Laser Power Upgrades Explained: Pros, Cons & Best Practices
You need to find a laser system that gives you the results you need
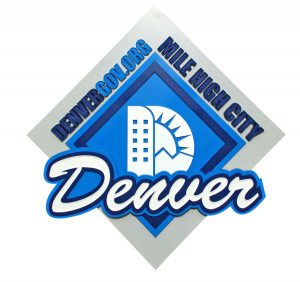
Upgrading a laser engraving machine may seem like a way to handle a larger workload, expand offerings and bring in more business, but in some cases, too much power might not be the best option.
“It is important to choose an initial system configuration that gives you the quality results you need,” says James Rabideau, strategic planner for Universal Laser Systems. “Speed is secondary. If a laser system does not produce the quality you need, then making it faster adds no value.”
Laser system operations
Laser systems use lasers instead of blades to engrave or cut images, words and shapes from a variety of substrates, from acrylic to metal, for clean, accurate lines. The systems have a wide variety of applications, such as fabricating metal and plastic, engraving plaques and awards, and cutting acrylic for point-of-purchase displays and commercial signs.
“It’s sort of like a glorified printer, but instead of using ink, you’re using a laser beam to engrave on or cut the material,” says Derek Kern, president of Kern Laser Systems.
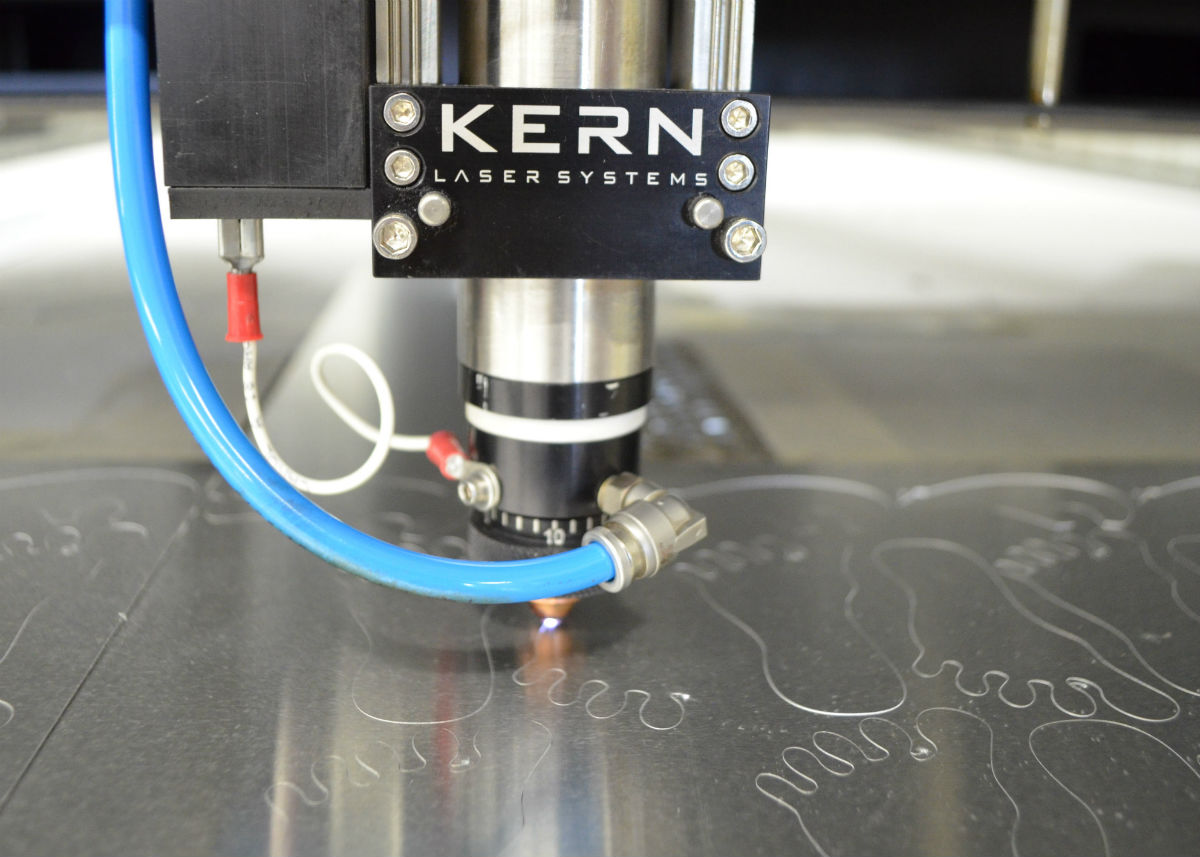
With engraving, a laser beam moves back and forth to create an image, similar to the movement of an inkjet printer head, and with cutting, the beam moves in lines and curves similar to how a router controls a cutting head, Rabideau explains. The laser removes material with both the engraving and cutting processes, set at the desired depth for engraving, or to penetrate completely through the materials in the case of cutting.
“We call laser engravers ‘laser material processing systems’ because they do more than engrave,” Rabideau adds.
Two popular types of laser systems include the flatbed and the galvanometer, or galvo. Flatbed laser systems are operated by a computer and allow the choice of graphic software to create image files. Flatbeds, operating about 10 times slower than Galvo systems, operate on an X and Y axis in a generous work area and can handle batches and large-sized jobs with a quick changeover.
“A laser engraving and cutting system will vaporize and modify the surface of most materials with the laser beam,” according to David Stevens, industrial applications manager at Trotec Laser Inc. “This creates contrast to the workpiece, or you can cut through it all together.”
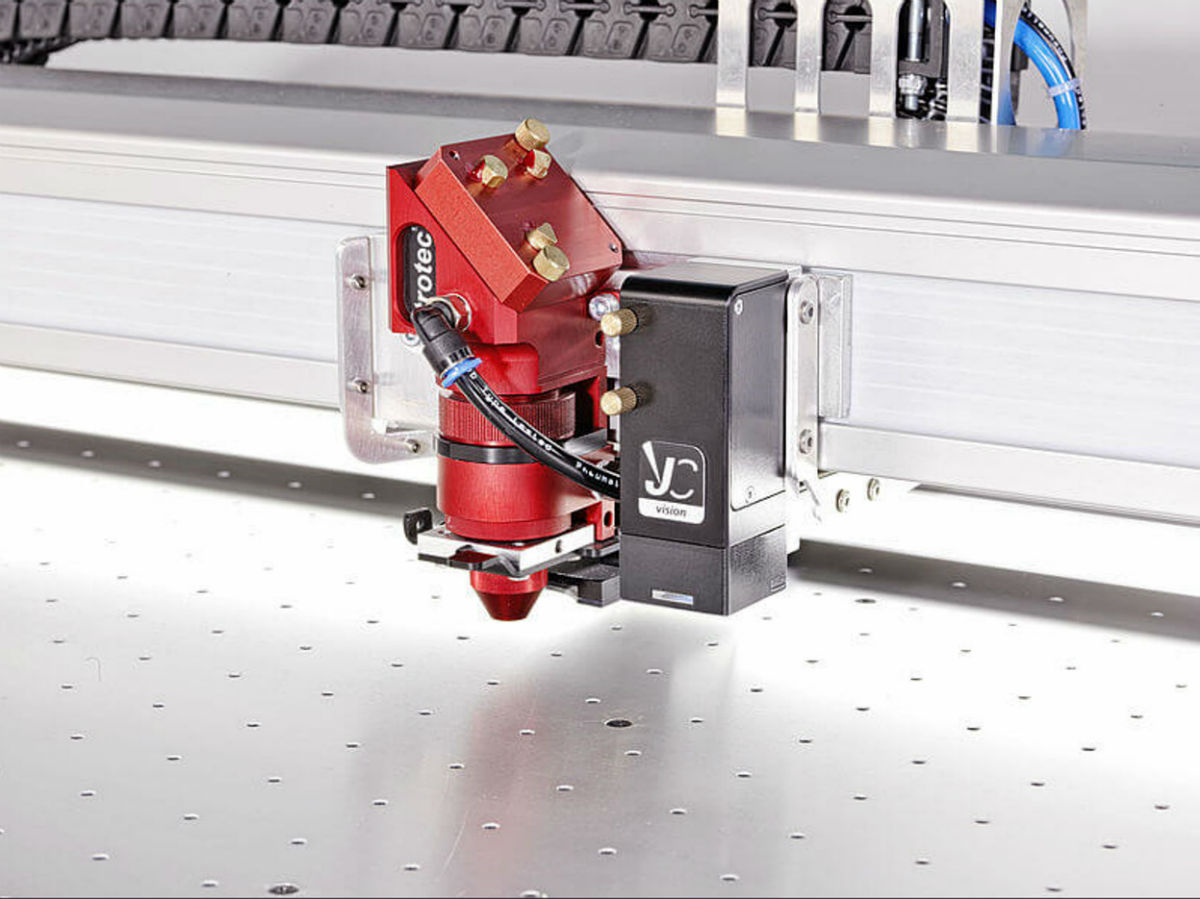
Galvo laser systems, typically used in high-volume and industrial applications, can do the same things as the flatbed, but the motion system is fixed and the laser beam is delivered by two mirrors onto a smaller working area. Once either system is in place, there may be a need for upgrades and additional accessories.
“Laser system upgrades are specific to each laser owner’s individual needs; however, increased power for boosted productivity and accessory add-ons that offer more capability are highly desirable options,” Stevens says.
Laser system upgrades
The main reasons customers give for wanting the upgrades or add-ons are to increase speed and to be able to engrave or cut thicker materials, according to Kern. “A larger laser would allow you to process thicker material or cut at a faster feed rate,” Kern says.
An upgrade in wattage can add more power to the laser system so that it can engrave and cut a wider range of materials at faster speeds, according to Stevens.
“Lower wattage laser engraving machines can often struggle to process thick and combustible materials, whereas a higher-powered system can efficiently complete the job without slowing the job down,” Stevens adds. “Working with dense materials, such as wood, rubber and glass, can be more limiting based on the system’s low wattage over its motion system.”
The power for most lasers is measured by wattage, with many entry-level systems starting at the 30-watt mark, explains James Stanaway, director of marketing for Epilog Laser.
“On Epilog systems, 30 watts is enough to cut through up to one-fourth inch of hardwoods and acrylics,” Stanaway says. “If you are cutting through a lot of one-fourth-inch thick wood, then you’ll probably want a higher wattage, 40 or 50 watts, so you can run the system at a reasonable speed and move through more product.”
A 150-watt laser able to cut one-fourth inch of material upgraded to 250 watts or higher will be able to cut one inch of material, Kern says, adding that the type of materials also could be expanded.
More powerful, higher-wattage lasers also can perform faster or deeper engraving, especially with acrylic, wood and other hard materials, according to Rabideau. Additional power, however, would be inefficient for thin engraving or microsurfacing engraving, which does not require a lot of power, making a power upgrade meaningless.
“The right configuration of lasers, optics and accessories will give the best quality results with the material,” Rabideau explains. “Then, adding power will, in many cases, result in higher productivity without sacrificing quality.”
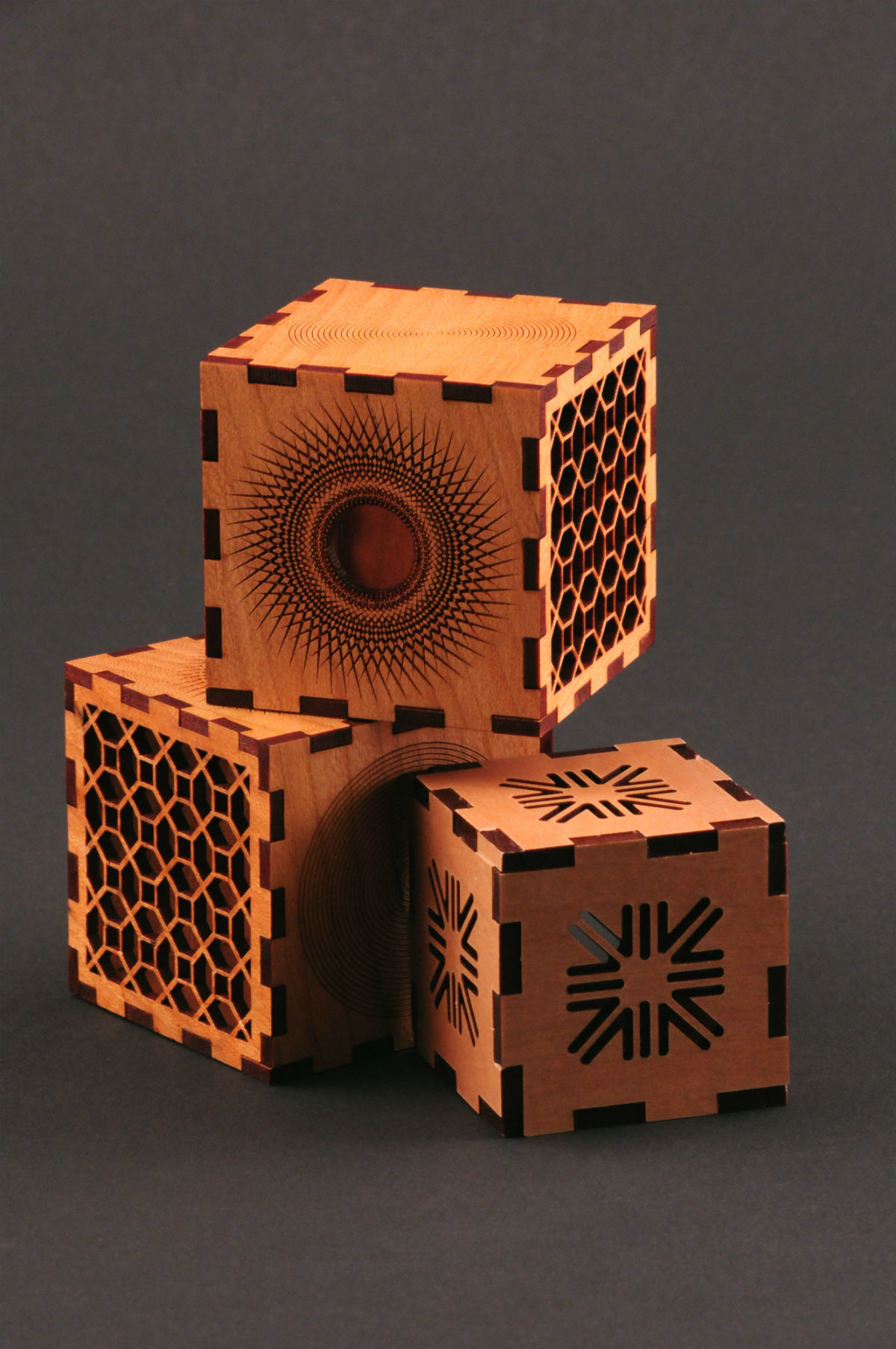
Universal Laser Systems provides laser systems that are designed to be expanded as a business grows or commercial requirements change.
“A number of laser system companies promote upgradable systems, but they don’t provide details on what that really means until you ask,” Rabideau says. “For some, especially laser upgrades, it means sending out a technician or sending the system back to the factory incurring downtime and a lot of expense. For us, in most cases, it means providing a module that the customer can install in seconds or just a few minutes.”
Universal Laser Systems focuses on system configurations, and customers can opt to reconfigure their laser systems to improve processing results, quality and productivity. But higher power for greater speed and capability also comes at a higher price, according to Rabideau.
“What does more power buy you? What can you do with a higher power system? How much more productive can you be?” Rabideau poses. “Sometimes adding power isn’t going to do anything for you.”
Options to attachments
Laser systems can be upgraded in ways that do not require power upgrades, such as the addition of optics. A vision or camera system will improve cutting accuracy through the use of magnets, which are better able to align images to the material being cut. The system can recognize any distortions within the design cutting path and automatically adjust the cutting lines to match that design.
“If, for example, you had preprinted material and wanted to cut it out and align it to a piece of plastic, the camera system automatically aligns it for you, so you can cut out artwork precisely onto the sheet,” Kern says. “You have a nice finished product when you’re done.”
Another upgrade is to vary the camera’s focal lengths, so that shorter lenses have a smaller spot size for height resolution engraving, Stevens says. The longer lenses have a larger spot size that produces better tolerances, allowing for a greater variety of materials and applications to be processed, he says.
A rotary attachment can add a third or Z axis to the X and Y axis points for 360-degree engraving, normally limited to two-dimensional, flat materials. This allows engraving around the surface of cylindrical objects, such as coffee mugs, glasses, bottles and flashlights.
The various upgrades and attachments are dependent on the applications and may be inefficient if the laser is too large for the intended use or material, Kern says. Lasers operate most efficiently from 10-100%, but below 10% will decline in that efficiency, he says.
“If the primary application is a real thin plastic, you don’t need a big laser to do that. If it’s too powerful, it could burn the material,” Kern says.
A paper application also doesn’t require more power if the fastest speed already is employed, Kern says.
“You’re limited by the speed rather than the power of the laser. An upgrade wouldn’t give you more speed,” Kern says.
Environment upgrades
If systems are upgraded, two good investments in the work environment include a larger chiller to allow for more water flow to cool the laser engraver and a power upgrade with more amps and a larger circuit, Kern says. For instance, an upgrade from 150 watts and a 2′ X 3′ chiller to 400 watts would require a 4′ x 4′ chiller. The needed power would subsequently increase from 150 watts at 70 amps to 400 watts at 100 amps.
“Make sure your building has enough electrical capacity,” Kern advises. “Talk to an electrician for additional changes and bringing in any power.”
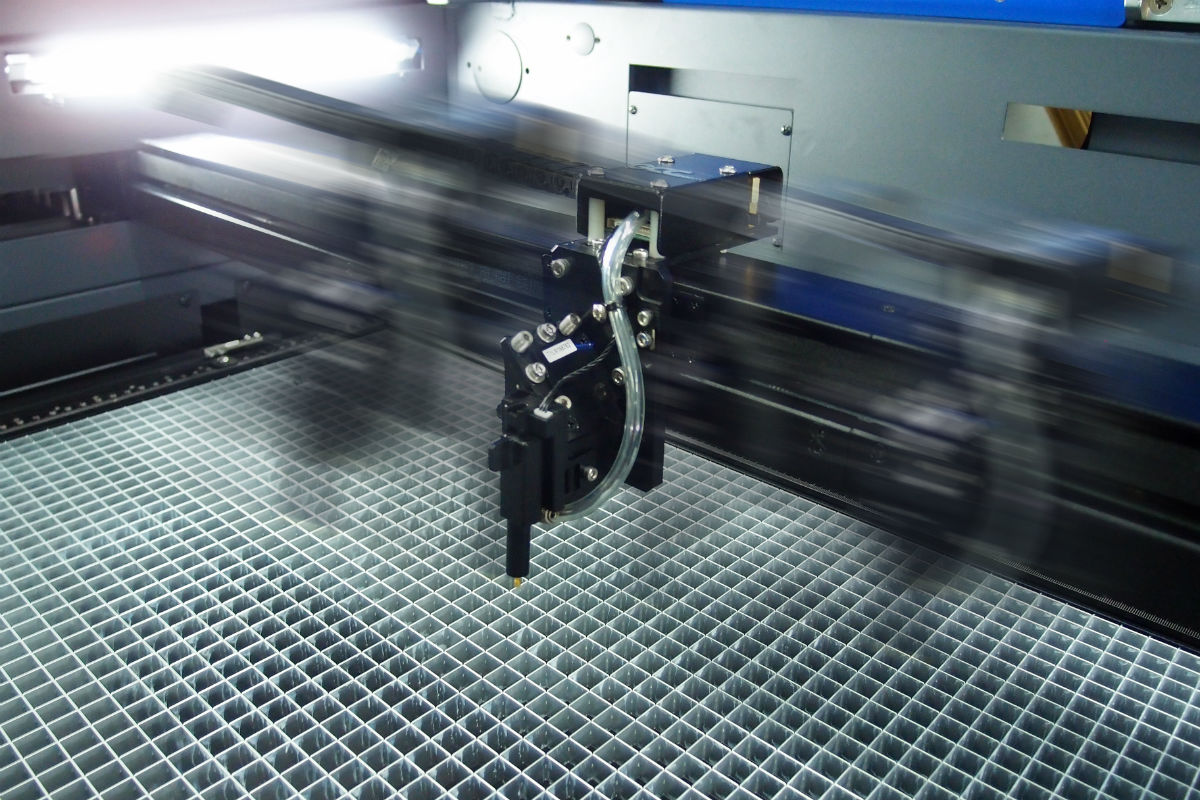
A 100-watt machine can be expanded to 150 or 200 watts without making any changes other than upgrading the laser, Kern says. An upgrade of 200 watts or more will require the upgrade of both the chillers and higher electrical power to operate the machine with commiserate electrical wiring upgrades.
“More laser power can mean faster material processing with more material removed in the same amount of time, so having adequate exhaust or filtration and adequate room ventilation is another consideration,” Rabideau says.
Larger systems able to accommodate larger production runs also can produce more smoke and debris.
“It’s important to consider if your current exhaust ventilation setup, whether you are set up to vent outside or use a portable filtration unit, can handle the increased smoke and debris that may come with an increased workload,” Stanaway says.
The use of a cutting table is another addition to help keep the system and materials cleaner and minimize the burning and melting of materials by reducing the reflection of the beam from the table.
“If you want to enter the world of metal cutting, be prepared to spend a lot more money and consider much more power,” Rabideau says.
The decision on the various upgrades is specific to the laser owner’s needs, but too much power may not give the desired outcomes.
“Having too much laser power is a very real possibility and can result in reduced control for the laser operator. Attempting to process sensitive materials in an overpowered laser engraver can also make locating the proper power settings extremely difficult and, in some cases, some materials might not be compatible at all,” Stevens says.
Another consideration is the fact that the laser source is the most expensive component of the system.
“Upgrades should only be done when you are making a large increase in power. Upgrading by 10 watts would not be normally suggested,” Stanaway says. “Another thing to think about is if you have enough business that you want to be able to run more product through your machine, maybe the addition of a second laser makes more sense than just a power upgrade. Then you can be running multiple jobs at the same time to increase your throughput.”