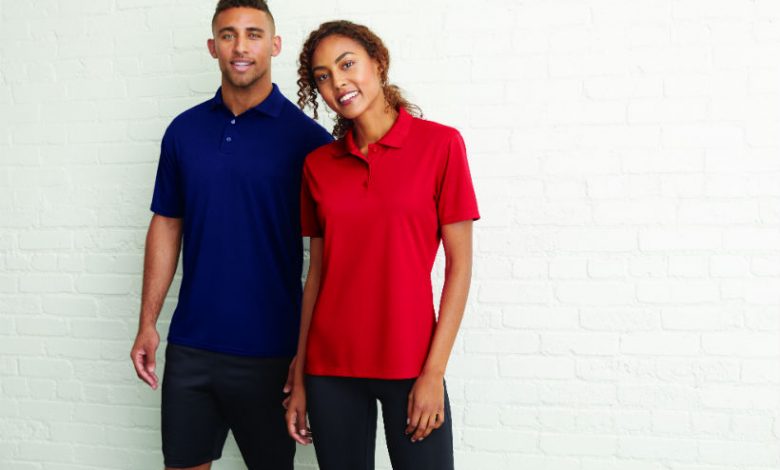
Decorating 101 tells us that not all fabrics should be treated equally. The way you print determines how your print will look and each fabric has different qualities that make screen printing a new adventure. Whether it’s through years of experience or learning the hard way, the printing process becomes second nature. Here are some tips, tricks, and reminders for decorating on some of the most common fabrics.
Cotton
Cotton has been used throughout the history of screen printing. It’s important to know this substrate to be prepared for production, planning, and printing. Cotton tends to be a pretty quick print, which is a bonus, but the key to screen printing on cotton is to keep inks on the surface of the garment. You want a thin layer of ink to sit on top without soaking into the fabric. This is the best practice for most fabrics.
Polyester
Polyester is a great fabric for performance wear products and a popular material for team gear and active customers. There are challenges to printing on polyester you’ll want to consider.
With any synthetic garment, you’re going to deal with some troubles. A good decorator is prepared for the type of substrates they will come across. The number one issue with polyester is dye-migration.
Tips for printing on polyester:
- Test all your substrates: If your fabric is in-house and you know you have time to produce them-test print on some fabric and leave it over the weekend. Tests help decide if the inks you use produce the best result and if your process will work. If they don’t, you’ll be able to make changes to stop migration or improve the overall quality of the print.
- Decrease the heat: One problem that decorators run into is that they like to increase the heat and run their belts faster, but that’s actually a big mistake. It is faster for production, but the ink will migrate worse. The key is to keep the temperature close to your cure temperature and your dryer belt slower. The thicker the print, the longer the cure time.
Fleece
Like with polyester fabrics, dye migration is something to watch out for with fleece fabrics, since fleece often contains a polyester substrate. The cheaper the product, the more issues you’re going to have. One of which is shrinking. To prevent shrinking you can also try two things:
- Run your fleece through the dryer first to help with shrinking. This also helps with migration.
- Pre-flash your fabrics to help the fabric relax or shrink before you put the ink down.
Tri-blends
A lot of decorators want to treat tri-blends the same as any other substrate, but it is important to consider how they are different.
Since tri-blends contain rayon or spandex, the substrate tends to stretch more easily. You may want to put additives in your ink to get the ink to stretch, as well as prevent cracking.
When using adhesives on tri-blends, you may not be able to get the garment off the platen if you have too much adhesive on your platens. With that said, it’s better to print wet-on-wet.
Three tips for tri-blends:
- Graphics: You don’t want to print with six different colors on a tri-blend. It just won’t be successful because you’ll have to flash a lot to achieve a certain color. Try to reduce the number of colors if you can.
- Open up your graphics: Utilize the substrate color in your graphic. This helps create a better hand and drape, uses less ink, and decreases flashes.
- Work with your artists: Artists need to understand substrates as much as decorators do. Teach the artists how artwork changes based on the fabrics.
Final tips
Fibrillation is something to watch for when screen printing. Fibrillation occurs when the fabric fibers lift off the surface of the print, causing it to look slightly fuzzy. Attempt to prevent this by flooding lightly. Avoid agitating the ink too much in the flood process.
The higher the shirt quality, the smoother the surface of the fabric will be, and the less this will be an issue. You want it to be like paper. You can also troubleshoot fibrillation with presses, squeegees, or rollers.
High-quality garments have a tighter stitch density due to the fact that they’re spun tighter than other cotton substrates. The smoother the fabric, the less trouble fibrillation will cause you.
Scorching is another issue that occurs, in particular with heather garments. If you flash too close to the material or you flash too often, you can pretty much scorch anything. With any substrate, you want to control your flashes and your temperature. Be sure to experiment to get the best outcome.
These tips are by no means comprehensive. However, consider these suggestions when printing on different fabrics and research techniques and tips for getting the best result when printing on any type of fabric.