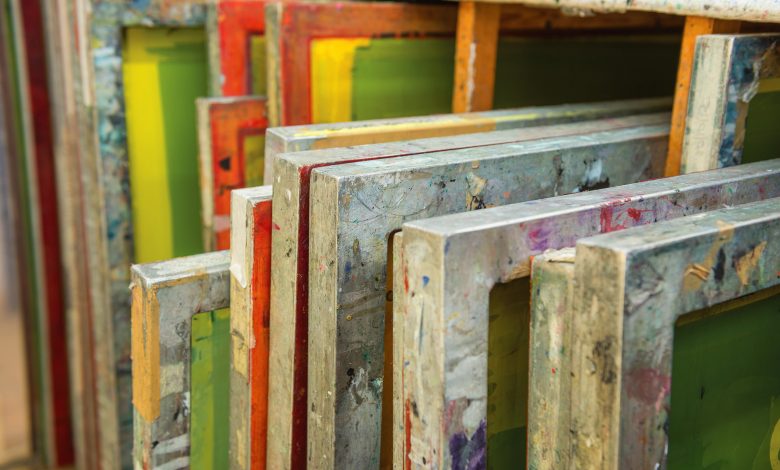
I know I have opened more than one mesh specification sheet and been so impressed with the scope of the information and the “transparency” (to use the currently-PC expression) of the mesh-weavers. I adore the massive amount of data and the level of the detail on each product, but the problem I have had in the past is trying to predict what this abundance of numeric attributes mean to my quality and productivity.
Sometimes the selection process is simple. For example, if we need to print a 65 lpi halftone and want to hold a long tonal range and print all colors at 22.5-degrees, we would want to use a 315/30 L-grade mesh between 20 and 30 N/cm². Alternatively, if we want a beautiful white solid area we might opt for a delicate 100/55, but our example is the toughest one in the mesh selection process, so the mesh will need to accommodate both large area solids and delicate full-range halftones with white ink. The selection process comes when we need to print white ink since the mesh is fundamental in order to balance throughput and quality.
Who’s on first?
If you have read this far in the article, you may wonder if you have a problem, and, if so, if there is a “mesh-solution” in your near future. Abraham Maslow, the creator of the Maslow hierarchy of needs, said, “If all you have is a hammer, the whole world looks like nails.” The first step in the investigation is to determine the primary and secondary causes of your specific issue. In other words, is the problem due to improper mesh selection or not?
In the following table, the left is alphabetized since there is no consistent prioritization (e.g. print buyer to print buyer).
(Charts courtesy the author)
Clearing: The mesh is the foundation for clearing based on its fill-rate and capacity. A high fill-rate and low capacity mesh will exhibit superior clearing, and it will do so at a wider range of static and dynamic tension levels. The blade must fit the mesh and flex based on the ink. The stencil, specifically the EOM will restrict, even inhibit clearing if it is industry typical.
Deposit: The mesh should be selected based on its deposition filling that capacity if the responsibility is of the blade. Although the stencil is often and mistakenly used to regulate deposit, this methodology, propagated by most of the stencil purveyors, comes at terrible costs on-press.
Drape: To clarify, our lexicon uses “hand” which encompasses both surface roughness of the print as well as its ability to fall and fold in the same manner as the garment. In the textile screen-printing business, “hand” means “How does it feel?” Drape is the inverse of deposit and is determined most by the mesh. It is the job of the blade to properly fill the mesh, while the stencil has little to do with the drape.
Edge acuity: This is the sharpness at and squareness of the image edge which is defined primarily by the stencil and supported by the blade which is tasked to properly fill the stencil. Quality edge acuity can only be determined by both stencil and blade.
Ink tack: Is the ratio of how much the ink likes to stick to itself over how much it likes to stick to something else. With rare exceptions, we all want a low-tack ink irrespective of type or color. To facilitate the transfer of inks with a higher tack level, the fill-rate of the mesh should be maximized and the flexion of the blade should be optimized to fit the mesh and apply sufficient shear-stress to the ink.
Matte-down: The primary responsibility to cover the fibers which rise above the plane of the garment is that of the ink. However, the blade which must fit the mesh, flex based on the ink, and apply minimum pressure to the substrate and maximum pressure to the mesh. A high fill-rate and low capacity provide latitude for matte-down, but the stencil provides little benefit and is only effective at a nominal ~3/16″ or smaller.
Opacity: Opacity is the tendency of the white ink to appear white without cast, smooth which is the key to brightness and which buries even the shortest fibers sufficiently below its surface. Opacity is reliant on both “deposit” and “matte-down.”
Resolution: The smallest element which is printable. Positive resolution (think highlight dots) is defined by the stencil but limited by the knuckles of the mesh. Negative resolution (think shadow dots) is defined by the stencil but limited by the area of the mesh opening.
Smoothness: Is the absence of surface roughness which is characteristic of low fill-rate/high capacity mesh, and/or a blade which does not fit the mesh or flexes to provide sufficient shearing forces to fill the mesh to an optimal level.
Note: the type and the fluid dynamics of the white ink is paramount in virtually each of the parameters above. Be forewarned, using the stencil or blade to regulate the deposit is akin to the tail wagging the dog. It won’t work well that way! The mesh and the ink are paired for deposition while the stencil and blade may make minor alterations but only at the expense of throughput or image integrity.
In the times of the ancients
It seems that for decades there have been two camps: the best-looking prints at the highest speed and those in search of an immortal screen because the ones which print slowly and poorly will last nearly forever. The former used “thin ‘S’ threads” (relatively high fill-rate and low capacity) but the strength of the yarns was low and the fabric was barely compressed, so they weren’t very durable. The latter rugged-rug mesh, also known as “thick threads,” had low fill-rates and very high capacity, which made poor prints very slowly but did so forever. Today, we can select a high fill-rate and low capacity screen mesh providing we have a high modulus yarn with sufficient fabric compression to withstand what is literally abuse, on most uncalibrated presses with most tacky or evaporative inks.
Now that we have the mesh
The terms fill-rate and capacity are for comparative use and the table below lists the expectations of a low fill-rate/high capacity mesh compared to a high fill-rate/low capacity mesh. If you are struggling with any of the issues on the right, then you may be a candidate for a mesh upgrade.
If we make the upgrade to a high fill-rate/low-capacity mesh, have a high opacity, highly shear-thinning ink, and then clean the non-image areas and do not clear the mesh, we may need to make other “non-mesh” adjustments which are listed below.
We have learned to think in terms of dynamic versus static screen tension, which means within a relevant range we can compensate for lower tension with blade and press settings. Notwithstanding the static tension should be optimal for conditions, mesh pops (at the perimeter) indicate excessive tension while mesh bursts (at the center) indicates low tension.
Mesh is a crucial part of any quality screen print, but it is how we choose and then work with said mesh that truly affects a prints results and the screen’s longevity.