method of blasting/engraving?” Let’s take a look at some of the possibilities.
Masks for blasting
First of all, you want to determine what you are going to be blasting on, and second, which technique is going to be used. The simplest of these choices is working on glass and, most likely glasswear and/or award blanks or metal. For this scenario, the mask of choice would be any type of photoresist.
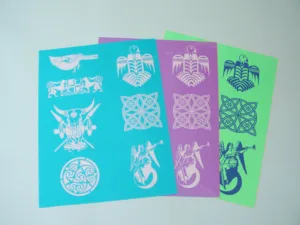
Most of you are familiar with the brands available and have probably have a product of your choice. It would be useful to investigate the different materials on the market. Why? Because you may not use the best choice for what you are going to do.
If a single blast stage is all you do, then you can ignore my next ruminations. Should you want to blast deeply and/or in a couple of stages, then you should be aware that there are different thicknesses of photoresist available, which allow you to do just that.
Some photoresists are more flexible than others, which may play a role if you are working on curved surfaces and or, heaven forbid, having to deal with compound curves. In these cases, you definitely want a more pliable resist that will conform.
Should you be interested in blasting halftones, then a completely different mask is called for, one that can hold very fine detail since you are working with a very fine dot pattern. These masks are usually much thinner than the regular photoresists (2 mil).
Should you be interested in blasting on stone, then the requirement for the right mask lies more with the thicker versions, as one usually ends up blasting more deeply into stone and adding color-filling to the product. This could mean switching to a 5 or 6-mil version of photoresist. In special cases, you could even go with a thicker film in 9 mil or so, if great depth is to be achieved, like on some monuments.
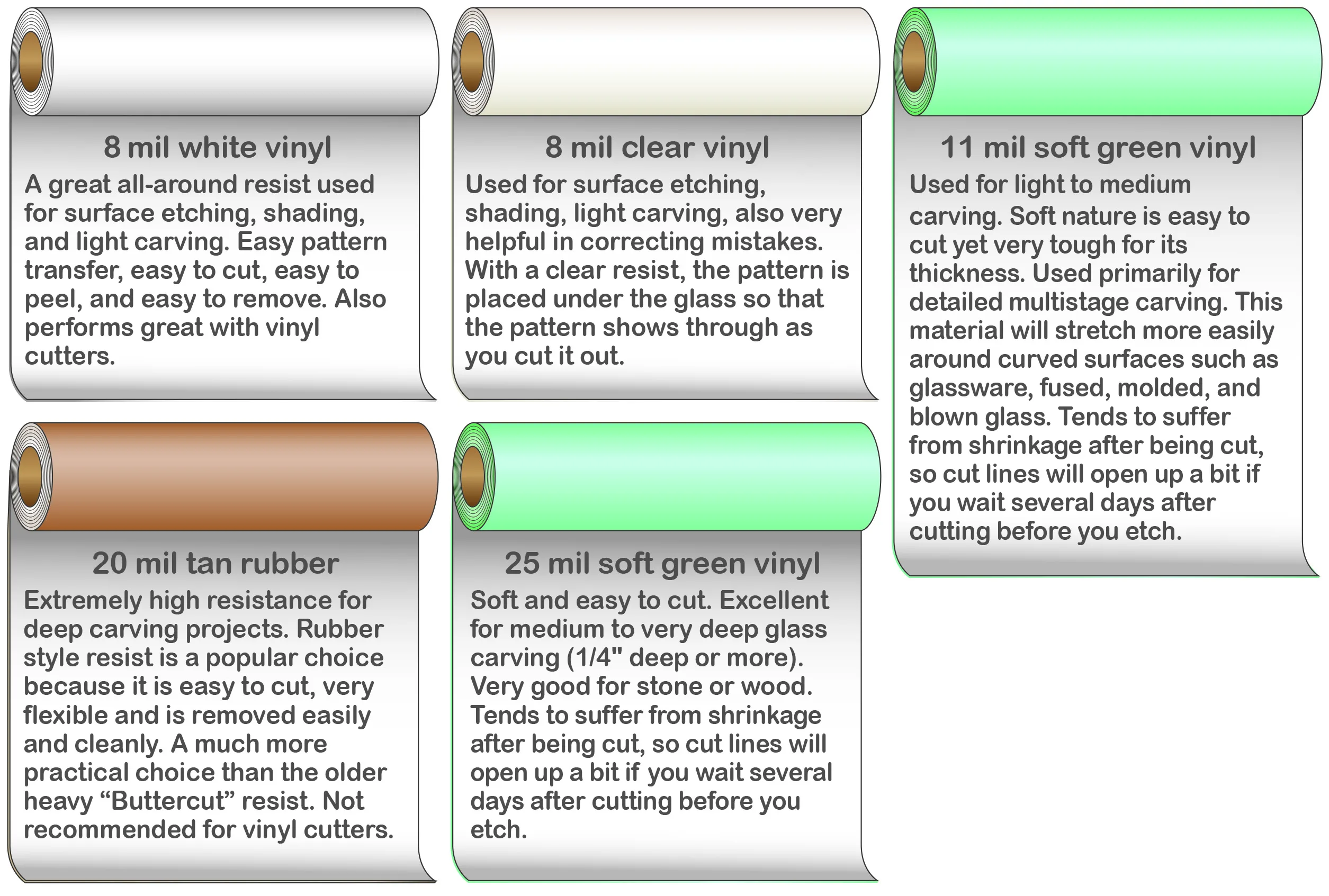
If you are employing a laser for your work method, then you may want to consider using a special mask created just for this purpose. By using this type of masking, you can use your laser to create the image in the resist material while also imaging the object at the same time; you simply adhere the mask to the product and use your laser to do the work.
These masks are specially formulated for laser and do not contain any PVC, which otherwise would cause your mirrors to fog up. Please pay attention to the manufacturer guidelines, which inform you which setting to use for the wattage of your laser.
These laser tapes are available in three different colors: green, blue, or orange. Why, you ask? Well, the darker colors were first on the market, and then the manufacturers heard that the dark colors were not very visible on dark wine bottles or stone. The orange makes it easier to see.
Should you fall into the unusual category of an art-based blasting business, meaning that you often employ the multi-stage techniques of carving and shading on glass, then there is another whole slew of resist materials to consider.
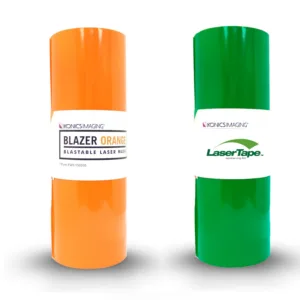
For simple surface blasting on a larger scale, we commonly use vinyl specifically created for this purpose. What do I mean by that? Well, these mask materials are formulated to have an adhesive which is just aggressive enough to stay on the surface to be blasted but not so strong that it would be hard to remove after blasting and potentially leave adhesive on the surface of the product, which then would have to be cleaned off, creating an extra step in your procedure.
Vinyls come in two types: hard and soft. The harder versions are good on any flat surface, like glass and polished stone. On rough surfaces, you want to switch to a soft vinyl, which conforms to those surfaces better and grips on an uneven surface much better.
The hard vinyls come in 6 and 8 mil thicknesses, and the soft ones in 10, 25, and 30 mils. If you see a vinyl with 3 or 4 mil, do not use it because those are sign vinyls with super aggressive adhesives, which will cause you a lot of grief in the removal stage.
For super deep blasting on natural stones with rough surfaces and in doing deep multiple-stage carving we sometimes resort to using a very pliable rubber resist that is 20 mils thick. It conforms to just about anything and will stand a lot of abuse which happens during prolonged blasting.
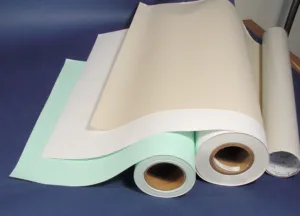
All of these latter materials are not suitable for lasers as they contain PVC or worse. Also, should you use a plotter for design cutting in your mask material, then you will find that the hard and soft vinyls can be cut on a plotter with a special knife angle, but the rubber resist cannot. The rubber resist is so soft that any knife blade, no matter how slow your plotter cuts, gets caught in the soft material and gets tangled up. Also, the cutlines are not visible in the rubber resist, even with an application of colorant. Any material sticks to the resist and can’t be cleaned off.
I hope this gives you an overview of a few materials that are available for our line of work. Make good choices, and your process will be easy!