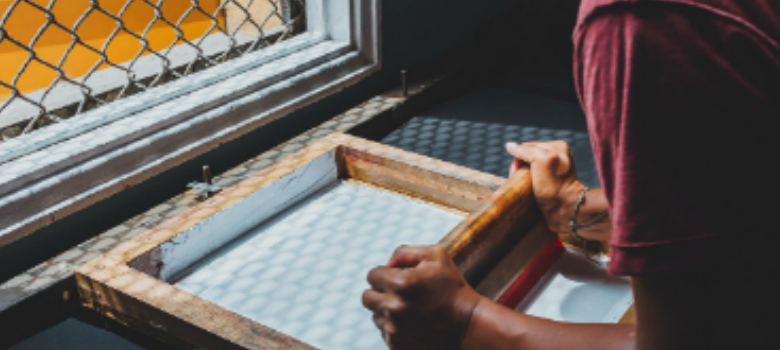
Once upon a time…
Some people viewed it as an art that could not be taught. To others, it was a mystery that only a special few with “the eye” could solve. For the rest, it was hours of toil and perhaps a bit of luck to get a multi-colored job properly aligned on-press.
As the years have passed, registration systems have been developed and refined. They are an essential tool in many screen-printing shops. There are documented do-it-yourself options that work fine and save time and money (headaches too), and there are some systems exclusive to certain manufacturers’ presses that cost thousands of dollars. These systems tout greater accuracy and speed, but regardless of which system you choose, it’s important to use it regularly and properly.
A registration or grid system has many pieces and steps that need to be in harmony to deliver the goods. It helps ensure efficient use of time and maximize your production. It involves pre-press in the art room, proper placement of the film on the screen to be exposed, and the alignment of the screens on press with necessary fine-tuning via micro-adjustments. While commercially available registration systems may have some differences, they all take into consideration these fundamental steps.
You first must work with the separated artwork and its placement using registration marks, or a simple plus (+) sign on each piece of film or vellum. Make the marks large enough so they’re visible after you shoot your screens.
Let’s begin with a simple way to register screens for a multi-color print that won’t cost you thousands of dollars. Before exposure, center your film with appropriate registration marks on the screen or exposure unit, with the top of the image area about 6″ down on the screen. You can use a T-square for this purpose, but eventually, you’ll devise a grid or template to maintain accuracy and speed things up. You’ll need to double check yourself as you progress through the steps, especially at the beginning, but here’s a brief overview:
- Center and place your main film positive on the platen and tape it. No tape should come in contact with your image area. When centering, some people draw a line down the middle, others will develop a template.
- Place your screen so it is aligned with the film on the platen and partially secure it with the clamping system you have.
- Line up your screens accordingly in each print head of your press with the registration marks on each of the separated layers.
- Fully secure your registered screens with your screen clamps.
- Double check yourself to ensure all screens are properly aligned. Adjust your micros as needed (if available).
- If everything appears okay, remove the film you had attached to the platen. Don’t tape off or put a block out on your registration marks yet.
- Put ink on your screens and do a test print on a pellon, test shirt, or piece of fabric. Adjust as necessary until the image is accurately registered.
- Block out the registration marks and begin production.
There are other DIY systems, so do your due diligence and find one what works for you. What if you want a manufacturer’s registration system that’s all ready to go and comes with easy-to-follow steps? Most screen-printing companies have developed their own such systems, but be careful. Some are designed exclusively for use with specific presses. They do cost some money, but the promised payback comes quickly as you print more multicolored jobs. One other note: different sized screens often require different systems.
With the advent of direct-to-screen (DTS) and computer-to-screen (CTS) technology, systems are available that eliminate the need for film, expose lightning fast, and prevent exposure issues such as undercutting. Once again, do your homework and invest in what suits you best-and print happily ever after.