CNC routers have remained fairly consistent over the past several years, with the biggest innovations happening in the size of router tables offered, the different axes available, and the types of router bits used to carve anything from 3D sculptures and signage to metal parts for the aerospace industry. There’s also a trend toward more automation opportunities. That could mean more advanced software, control systems, or robotics that make it easier for clients to get their projects to the router, cut out the project to exact specifications, and then unload it when the project is completed.
“CNC routing equipment is often one of the most expensive components in a sign shop,” said Kevin Recinos, software product manager for AXYZ Automation. “The machines are expected to run continuously with some shops having two and even three work shifts per day. Being a critical piece of production, the reliability of the machine needs to be a critical factor in the buying decision process.”
Carl Ondracek, president of Computerized Cutters, agreed, saying that there are still a few router manufacturers in the U.S. that build their router tables in-house. “The quality of some of the routers now and the precision is a little better. It always seems to get better as long as companies are using high-quality components. Chinese machines don’t come in with the highest quality components.”
Innovations
Ondracek added that many routers are becoming dual-purpose, meaning they aren’t just router tables anymore. Many come with registration vision systems that allow businesses to easily handle print-to-cut. Vision systems recognize the registration marks on printed products and can easily align the router’s working path based on these markings.
He calls vision systems and oscillating and tangential knife cutting the biggest improvements he has seen in the CNC router industry.
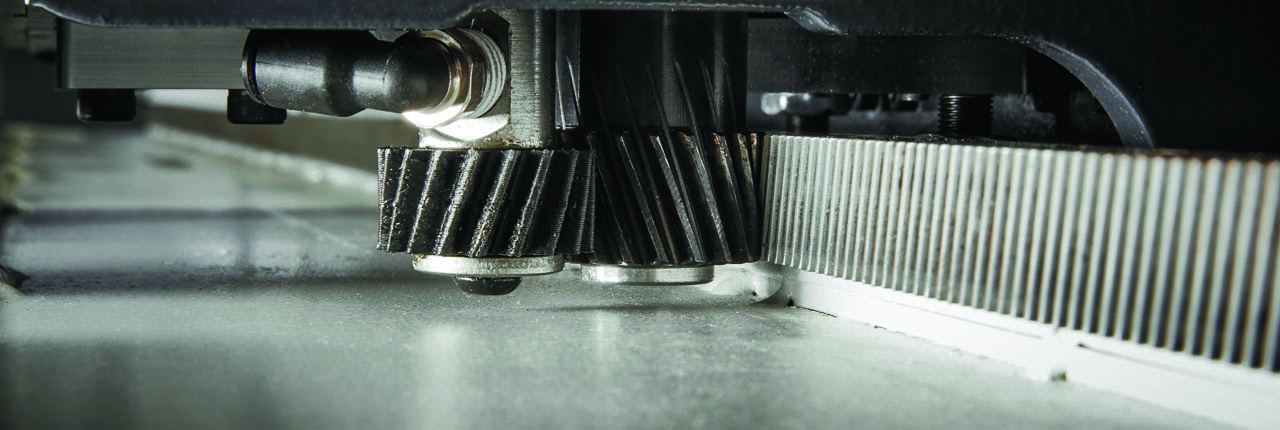
“Back in the day, routers were used to cut plastic, wood, and aluminum. Now they can cut foams and foam boards,” he said. Oscillating knives can cut substrates, such as sign foam, that can’t be cut with a router bit.
“Material handling is becoming the focus for a lot of people,” says Jason Friesen, sign division manager at Laguna Tools.The company has begun to incorporate a new control system in its offerings from FANUC, which is a provider of automation control and robotics.
“We’ve incorporated both their control systems and their robotic arms to do material handling things outside of just traditional CNC routing. We can incorporate the robot to load and unload material and sort parts when they come off the machine,” he said.
Automation
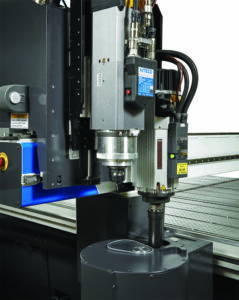
Many large sign shops already utilize CNC routers in their setups and have turned to automation to make their business operate more efficient.
They want a machine to autoload material and unload material. They also want a system that allows them to load a whole series of programs into the machine and leave it to its own devices while it cuts them out, Friesen said.
“For bigger shops doing a lot of production, it is a huge help because they can be virtually hands-off for the whole process. Once the programming is done, you get the materials set up and press go,” he explained.
Four- and five-axis machines are not typically sold in the sign industry, not because they don’t have an application in sign making, but because the cost of entry for sign makers is too high. Many sign shops use routers for one-off projects and the CNC routers with more axes are typically used in production manufacturing where multiples of one item are being cut out quickly.
Laguna sees more interest in these multi-axis machines from the woodworking and aerospace industries because they need them to complete more complex projects.
Water jets are another type of automated machinery for cutting a variety of ferrous and nonferrous metals, foams, woods, and plastics. Fiber-cutting lasers and plasma tables are both used to cut metal.
Along with multi-axis machines, automated tooling is also in high demand. Sign and graphics shops that want to make the process move more quickly are investing in technology that will automatically switch out tools on the router, saving operators time.
CNC routers on the market
When choosing a router, “Signmakers should first consider their application and look at equipment that is designed to process the materials used in their operation. From acrylics to foams, every tool and feature on your CNC equipment will determine the output quality of the part and/or the speed it takes to process the material,” Recinos said. “It’s also important to consider the secondary processes that might be involved if the quality is not to the desired standard.”
Ondracek has been designing router tables for 30 years. He believes that the software systems used in routers now are far more advanced than they were when he first got into the industry. Now, when the artwork is sent to the router, all the operator has to do is input the diameter or size of the bit and whether the project is 2D or 3D.
“The software then creates a tool path depending on the type of router bit, size, and materials it is cutting,” he said. It also can control the speed and depth the router is cutting.
Routers still do what they’ve been doing for decades, and one would think the market was being saturated with them, Ondracek said. “So many routers are still being sold. There is always a need for a router table and as older routers get old, they are not as accurate, so shops replace them and get new ones. Just like the need for printers.”
Ondracek continued, “I think a lot of router manufacturers, since the influx of machines from Asia, are trying to be smarter in how they build routers to bring the price down. They are going to make good router tables but make them more affordable. Other than some of the different cutting heads and tool changers to do more things on the fly, I don’t see that the industry is going to do anything different. It is still a necessary evil for every big sign company,” he said.
Smaller sign shops don’t necessarily have space for a router table, so they farm out that work to larger businesses. Even small router tables made in the U.S. cost a lot more than those coming from China, he said, but the difference is that when there is a problem with a U.S.-built product, it is easier to get help from the manufacturer.
Friesen said that there is a lot of talk right now about the U.S. economy being soft, but he says he doesn’t see it.
“It is a strong economy. People are buying machines; shop owners seem to be busy with work and it is kind of the same, it feels like everyone has the same gripe: they have plenty of work but not enough workers to work for them,” Friesen said. “They are jumping jobs to get to the next pay level. It is not as doom and gloom as certain news stories would have you believe.”