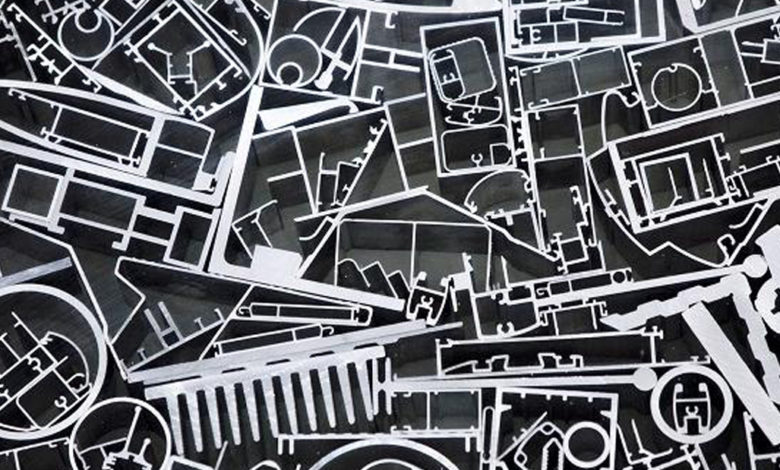
When designing and developing sign systems for indoor usage, I usually try to avoid aluminum extrusions. Not because I don’t like the material; on the contrary, aluminum is amazing. Brushed aluminum is gorgeous, and besides this, it is also affordable, light, and environmentally friendly.
It is just the use of extrusions for smaller signage (like indoor signage) that is not very efficient, and it is hard to fit small parts neatly. There are other materials out there that are much easier to be manufactured and more precise in the assembly process, offering a higher quality of finishing.
However, there is a turning point where it is more logical to make use of aluminum extrusions. For larger signs, it is evident that there is a need for aluminum extrusions because they can offer solid yet light constructions. These extrusions can be invisible as they are just supporting the outer material, or they can also be used to mount the signs efficiently. When they are visible, the anodized versions of them are used, which offer a beautiful finish. Well-known examples where you may have seen these include totem and textile signage.
The extrusions that are visible, though, usually tend to look a bit the same. And there is a danger that the sign maker will use them again to frame ads or images, as I talked about in my article Signs: To Frame or Not to Frame, but this time in a larger size. This practice is limiting creativity and gives less opportunity to stand out from the competition. Apart from that, I noticed that many sign makers are looking for a specific extrusion. It might be a bit different in shape, in the finishing, or just somehow different for the sake of being unique, but still keeping a similar functionality.
So, why not do it yourself? You don’t need to be stuck with the standard available extrusions. The development of your own extrusions is much more accessible than ever before, with far lower minimum order quantities. And let’s be honest: the shape of the extrusion is not really rocket science.
Even though the design might not look complex, it is recommended to hire a professional designer for this, especially if you are using the extrusions for larger installations, and you need separate extrusions or parts to fit perfectly well. Parameters like material tolerance, strength, stability, and many other details will be too difficult to cope with by yourself. But when you look for a designer, make sure they have sufficient experience with extrusions and preferably with signage, as it will save you a lot of time. Be aware that extrusion companies can often offer a great deal of advice and expertise.
So, is it worth it to design and develop your own extrusions? Of course, this depends on the quantity you are using. Many sign makers that I know use only a few extrusions, mostly for hanging lightboxes, totems, and textile signage. However, it can be profitable to develop your own extrusion when the estimated amount of material is around 1,000 kg of aluminum, including the extrusion tools and design. This might seem like a lot, but if you take 1,000 meters of a standard extrusion, you need to manufacture around 160 2m X 1m lightboxes to make it more profitable than buying standard extrusions. For the larger sign makers, this could be just one major assignment.
Plus, making your own is an exciting step in creating a unique product and opportunity to stand out from the crowd, and it could give you a cost reduction in materials.
Last but not least, when looking for partners for your own extrusions, be aware of trading companies that outsource the design, extrusion, and finishing. They usually offer stock for you, but they will always try to push more than you need. You can say that such companies will “release” you from the burden of developing your own extrusion, and there is less to worry about. However, you will not learn the procedure yourself, and you will eventually pay double the price, resulting in zero financial benefits from using those standard extrusions.