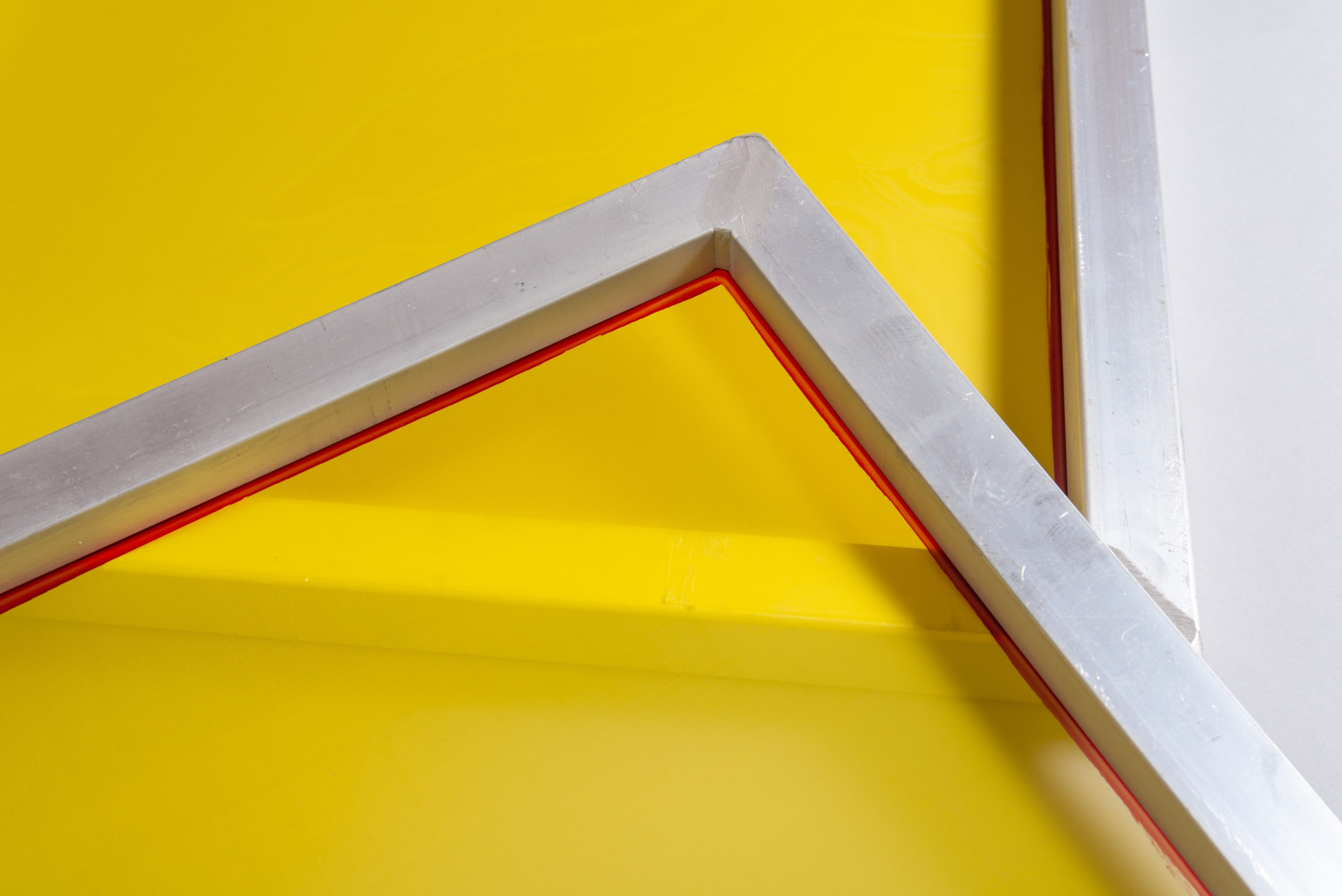
The past 20 months have handed our industry a pronounced change in the way we work. Consider the number of startup screen printers and others who invented or reinvented their livelihoods; the larger screen printing shops that weathered 2020 by streamlining the way they worked. For a large percentage of these groups, an aspect of printing that changed involved bringing screen stretching in-house. Here are some tips and information on the process, including two adhesive options essential to this DIY approach.
Adhesives used in the screen-stretching process
One and two-part adhesive options can be used on both aluminum and wood screen frames. Depending on time, economy, project, and production deadlines, the screen printer benefits from either of these types of frames and adhesives.
For example, a one-part adhesive that dries in 15-30 seconds once applied to the screen frame is an optimal choice in a small shop. It’s especially advantageous when only one manual screen stretcher is available or all screen stretching is done by hand.
To stretch or re-stretch rapidly, here are the steps:
- Stretch the mesh to the required tension based on the mesh manufacturer’s guidelines.
- Lay a bead of glue around the frame and spread evenly using a mini plastic squeegee.
- Mist with an aerosol activator held 12″ from the frame.
- Within 15-30 seconds when the screen is dry, release the screen tension, trim excess mesh from the frame, and instantly use the frame.
A two-part adhesive system can offer an effective method with superior bonding of mesh to frame. Here’s how it works:
- A catalyst is mixed in with the adhesive to ensure chemical/solvent resistance.
- The mesh is stretched to the tension required and a bead of adhesive is spread evenly around the frame.
- Bonding of mesh to the frame will be complete in 10-30 minutes dictated by humidity, cold, and heat in the shop.
The two-part system will also offer flexibility if there is excess squeegee pressure near the edge of the frame. When being used for a project, the mesh won’t pop off the surface of the frame. And, haze remover, press wash, or screen wash ink degradant will not affect the adhesive bond.
Cost-effectiveness
According to my co-worker Chris Skarstad, if a shop runs multiple tables of frame stretching/gluing at the same time, it is this type of assembly method that makes a two-part adhesive time-effective and highly efficient. If bought in bulk, it’s also the most cost-effective.
Summary
Remember, every decision you make regarding your business is crucial to your bottom line. The aforementioned tips and information will help you make a confident, informed determination about which adhesives to choose when creating your in-house screen stretching operation.