One of the first questions new buyers of DTG (direct-to-garment) equipment need to ask themselves is, “How should I set prices for my custom printed T-shirts?” For many years (before DTG made its way into the printing world), pricing was based on screen printing, which involves large setup costs, minimum order quantities, and higher charges for additional colors in a graphic. As a result, screen-printed shirts have a high cost for the first dozen or so shirts, with costs decreasing with larger orders of the same design.
When DTG printing came along, it flattened this pricing model. With DTG, you do not need to enforce a minimum order quantity, you can customize and personalize each shirt, and you can produce unlimited colors. Whether you have one color or a thousand colors, your cost is the same.
With a relatively flat cost curve and a simplified printing process, decorators are free to focus their pricing strategy on what works best for them and their customers. So, what should you be keeping top of mind when creating your pricing strategy? Consider these five questions.
No. 1: What style of T-shirt does the customer want?
What T-shirt blank are we using? Sleeve length, fabric thickness, the softness of fabric, hoodie, zipper, etc., are just a few of the options your customers might request. Some may have a specific brand they like, while others might supply their own blank. Some may want the absolute cheapest T-shirt you offer.
Many garment suppliers offer wholesale prices. Keep in mind that this is another opportunity for you to add margin to your pricing. Typically, you can purchase your blank shirts for $2-$5, depending on the factors above.
Find information on choosing the best T for DTG here.
No. 2: What color is the shirt?
The color of the garment is one of the biggest factors to consider in pricing DTG-printed T-shirts.
Light shirts are as easy as it gets. Typical ink costs run between 10-20 cents per print on a white shirt. The printer only does a single pass laying down all the colors (CMYK) onto the shirt. This means very little ink is used, and the actual printing takes no time at all.
Dark shirts are done a little differently than light shirts. Dark shirts require two ink layers; you have a white underbase layer and a CMYK color layer on top. The white underbase is required to help the CMYK colors stand out on the dark garment. This extra layer increases the ink cost of the print. Typical costs run around 75-85 cents per shirt. I should mention that this can vary depending on the size of the print.
For example, a pocket print will cost significantly less than a full front print. You also need to factor in your cost of pretreatment. White ink requires a pretreatment to be applied to get that rich white we expect to see in a DTG print. The average cost for pretreatment is about 50 cents per shirt.
No. 3: How many shirts does your customer want?
It’s typical to offer a small discount if your customer orders more than one shirt. This discount can vary depending on where you are located regionally or in an area with heavy competition. The price per shirt should decrease for someone who orders 50 shirts vs. a single shirt. Although DTG makes customization simple, you should also increase the price if each shirt has some level of customization to cover the cost of the artwork preparation.
No. 4: How much artwork prep is required?
Some customers may come to you with ready-to-print graphics that do not require any adjustments before loading into your RIP software. However, many will bring you graphics that need some help. It could be something as simple as making the image transparent or having the whole graphic redone. Factor in the extra time and cost into the price. Set yourself an hourly rate and charge accordingly.
Also, do not get overwhelmed thinking you have to do this yourself. There are tons of graphic designers out there that can get the image exactly the way you want at an affordable price. I personally have used IgnitionDrawing.com, but there are many options available. They will have the graphic back to you in 24 hours or less, and it will only cost about $15.00 for two hours.
I am 100% confident the industry will ultimately solve this problem, but it’s just not there yet. With that said, explore the different blends, pretreats, and techniques out there and see what works for you.
Explore Software: Tools for Production & Design on March 24 for presentations on graphic design and working with difficult artwork.
No. 5 (the bonus question): Would you like fries with your order?
Look for the opportunity to increase your margin or order size. One easy yet extremely profitable idea is to add the option of foil prints. Adding foil to your prints is as simple as inserting a single step in the printing process and about 10 cents of material. However, customers will often pay $5-$10 on top of the price of a standard printed shirt.
Offer printing on sleeves, a pocket, or the front and back of a shirt. Don’t just settle for the basic order and always look for ways to add value for the customer while adding to your margin and bottom line profits.
Where does all of this leave us? Over the years, the team at DTG Connection has worked with thousands of DTG business owners. Although business models and markets vary, below is a pricing guide based on the factors I’ve discussed and what we’ve seen and heard from customers. As always, you may need to adjust some numbers based on your local area and your specific business model. Search locally to see what your competitors are offering.
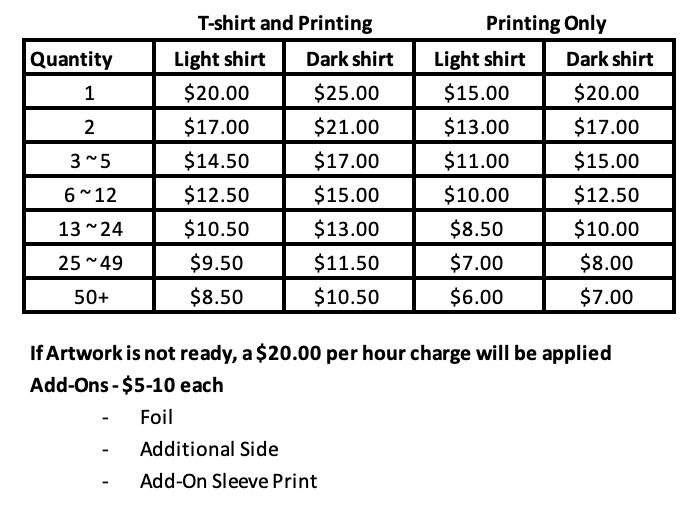
As you can see, your cost of goods sold is minimal compared to the typical selling price for DTG T-shirts, which is great for your ROI.