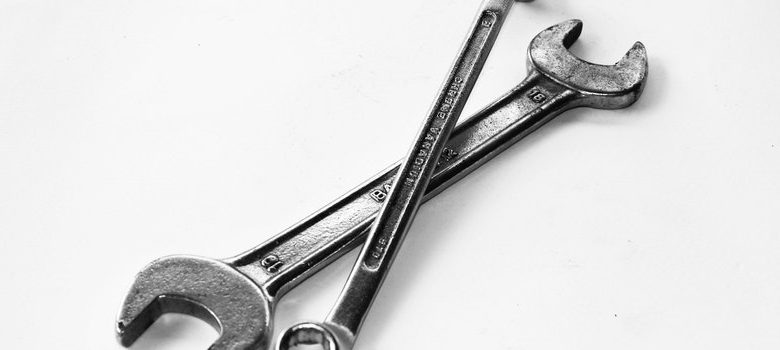
You have put a lot of thought and money into buying your first automatic press, but purchasing is just the first step. Refer to this to-do list to make the installation of your automatic press as painless as possible.
Before Arrival
- Continue your research. Buying the press was part one. Understanding and preparing for any hiccups is part two. Delve deeper into installation issues. This makes your job, as well as the tech’s, easier. Contact the manufacturer about any tips or guidelines they may have, go to seminars in your area, or reach out to printers in your area or through Facebook groups.
- Be clear on the expenses that are included in your setup fees. The technician is there to get the machine working and make sure you understand the functions and operations of the press. Getting the press set up takes an estimated 12-16 working hours. Expect a flat fee for this service. Other fees for the tech include food and lodging. If you need additional time with the tech after the specified amount of time you can expect to pay hourly, which can get very expensive.
- Clear space. For example, a six-color/six-station press takes up 10 feet in diameter. You will also want to allot 2-3 feet of walking room with absolutely no obstructions for yourself and your employees. If you don’t use an auto flash, you need to clear enough space for your flash unit.
- Flooring. Concrete floors are preferred. Wood floors will require additional support to hold the weight of the machine.
- Power. Your electrician will set up your shop’s power. They need to know the specs of the press-amps, is it three-phase, voltage, etc.
- If you have not done this already, upgrade your other equipment to handle the workload of the automatic press. This also includes the purchase of an air compressor. This should be an option given to you by the manufacturer and, as a bonus, they will take care of the routine maintenance of the air compressor for you.
- Invest in the people power. To successfully run an automatic shop, you will need the extra hands.
Arrival
- Scheduling and moving your press is your responsibility. Freight companies have different requirements and costs for delivery. Talk to the freight companies about the best solution for you. Communication is key here. Get a tracking number for your press and know the anticipated delivery date and time range to prepare your shop for arrival.
- The delivery truck delivers. You must do the rest, which includes unloading your press from the truck with a forklift and making sure there’s enough clearance for your press to pass through.
- During the working hours of the tech, their first job is to get the press up and running. Any information you can provide to the tech will save them time. This helps you out because it leaves time at the end of the process for questions and a lesson on operating functions and maintenance needs of your new press.
- Have your 23-inch by 31-inch screens ready to go to run a practice job with the tech, if possible. If you run into any hiccups during the printing process, they can be addressed while the tech is there. If the tech is unavailable to you when you do a test run, you can always call your manufacturer and run the issues by them to get an answer.
Remember that communication and preparation are key for a painless installation. Having a clear understanding of what issues you need to address with the tech, what their responsibilities are, and what your requirements are will help you have an easy time getting your press set up and your shop running smoothly.