Heat Management On-Press: Controlling the Variables
Heat management on-press is a crucial variable to understand
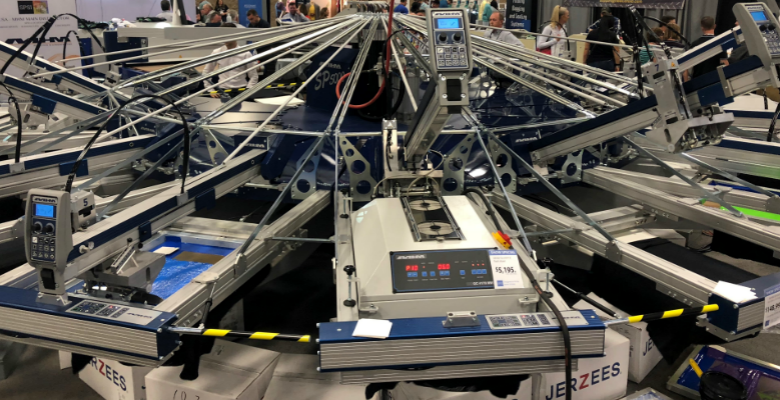
When a statement gets repeated, there is usually a good reason. “Control the variables, and you control the process” is something I’ve heard repeated in many scenarios from screen printing to polymer development.
Heat management on-press is a crucial variable to understand and is one that can easily be cast aside to fit a multicolor print into a smaller press. Depending on which inks you use, a minimal amount of heat is generally required to warm platens for ink curing and the ink itself to achieve the best flow properties. Too much heat in the process can cook inks and shirts alike and affect print attributes by over-curing, migrating, and degrading color.
Sizing your job to the automatic press available is essential in controlling this variable. With some ink systems, a cooling station is a management technique that is almost required to keep your process humming for long production runs. A print-flash-cool order allows you to maintain a minimum platen temperature to maximize flash and production rates without building up excessive heat in platens and inks, leading to the failures mentioned above. This order can also allow for enough time for the ink film to become tack-free and reduce pick-up on the following screen.
When printing with some particular inks and colors, it may be necessary first to print several screens of the same color to build up adequate opacity. Doing so may cause the screens to gang together in a print-flash-print process purely due to limited press space. Printers should aim to minimize this if heat buildup is a concern, especially with inks like HSA and silicone.
Of course, there are times when you want to print wet-on-wet, most notably in process or CMYK printing. When printing an underbase wet-on-wet, you may consider adding extra cooling space after your base flash to ensure the ink is cured enough to overprint. Printing an underbase wet-on-wet is often used to cover the shirt color or control migration. While this print-flash-cool protocol helps to control the variables for ink and fabric, perhaps the most useful practice is the ability to test the ink film for cure while setting up production, as well as checking screen registration. You can do this in an open print head. Often these benefits lead to unintended heat management. However, it’s important to note that this provides a control over your process.
Everything in moderation is another saying to keep in mind. Moderating heat in your printing will help you control the process for success. And remember to keep a data book handy for press setups, so similar or repeat prints can be quickly set up for optimal results.