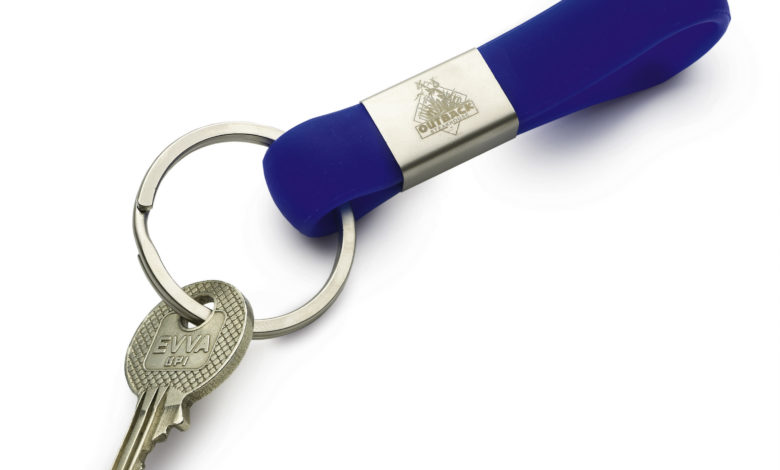
The laser marking process refers to the technique of marking or labeling materials and workpieces using a laser machine. The removing method of marking, as the name implies, involves removing the top layer of the material by laser processing, whereas engraving involves changing and making depressions in the surface of the material.
Both CO2 and fiber laser marking machines are leaders within the industry, offering unparalleled processing speeds. CO2 lasers are gas composed systems containing a mixture of carbon dioxide that is stimulated electrically. They are best suited for processing non-metallic materials and most plastics and are the most widely used laser type because of their relatively high efficiency and superior beam quality. Fiber laser sources are solid-state machines that generate a beam using the “seed” laser and amplify it in specially designed glass fibers supplied with energy through pump diodes. Fiber systems produce an extremely small focal diameter that results in intensity up to 100 times higher than a CO2 system, but by emitting similar power. Fiber lasers are ideal for metal marking applications and feature a long service life with a minimum of 25,000 laser hours.
Laser marking technology is ideal for producing consistent results and is a permanent process that is resilient to acids, abrasion, and heat. Differing applications may require different techniques, but engraving, staining, removing, annealing, and foaming are the most common marking methods. Each laser marking procedure will have its own unique advantages and disadvantages, depending on the materials used and the quality requirement. While it is possible to mark various materials with a laser, the two most common materials that are laser marked are metals and plastics.
Metal marking
When it comes to engraving and marking on metals, lasers are an effective and efficient tool. The laser marking of metals is typically done by a fiber laser and requires no pre- or post-processing. Metals of all types, hard or soft, can be marked accurately, legibly, and quickly with a laser. Commonly used metals include stainless steel, anodized and non-anodized aluminum, alloyed steels, precious metals, coated metals, and many more.
Laser marking of metals is typically utilized for product traceability features such as serial numbers, data matrix codes, and logos. This method is commonly used in the electronics industry and for mechanical engineering and tool manufacturing. Laser marking can also be useful to various other industries and applications, including medical technology, promotional products, sheet metal, jewelry, signage, and automotive parts.
A specific type of metal annealing allows for color marking stainless steel, a process utilized by MOPA laser. This particular technology can mark stainless steel with a variety of reproducible colors, providing users the ability to label their products with color designations. Whether it’s for identification marking using company logos or functional marking using temperature indications, this is a valuable metal processor capability.
Plastic marking
Laser marking plastics can provide a variety of ways to broaden your product line. This method offers fast, non-contact processing, which helps maintain the integrity of the material. Lasers also allow for versatility since they can process a wide variety of different plastics such as polycarbonate, ABS, and polyamide and can produce different effects depending on the type of laser used.
Engraving plastics with a CO2 laser can create different reactions or appearances, not only based on the type of plastic but also the raw materials, such as color pigments and additives like fillers and flame retardants. Fiber lasers can also create different appearances when laser marking plastics, including foaming, carbonizing, and color changing. Since not all plastics will react the same way to laser processing, it’s wise to have your material tested before purchasing.
Because a laser machine requires minimal setup and provides a large degree of flexibility, laser marking plastics is an economical processing method, even in small batch sizes. Graphics, logos, text, codes, serial numbers, and fully dynamic data from ERP systems can be marked quickly and efficiently, even on the smallest components and in areas that are difficult to access. Typical plastic marking applications include electronic components, keyboards, automotive parts, identification tags, packaging, films, sensors, and many other applications.