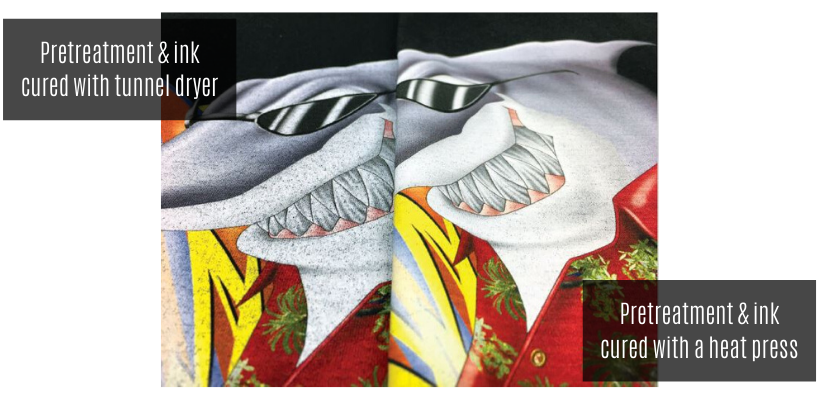
Direct-to-garment (DTG) prints provide an unlimited number of colors and the ability to print designs that would otherwise be very prohibitive with other printing methods.
For all of its differences from screen printing and other disciplines, it still requires drying and curing of inks and pretreatments. Most DTG shops use a heat press to fulfill this need. However, we’re often asked, “Can I tunnel-dry the pretreatment? What about tunnel-drying the inks?”
The answer to these questions is yes. You can cure pretreatment and inks with a tunnel dryer. But, what happens to the actual prints when you deviate from the standard heat press? How do they look and feel? Are there any other consequences to consider?
To help show what happens with these different processes, we printed the same design with varying techniques, and the results were interesting. We utilized the same printer, inks, and pretreatment on a high-quality, ring-spun shirt, but changed up the curing of the pretreatment and inks.
Conveyor dryer
Pros
Pretreatment machines are typically able to pretreat a shirt faster than the curing process takes. Utilizing a conveyor dryer, provided it is sufficient in size and capacity, will allow a single operator of the pretreatment machine to process shirts at a higher capacity rate than using a single heat press. Another bonus is there are no compression marks from the heat press on the shirt.
Cons
The finished print surface is much rougher than if it had been pressed dry. One option is to use the conveyor dryer to get most of the pretreatment dried and finish off with a quick press, but this defeats the purpose of trying to eliminate the heat press in the first place.
Additionally, it needs more space, typically requires more electricity or a gas hookup, and conveyor dryers can cost more than a 16″ X 20″ heat press.
Using a conveyor dryer to cure the pretreatment will cause shirt fibers to rise, which ultimately gives the shirt a rough feeling.
When you utilize a heat press to cure the pretreatment, you crush the fibers under pressure while at the same time cure the pretreatment. This cured pretreatment helps hold the fibers down for a better printing surface for the inks. Thus, in all our test prints where the pretreatment was tunnel-cured and not heat pressed, the shirts had a rougher printing surface for the inks.
The main difference when tunnel curing the inks is that it takes longer. Though this varies depending on the dryer (electric or gas) and the size of the dryer, the cure time is longer than using a heat press. However, the time it takes is somewhat of a non-issue because as long as your dryer of choice can keep up with the printer, you are just laying shirts on a conveyor belt. They pop out cured on the other end, but with a bit more of a “feel” to it. The colors were also slightly brighter, as we were not pushing the inks into the white and shirt.
Heat press
Pros
Using a heat press results in a much faster drying time of the pretreatment and smoother finished printing surface for the inks. A smaller footprint is needed to complete the process, and it can easily fit into a small room or office.
Cons
Using a heat press for curing can tie up a press needed for other applications. It can also leave a visible pretreatment box, depending on the shirt, shirt dye, and pretreatment used, as well as how the operator presses the shirt.
Additionally, depending on the size of your print and the speed of your printer, you might find that the heat press restricts your hourly production. You may even find that more than a single heat press is required to keep up with your printer. The resulting prints, though, had a very smooth hand on the higher-quality shirts.
The colors were also slightly lighter and less vibrant than the tunnel-dried version, although most end customers would not notice a difference. This was partly due to a weaker white underbase in conjunction with the heat press, mushing the inks into the shirt.
So, dryer or heat press?
Space and monetary constraints limit many shops. The least expensive and most common procedure is to dry the pretreatment and inks with a heat press. Presses take up less space compared to a conveyor dryer and typically cost less. Plus, most heat presses can run off a standard electrical outlet. If you are working out of a small office or bedroom, then the heat press is the most logical way to go.
Other shops with more space should consider a conveyor dryer for curing pretreatment and inks. If daily shirt volumes are high and financial and space resources are not an issue, a serious look at a conveyor dryer for curing the ink should be considered. Due to increased throughput and productivity, a good conveyor dryer for curing ink can make sense for some DTG shops that are running their printers in a volume/production setting.