Sublimation printing on drinkware and other cylindrical or conical products requires the same software, printers, ink, and paper as printing on flat textile and non-textile products. But once the sublimation transfer has been printed, printing on drinkware takes a decisively different route, requiring different equipment and expertise.
The principles of applying the transfer onto the final surface remain the same: pressure, time, and temperature are required for the image to migrate from the carrier paper to the substrate. However, those three variables are delivered by a few very specific tools.
Pressure is provided by first firmly wrapping the transfer around the substrate and taping it down with heat-resistant tape. However, by itself, this is insufficient to result in a crisp image on the mug surface. Additional pressure is required — this either needs to come from a mug press or from a tool called a mug wrap. Along with this pressure, timed heat is delivered by a mug press, a 3D vacuum press, a countertop-type batch oven, or a conveyer-type oven.
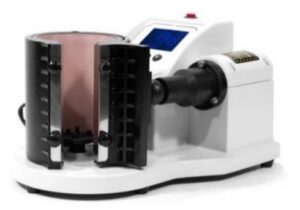
The mug press
The original way to sublimate on a mug is with a mug press. The press consists of a closing/pressure mechanism, wrapping firmly around the substrate. The heat is provided by a heating element which consists of a metal filament sandwiched between two heat-resistant silicone pads.
The advantage of this process is that it is simple (requires just this one tool) and is inexpensive for small, one-off projects. For runs over a dozen, the press becomes quite time-consuming. The three-minute intervals between mugs are too long for the operator to idle but too short to do anything else significant.
Another disadvantage is the lack of versatility. Although there are a few presses on the market that come with a few attachments of varying shapes, mug presses are typically limited to straight-walled 11-oz. to 15-oz. mugs. Swapping between different-shaped attachments — while hot and when available — is cumbersome at best.
Another downside is their heater band. At 400 F, the thin heater band is fragile while being squeezed between the substrate and the metal housing of the press. As a result, heater bands tend to have a short life expectancy. Furthermore, they are not cheap and are seldom easy to replace.
One solution is to separate the pressure action from the heating source. This leads us to the introduction of the mug wrap (see further down).
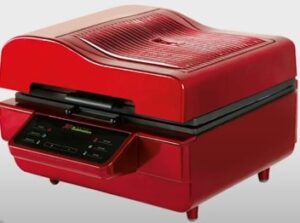
3D vacuum press
The 3D sublimation vacuum press is an all-in-one machine combining vacuum pressure and heat to wrap sublimation transfer paper around curved shapes to permanently fuse the decoration onto any curved surface. The press can be used to customize many types of substrates like sublimation blanks, mugs, latte mugs, cell phone covers, curved plates, etc.
Because of its size, the press is not suited for large production volumes. However, for some irregular surfaces, a vacuum press may be the only current solution on the market for now. Vacuum presses can also handle any drinkware and mugs. However, for the straight-wall or slanted-wall drinkware products, there are more economical and scalable solutions available.
Enter the mug wrap and sublimation ovens.
The mug wrap
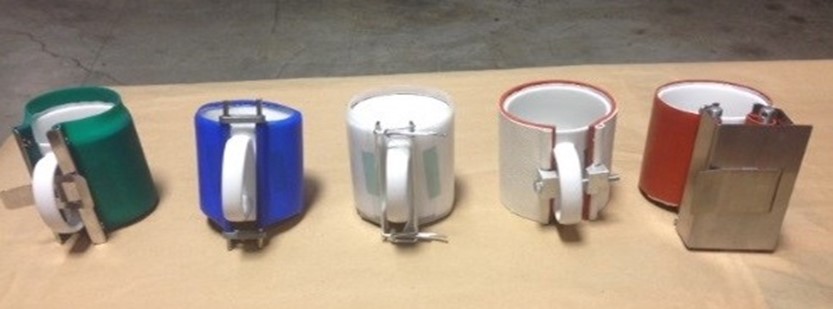
Mug wraps are pressure devices consisting of a clasping mechanism and a silicone pad that wraps and locks around a substrate, providing a close fit. Mug wraps on the market include:
- Tool-less wraps vs. tools-required wraps
- Welded wraps vs. wraps with removable silicone
- Wraps for straight-walled vs. tapered substrates
- Wraps for small, medium, or large substrates
- Variation in silicone quality and durometer
Tool-less vs. tools required
Some wraps will need tools such as drills with special drill bits to open and close the wrap at each cycle, which can lead to overtightening and the mug handle snapping. Some mug wraps may require no tools but are clumsy to open and close. The best choice for a wrap is one that opens and closes easily without additional tools.
Welded wraps vs. wraps with removable silicone
Welded wraps are permanently attached to the steel holding pins or the wrap assembly. This effectively turns the entire wrap into a disposable tool. The welded wrap, although cheaper to acquire, may end up costing more.
Wrap mechanisms with removable silicone can be detached from the silicone. The clasp assembly sustains no wear-and-tear and has a near indefinite life expectancy. The replacement-silicone option may offset a higher initial investment.
Straight wall vs. tapered wall mug wraps
Straight-wall wraps cover mugs with parallel walls. Tapered-wall wraps cover slanted walls. Ideally, the wrap needs to provide about 1/4″ to 3/8″ of overhang over the edges on both sides of the mug to provide a good and firm fit for the transfer and pressure at the edges.
Wraps for small, medium, and large substrates
Most drinkware on the market is the standard 11-oz. or 15-oz. mug, but more variety seems to appear regularly, requiring different size wraps. Sizes vary from small shot glasses to tall travel coolers and from pint glasses to wide dog or cat bowls.
Each shape and size requires a different mug wrap. Any inconsistency in the slanting angle will result in uneven pressure on part of the mug. The wrap’s height needs to be sufficient to cover and even overlap the printing surface. Some companies will custom-manufacture wraps for any non-standard shape.
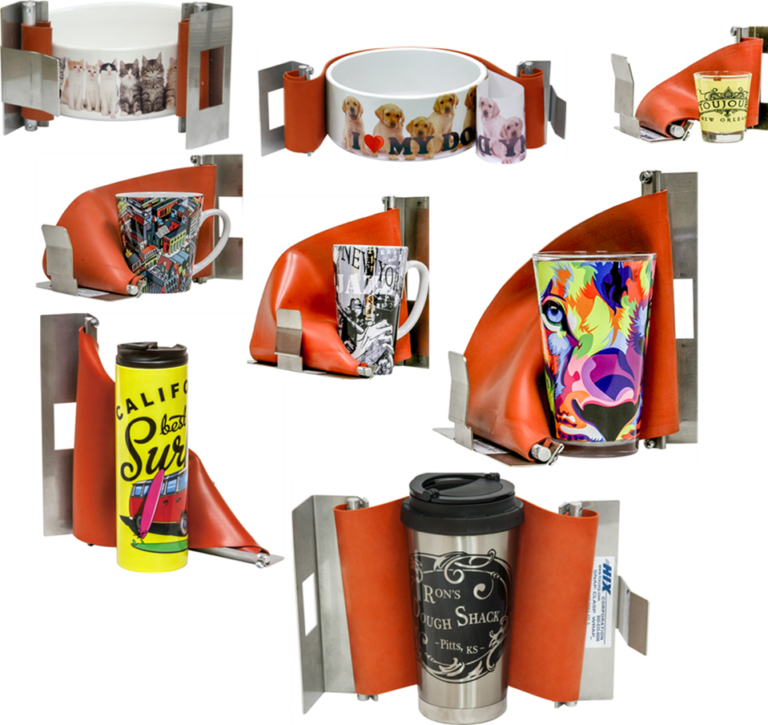
Variation in silicone quality and durometer
The quality of the silicone directly relate to the flexibility and longevity of the wrap. Good quality silicone can last 100-150 cycles. Keep the wraps in a cool, dry place, allow them to cool between uses, and don’t throw them in boxes.
The durometer of the silicone is also important. Too soft, and the wrap will provide insufficient tension. Too hard, and the clasp will be difficult to lock and open. A “Goldilocks” solution provides tension/pressure and user-friendliness/ease of manipulation.
The mug oven
Batch-type or conveyer-type ovens can be small enough to accommodate no more than two to four mugs or large enough to hold as many as 400 mugs at any given time.
A few key features are critical for a quick, complete, and uniform sublimation in an oven:
- Ideally, the oven is a convection-type model. The forced air inside the oven chamber allows for a quick and even heating of the mugs regardless of their precise location inside the oven so that all mugs are equally well and completely sublimated, top-to-bottom and handle-to-handle.
- A quality convection oven features strong airflow and sufficient heating capacity to quickly heat up the mugs as they are placed inside the oven. Convection ovens used in food preparation are generally too small to make the process economically feasible. They mostly are insufficiently powerful to provide the required air velocity or heat recovery speed needed to achieve a quick and even sublimation of all mugs in the oven.
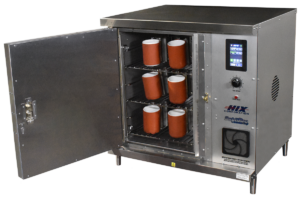
Countertop batch-type sublimation oven
- The equal air distribution inside the oven is even more critical in the case of larger conveyer-belt type oven chambers. Without properly regulated airflow, sublimation will be unfinished, and substrates wasted. A proper temperature differential is within +/- 5 F across the belt and within 15 F top to bottom of any substrate.
- For these types of ovens, accurate belt speed control is also critical so that all drinkware lingers equally long in the oven chamber. Differences in heat quantity will result in differences in color outcomes.
- For the larger conveyer-belt units, an appropriately sized cooling tower is no small luxury — allowing for mugs to be picked off the belt bare-handed and packed into boxes at the exit side of the belt. An integrated cooling facility may be superfluous for a smaller countertop oven, in which case a table fan can easily do the job.
- Since conveyer-belt units can hold many mugs at any given time, the belt will need to be sufficiently strong to support the weight of the drinkware. Do not attempt to place mugs on a standard fiberglass belt of an oven used for screen printing. The belt will be unable to support the weight of the mugs and will rupture. A chain-linked stainless-steel belt with a weight-support capacity of 6 lbs./ft2 is ideal for drinkware. Support reels are needed as well to carry the belt without sagging.
Conveyor-type sublimation oven
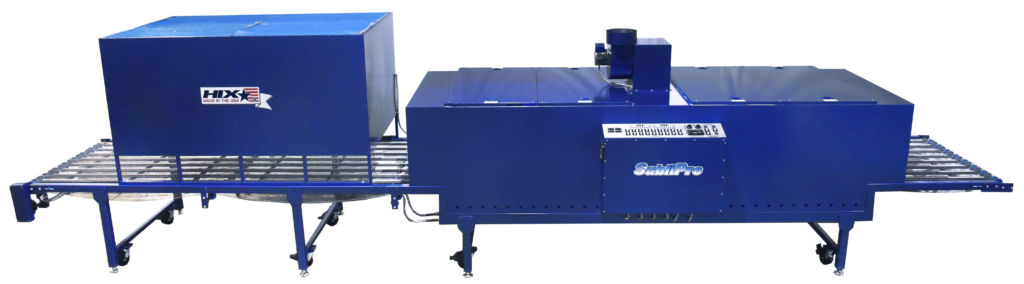
- Customers have a choice between smaller batch-type countertop ovens and larger conveyer-belt ovens. Typically, a customer who has outgrown their mug press will first look at a smaller batch oven because of its increased capacity and labor efficiency. For even larger capacity and efficiency, different sizes of conveyer-belt convection ovens are available.
- Because of the demand-volatility of drinkware during the year, companies often use a combination of ovens side-by-side: a countertop oven for off-peak days combined with a conveyer-belt oven for peak season. Larger companies may have several conveyor units of different capacities placed side-by-side for the same reason.