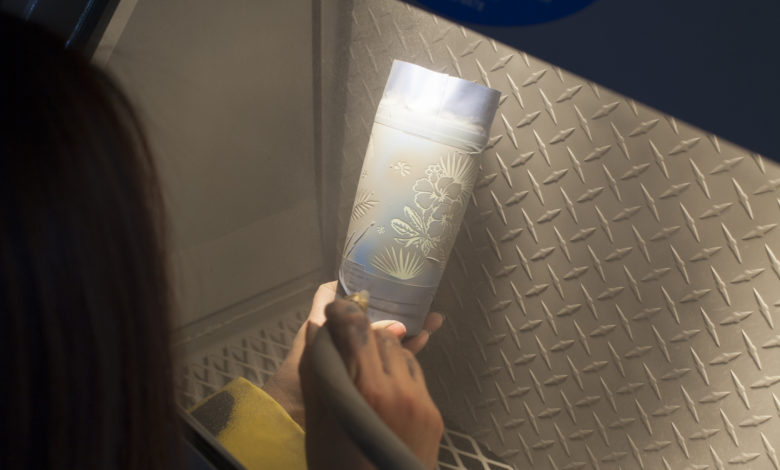
Some of the choices you are faced with if you etch and carve glass include glass beads, beach sand (brown), white crystal silica sand, garnet, aluminum oxide (white, brown, or pink), and silicon carbide (black or green). These materials vary in price from less than $4 per 100 pounds to over $200 per 100 pounds. When you consider that you may use as much as 50-100 pounds or more in an hour in a given blasting job, it becomes evident that you need a little more information before making your purchasing decision.
The best abrasives to use are the ones that are the hardest and have the sharpest, longest lasting corners and edges on the particles. However, those are also the most expensive. To make them worthwhile to use, you have to be able to recapture and reuse them over and over. In recycling the more expensive abrasives, you increase their cost efficiency to the point where they cost less to use on a per hour basis than sand or other cheap materials.
Sand was used for a long time, and rumor has it that there are still some individuals out there who use it (for questionable reasons) for architectural-sized work. I often hear that it’s because it is cheap. That is certainly true, but only on the surface.
Since you can only use sand once in the blasting process because it dulls with use, you continuously have to replace it, which makes it not so cheap in relation to other media that can be recycled. Plus, you can only get sand in 80- or 90-grit size, which is very coarse compared to the 180- to 220-grit abrasives we use today.
Sand works but has a definite effect on the finished piece. Since the particles are so large, you will never be able to blast a completely straight line with sand as an abrasive because the particles bump into each other along any resist edge, creating small skips. This holds true for any larger area as well. These skips create a sparkly look to any surface blasted with sand because there are always small areas of the glass that do not get abraded. One can recognize a work blasted with sand right away by this phenomenon, not to mention the ragged edges of any design element.
But wait, there is more. One of the components of sand is silica, which is also contained in glass. When you blast with sand on glass, a large amount of silica is set free in the dust created. If you do not wear appropriate breathing protection while using sand, you open yourself up to contracting silicosis, an accumulative process over time with eventually fatal results. As coal miners died of black lung, sandcarvers have died of white lung. In many European countries, it is against safety laws to use sand as an abrasive. Here in the U.S., OSHA classifies sand as a hazardous material. I cannot think of one reasonable use for sand as an abrasive for all the above criteria.
Today we have the choice between two commonly used abrasives—silicon carbide and aluminum oxide—that can be recycled and are classified by OSHA as nuisance dust but not as hazardous materials. This chart illustrates both of these abrasives’ common properties and may help you select one over the other.
Abrasive Types and Characteristics |
||
Abrasive Type | Uses | Other Facts |
Aluminum oxide grit sizes: 12-1,500 |
Glass etching, stone blasting, wood blasting, metal finishing, manufacturing sandpaper, grinding wheels | Very hard, tough abrasive that cuts glass quickly.
Major drawback: Generates static electricity, which causes dust to cling to the back of glass being blasted. It makes it hard to see what you are doing if you prefer lighting the glass from the back. Brown is the most common and cheapest. White and pink are available: higher purity and cost but no increase in speed. No free silica. |
Silicon carbide grit sizes: 12-1,500 |
Glass etching, metal finishing, manufacturing sandpaper, grinding wheels, non-skid surfaces (can be used on stone and wood) | Harder than aluminum oxide; it cuts glass faster because it constantly breaks off small pieces, exposing new cutting edges. No static electricity. No free silica.
Creates a “flashlight effect”: small sparks where particles hit the glass, making it easy to see the area being blasted. Black is most common; green is sometimes available and is slightly harder but costs much more. |
Both abrasives are excellent choices. Both materials are hard minerals, with silicon carbide registering a 9.5 on the Mohs hardness scale and the oxide at a 9. The hardest substance, diamond, is a 10.