6 Screen Printing Tips for Beginners
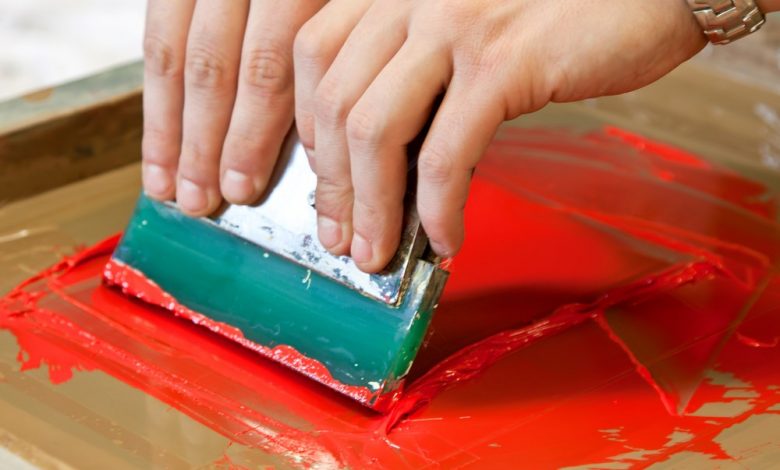
Screen printing is a relatively simple process. When you’re first getting started, though, it can seem more than a bit overwhelming. You have to purchase supplies and materials, master techniques, and, of course, there are a lot of mistakes to be made along the way.
Whether you are taking up screen printing as a hobby or thinking about starting a business, there are some things you can do to make the process easier and ensure your success. Keep reading to discover a few successful screen-printing tips for beginners.
Start with High-Quality Shirts
To save money, a lot of new screen printers try starting off using the cheapest shirts possible. While this may save you a few bucks up front, it’s likely to end up costing you, both in terms of money and time. Cheap, low-quality shirts may not absorb the ink well. They may also have inconsistencies that make them difficult to print on or contain fibers that don’t work well for the screen-printing process.
If you want to ensure your success from the get-go, use high-quality shirts. Bulk T-shirts and blank hoodies from leading brands are much more affordable than you may think, and they provide the quality you need to ensure finished products that meet your expectations. You may even find that your budget will go further than you think when you choose to buy bulk blanks from trusted wholesalers rather than trying to find the cheapest retail shirts on the market.
Watch Video Tutorials
There are a lot of written tutorials, books, etc., out there that will teach you how to screen print. If you want to get a solid feel for the process before you dive in, watching video tutorials is the way to go. There is only so much information that can be conveyed in writing. When you watch a video tutorial, you can see exactly how everything is done rather than just reading about it and trying to imagine it.
Watching video tutorials is a great way to pick up new techniques, too. Even if you already have a bit of experience with screen printing, a good tutorial can show you how to perfect your process and achieve better-quality results. YouTube is loaded with videos about screen printing. Spend some time checking them out, and you’ll likely have much greater success once you begin working on your projects.
Use High-Quality Graphics
If you use low-quality graphics, you’re going to get low-quality results. Unfortunately, there is no way around that. When you want to make screen-printed shirts featuring crisp designs and smooth text, you need to start with high-quality graphics.
High-resolution images are a must. Low-resolution ones will appear blurry on your substrate regardless of how good you are at printing. When using multiple colors, you also need to ensure that they are appropriately separated to ensure that your product has proper registration.
Choose the Right Screens
If you think you can get away with using the same type of screen for every project, think again. The screens used in screen printing come in varying mesh counts, and choosing one with the appropriate count is a vital step in ensuring a high-quality finished product. Newbie printers are often sold just one type of screen, but more accomplished printers know that they need to have a wide variety in their inventory.
Screens range from standard mesh count of 110 and under to 400 and up. Screens with lower mesh counts tend to work well for most simple jobs. If you are working on detailed or photorealistic prints, or you are trying to create halftones and gradients, you need to use finer screens. Once you’re familiar with how to choose the right mesh count, you’ll be well on your way to creating higher-quality finished products.
Be sure to check the tension on your screens regularly, too. Over time, screens can become loose, which can hurt print quality. Depending on what type of screen you are using, you may be able to adjust the tension, or you may need to replace it.
Check Your Equipment Regularly
When you start printing manually or using automatic equipment, regularly checking it could save you a lot of frustration. If you are using a press, the screws holding it together could become loose and allow screens and platens to move during the process, resulting in blurred prints.
Make sure your screens are clean. Leftover ink from your last run can quickly ruin your current one. Look everything over to make sure there isn’t damage before using it. Checking everything out before you get started adds a few minutes to the overall process. Failing to do so and ruining an entire batch wastes a lot more time. And, of course, ruined batches are a waste of money.
When you finish a batch, clean your screens and other equipment immediately. Taking good care of your supplies ensures that they will get the most life possible and will be ready to go when you’re ready to start another batch.
Always Do a Test Print
Even if it’s a project you’ve done before or one that seems too simple to mess up, always do a test print. Doing a test run ensure everything is set up correctly and that your finished product will be flawless. Trust us–it’s more affordable to do a test print and make small adjustments as needed than to ruin an entire run because something wasn’t right.
If you’re new to screen printing, the process can seem complicated and a bit overwhelming. If you keep the tips above in mind, though, you can significantly improve your likelihood of successfully printing your designs. Remember, though, that the only way to perfect your technique is through practice.