Preparing Your Building’s Electrical for Automated Screen Printing
Use these tips to determine if your space is up to par
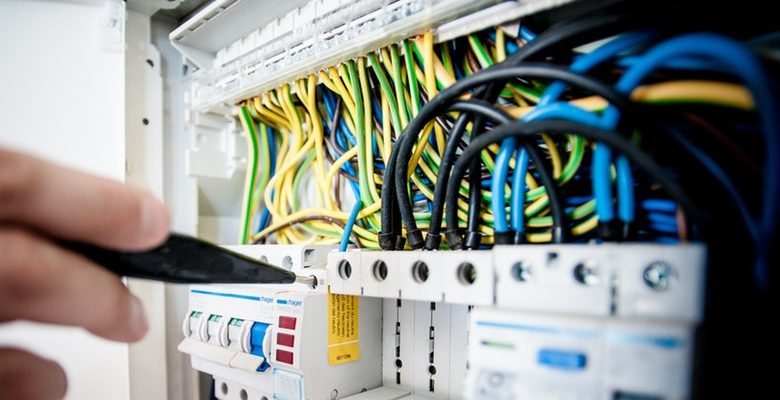
There comes a time when upgrading to larger equipment to keep pace with demand becomes necessary. Particular considerations for this upgrade such as size and capability of machinery, as well as staffing and financial decisions, are apparent. However, one of the most critical and often overlooked factors is the capacity of the building’s electrical power.
First, you want to determine what type of power your facility has. Most buildings will have either single-phase or three-phase power. The difference between these two types of alternating current (AC) electrical systems is an important consideration not just for your current space and new equipment, but also the utility costs you will incur in the future.
Three-phase power will deliver a steadier stream of electricity at a more constant rate than single-phase, which allows for a heavier electrical load to be carried while pulling roughly 40 percent less amperage. This differential will result in higher electrical usage and increased costs on your monthly utility bill if you are running single-phase power. Most commercial spaces will be equipped with three-phase, but it is critical to confirm this with the landlord and your electrician before purchasing equipment. Almost all residential properties will have single-phase power, as only minimal power capabilities are needed to run standard home fixtures and appliances.
The equipment distributor or manufacturer that you are working with will be able to provide you with the maximum amperage requirements for each piece of equipment. Your electrician will need to inspect your breaker box and the new equipment requirements to advise on whether you will need to add more amperage. They will also need to verify your voltage to ensure it meets proper conditions. Running automated equipment at a higher than recommended voltage can damage internal electrical components and cause them to fail. It can also void your warranty on the machine.
Each major piece of equipment may require its own dedicated electrical drop to be wired from the breaker box as most machines will typically not plug into a standard wall outlet. The best case scenario is to wire equipment from the top of the machine because your electrician can run dedicated lines up a wall, across the ceiling, and drop down to the location where the equipment sits. This solution avoids power lines running on the ground, which can be hazardous and impede foot traffic on your production floor.
It is recommended to draw out a birds-eye view of your shop layout, factoring in machine size, working space, walking lanes, and wall proximity to determine where electrical drops will need to be placed from the ceiling to correspond with your floorplan. Below is an example of a shop layout for electrical work.
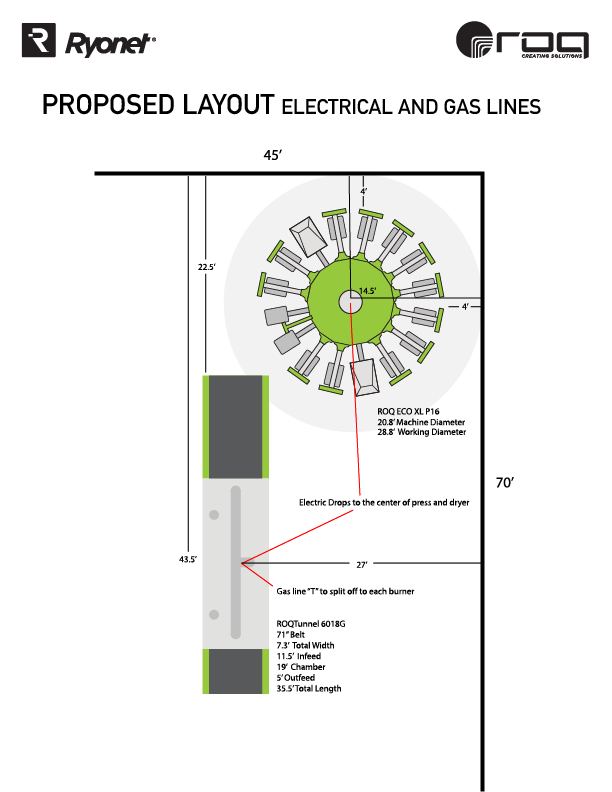
Whether you are just starting to print manually, getting ready to add automated equipment, or are already an auto shop with plans to upgrade or expand in the future, having a full understanding of your building’s power capabilities will be a crucial factor in planning for your next equipment upgrade or expansion.