How has the screen reclaiming process changed over the years?
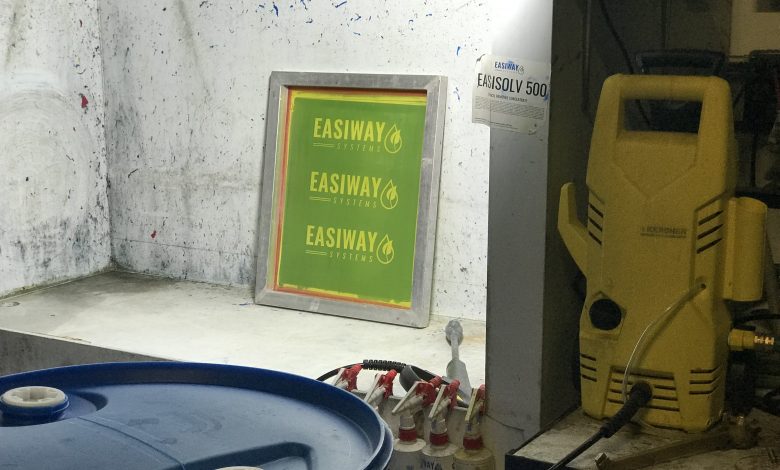
When I walk into a shop for the first time, owners direct me to the new gleaming press or the big, new automatic die cutter. I like looking at equipment, but where the rubber meets the road is the screen/reclaim area. Usually, the screen room has ventured into the 21st century with a newer point of light source and vacuum frame, or more recent updates, such as a direct-to-screen or an automatic coater.
If I could interject some personal history here, it will make the rest of this article pretty relevant. The date is etched in my mind: Monday, July 8, 1968. That was the first day I reclaimed a “silkscreen.” Yikes, I’m old, and I am still reclaiming screens. The point here is that in 52 years of being involved in some segment of screen printing, the screen reclaiming process has stayed the same. Yeah, there are now reclaiming machines and dip tanks and better pressure washers, but the process of removing ink, removing emulsion, removing the stain, and degreasing hasn’t changed that much. The significant changes are in inks, emulsions, mesh, and the knowledge base to bring the entire screen-printing process into the century.
The shops that are still using a traditional four-step method of reclaim, for the most part, are small specialty graphics, textile, and printed circuit board shops that are not big enough to justify the cost of an automated reclaim machine.
With the introduction of newer, hybrid reclaiming products now in the marketplace, most of these shops have eliminated one, if not two steps by moving up the food chain to more modern products that can do more than one process step at the same time. For example, an emulsion remover that has a built-in degreaser, or a screen wash that can remove ink, stains, and degrease in one step.