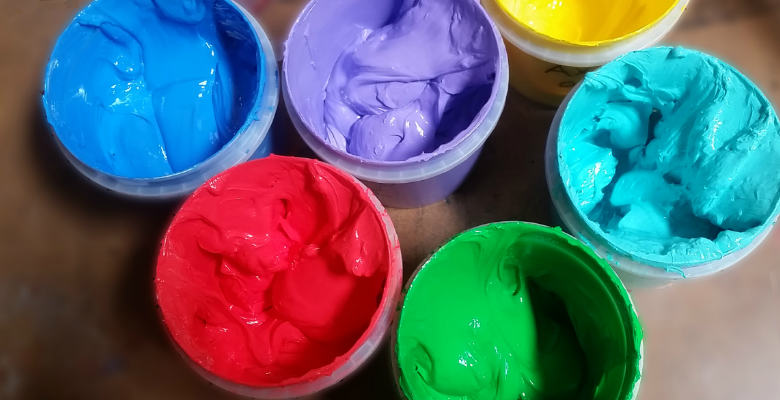
Three scenarios come to mind when thinking about when to use low-cure inks. Here’s a breakdown of each:
SENSITIVE FABRIC OR SUBSTRATE
If the fabric to be printed on is sensitive to heat (e.g., it will melt or shrink when exposed to high temperatures) then a low-cure ink might be the answer. There are few options other than either using an air cure type of ink, such as a solvent-based or water-based ink, or a two-part system (i.e., Epoxy). In using either of these options, there is the negative of having to wait for the ink to dry. This can take anywhere from a few minutes to days. When running a business where every minute lost means money lost, waiting for the ink to dry is not an option.
By using a low-cure plastisol with a cure temperature of around 275 degrees F (135 degrees C), the fabric might stand up to the heat. There is no excessive waiting time for curing, and the job is saved.
One of the most popular types of sensitive substrates is the non-woven polypropylene bag everyone is familiar with at the grocery store. They are offered as cheap shopping bag alternatives or used as promotional giveaways. If these bags are cured at 320 degrees F (135 degrees C), they will probably end up with what I call a “potato chip” AKA a molten clump.
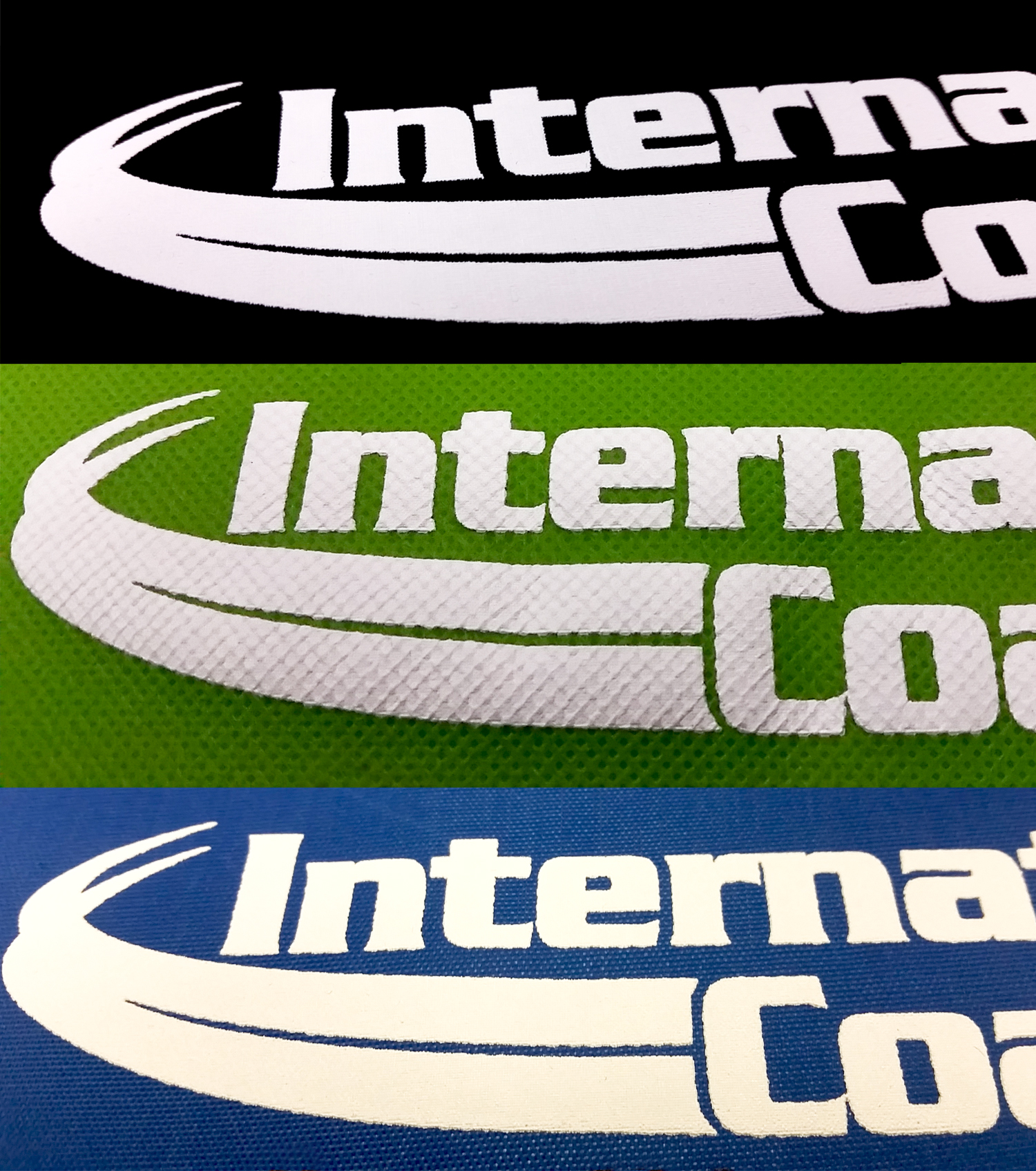
PREVENT BLEEDING
Many garments that contain polyester will bleed or dye-migrate when exposed to the standard 320 degrees F (135°C). Many things cause dye migration:
- Cheap dye
- Not correctly rinsing out the dye during the dye process (This makes colors stronger/brighter)
- The garment has been previously decorated using a dye sublimation process, where heat-reactive dyes react at temperatures below the 320 degrees F (135 degrees C) level.
No matter the cause, lowering the cure temperature of plastisol to 275 degrees F (135 degrees C) may help prevent the bleeding. I’ve been around far too long in this industry to say we’ve solved every dye migration problem we’ll ever encounter. However, using a low-cure ink will mitigate most dye migration problems, especially when paired with a great bleed blocking underbase ink for tougher cases.
SAVE MONEY
Just as setting the thermostat in your office or home to a lower setting in the winter will save money, the same goes for your dryer temperature with low-cure inks. The dryer uses less gas or power, which translates to lower energy bills.
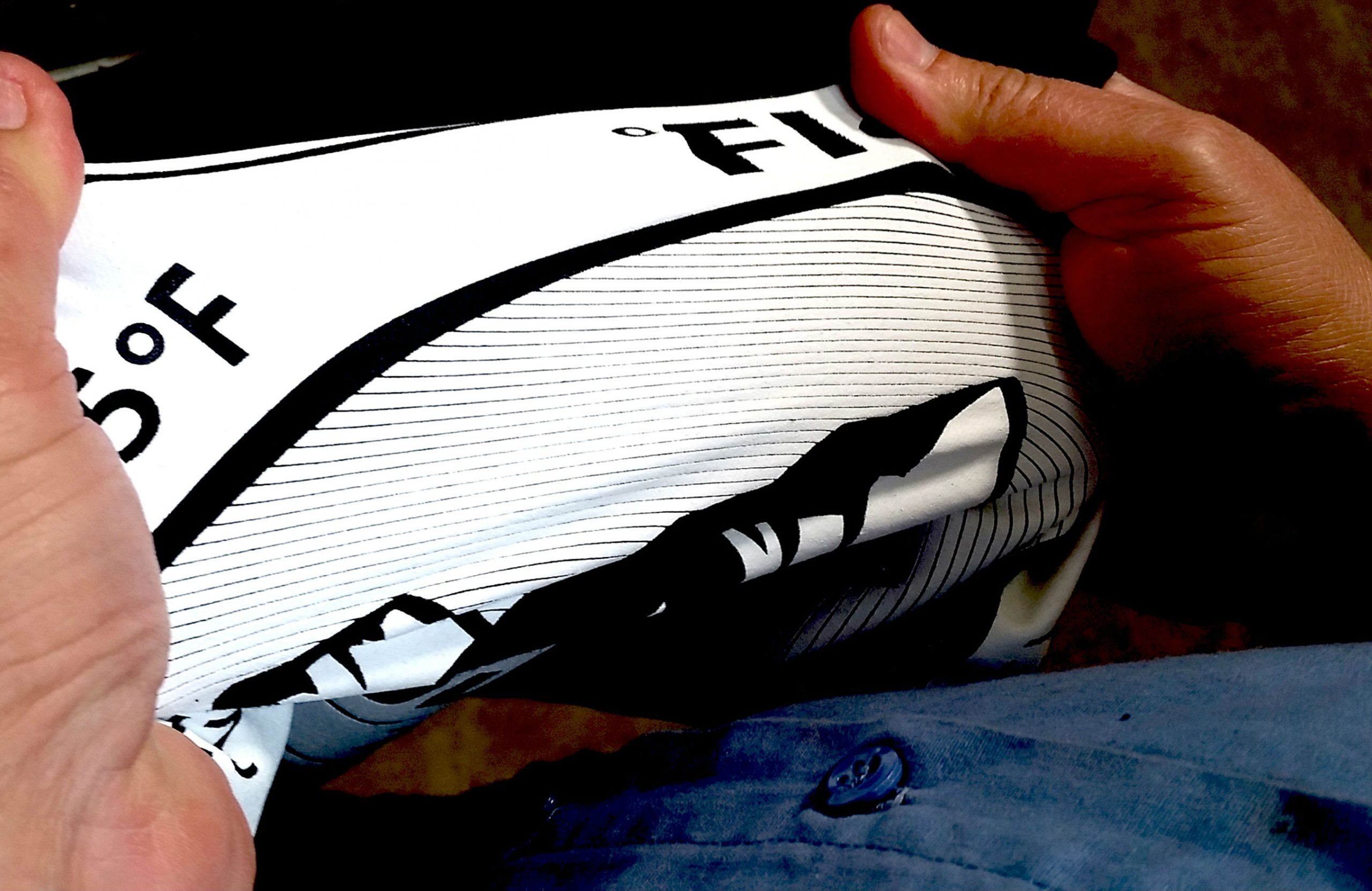
A word of caution when choosing low-cure inks: Be sure to pick a low-cure ink that works. Test print the ink. Be sure it does not crack when stretched, exude an oily substance, or come off in the wash. A low-cure ink that requires a longer than usual curing time can also translate to no savings at all because it will take more time to cure the entire production run.