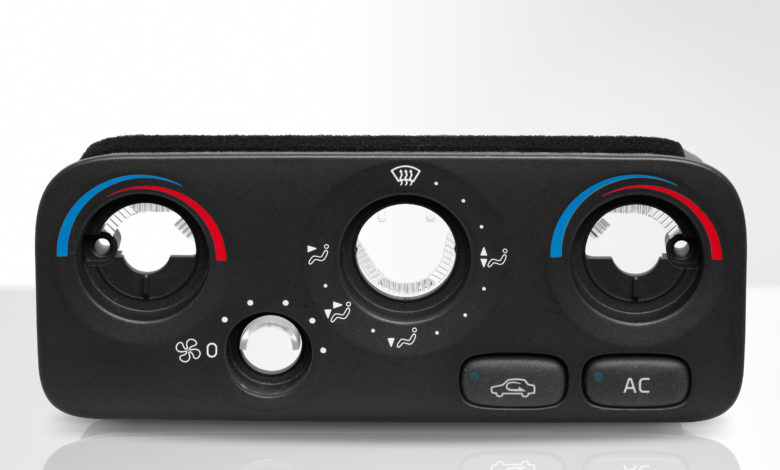
Due to its low cost and high versatility, plastic is a widely demanded material. It is considered enormously efficient due to its material properties such as transparency, flexibility, low weight, and robustness against strain. Since lasers can create durable and high-quality marks, laser technology is the proven method for plastic marking.
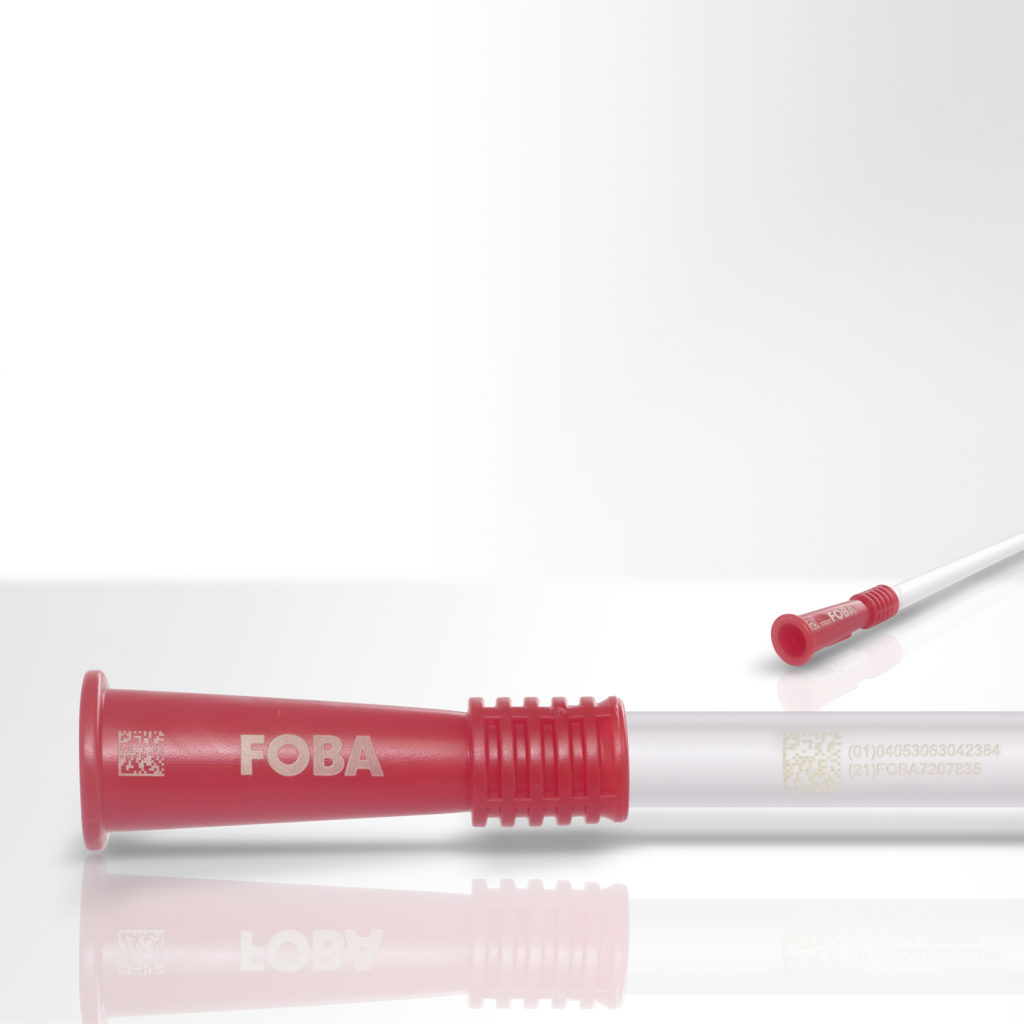
A significant number of plastic applications require direct part marking for device identification purposes. Traceability is the main issue in product defects and recalls (e. g., for automotive parts). But part identification is also crucial for streamlining manufacturing processes throughout the entire production chain. Tracking codes on the product surface should therefore be durable and human- and machine-readable.
In terms of patient safety in the medical industry, plastic marking applies particularly to medical devices used multiple times and reprocessed after each use. Direct marking is then even required by law and regulated by FDA (U.S.) and MDR (EU) regulations, referred to as unique device identification (UDI).
In addition, plastic products are sometimes also marked only for decoration or to increase counterfeit protection. Any requirements for direct part marking can be met for almost any plastic with the help of suitable laser technology.
Methods of plastic marking: Carbonizing, foaming, material removal, or engraving
Depending on the properties of the plastics, CO₂, UV, fiber, and other solid-state lasers are applicable for marking plastics. Since the laser’s thermal energy acts locally and with high precision, the color change achieved is sharply defined, high-contrast, and thus easily legible.
Another advantage of laser marking is its high abrasion resistance. Since the marking is usually created within the material substance, the plastic surface remains smooth and relatively even. This not only has advantages for the durability of the marks but also for product hygiene.
Plastics absorb light best in the ultraviolet (UV laser) and far-infrared (CO₂ laser) range. However, plastics can be laser-optimized by using special additives in the raw material mix. The used additives, fillers, and pigments help to improve the absorption behavior of the plastic.
Additives may facilitate or even enable the employment of versatile fiber lasers (with a wavelength of 1,064 nm) or visible green laser light (532 nm). This leads to best marking results when using the appropriate lasers.
The thermal changes in the material brought about by the laser produce different marking effects. While color changes to light or dark hardly affect the surface structure, melting or evaporation results in structural changes or engraving effects.
On dark plastics, a lighter coloring usually results, while on light plastics, a darker coloring or — in some cases with transparent materials — a lighter marking is produced. The four marking processes to mention when marking plastic are carbonizing, foaming, layer removal, including day-night design, and engraving.