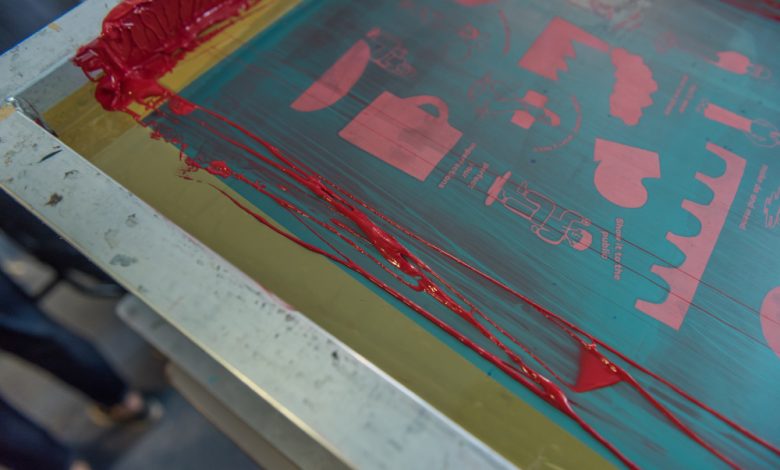
Several screen printing facilities have struggled with mesh staining in one way or another. Staining generally occurs in two different forms:
-
- Staining from the emulsion on the screen
- Staining from the type of ink used in the screen printing process
First, let’s look at the staining of the mesh from the emulsion on the screen. The leading cause of emulsion staining is due to the underexposure of the screen. When you have emulsion that is not 100% exposed, you allow chemicals like a hot solvent (lacquer thinner, xylol, and screen opener) to crosslink with the emulsion during the printing process. If you let the emulsion to crosslink with a solvent, you create a light deposit of emulsion that will be difficult to remove in the reclaiming process. If the light emulsion stain is repeated on a screen, you will likely have to resort to using a ghost and haze remover to remover the staining. As we all know, ghost and haze removers are damaging to screen mesh and shorten the life of a screen.
A couple of general procedures for finding the perfect exposure for a screen are as follows:
- Perform an exposure test for each mesh count/thread diameter to dial-in the best exposure time for a favorable outcome.
- Try matching your artwork (halftones, line count) to the proper mesh count, open print area, and thread diameter. Each one of the previous variables will deposit a slightly different ink film.
The second form of staining we commonly run into is the type of ink used in the screen printing process. There are primarily plastisol ink, nylon ink, and water-based inks for the textile market and solvent, epoxy, enamel, ultraviolet inks for the graphics market. Ink choice sometimes can be an option driven by the substrate you’re printing on like cotton or polyester garments, flat sheet polyester substrates, polycarbonates, vinyl, untreated polyesters, etc.
In this case, you need to pay close attention to the products you are applying to your screens as a press wash. Hot solvents have a fast flashpoint and can quickly lock in an ink stain in the open mesh printing area. In the case of a graphic ink removing a stain set-in with a hot solvent can be extremely difficult. Be sure to use an on-press solvent that’s formulated for the screen printing industry.
Here are two helpful tips you can implement to help reduce ink staining during your screen printing process:
- Use a press wash to clean the image area when your screen is sitting idle for a period of time (during 15-minute breaks, lunch hour, etc.)
- When your job is complete, be sure to clean out the image area with a press wash, so the remaining ink does not begin to set an ink stain before the reclaiming process. If your screen is not going to be saved for a repeat order and cataloged for future use, another suggestion is to clean the image area with a screen wash.