5 Tips for Winter Heat Printing
Every year when the cold weather sets in, it brings along some heat printing challenges with it
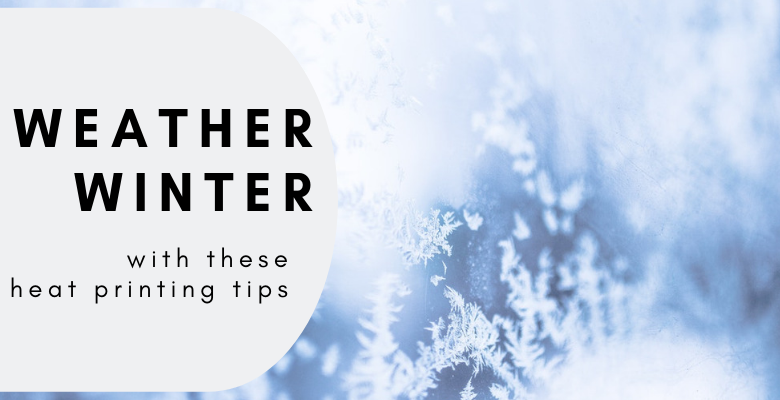
Every year when the cold weather sets in, it brings along some heat printing challenges with it.
Some shops that utilize empty basement spaces or garages can be exceptionally cold and present extra challenges. The first thing is to make sure your shop or area that you are heat printing in is heated and properly insulated. This can help reduce some of the challenges. When you are not constantly fighting a cold room temperature, your heat press can print.
After your work environment is somewhat warm, the problems related to the cold winter weather can be overcome by following these tips.
1. Preheat the lower platen for best results
When the heat press has been sitting in a cold environment overnight, the lower platen will be quite cold. This is true to the point that it causes heat loss on the first few transfers applied at the start of the next day.
Therefore, you will want to preheat the lower platen before you begin to press your apparel. After the heat press has reached the preset temperature, lock down the heating element for a full minute (without a garment) to warm up the lower pad, eliminating application failures caused by a cold lower platen.
This procedure will only need to be done at the start of the production day or after long breaks between pressing.
2. Remove any extra barriers
Some decorators use a pad protector on the lower platen or a cover on the top platen. Although these pad protectors are great for reducing wear on the pad, and for quick garment placement, they also act as an insulator that can keep the lower pad from retaining heat during a production run.
If you are having application problems with certain types of transfers, try removing the pad protectors.
3. Try a cover sheet for static
Heated production areas in the winter will dry out the air creating static electricity. This static can cause the transfer paper to stick to the upper heat platen when the press is opened. Transfer paper that is suddenly yanked from the print can cause misprints. This is especially true with cold peel transfers that have not had a chance to properly cool.
To eliminate this static cling problem, try using a cover sheet. A cover sheet will help reduce the chance of the transfer paper pulling up when opening the heat press.
Cover sheets can also reduce the amount of heat passing through to the transfer. If you are having application issues with a cover sheet, you may need to increase your temperature an extra 10-15 degrees F to accommodate for the lost heat reaching the transfer.
4. Prepress apparel
Always prepress your garment before heat printing to remove excess moisture trapped in the garment. This procedure needs to be done all year long but can be more of a problem during the winter months in some regions.
Just like preheating the lower platen, by prepressing, you are also heating the cold apparel to prep it for a warmer application.
Note: Failing to prepress apparel before applying a transfer can result in cracking or bubbling due to trapped moisture in the garment. It may not be apparent until the customer washes the garment.
5. Perform proper maintenance of your heat press
When the temperature is colder, the effects of an inaccurate heat press can be amplified. You want to make sure your heat press is functioning correctly and accurately.
For checking the accuracy of your heat press, you can utilize a heat press test kit. Make sure your temperature is what it says it is, along with your pressure. Check various places around your heat press platen for accuracy, typically in the center and the four corners.
Along with maintaining your equipment for accuracy, you will also want to make sure you have a quality heat press that can withstand a long run of T-shirts without dropping in temperature throughout the printing run.
If your heat press cannot stay up to temperature, you could run into application issues. If you are using a poor quality press, it may be time for a new press.